Brushless Motor(BLDC): Construction, Types & Applications
Introduction
A brushless motor is a type of electric motor that has gained increasing popularity in recent years. Which is due to its superior performance and efficiency. Unlike traditional brushed motors that use carbon brushes to deliver electrical current to the rotating armature. Brushless motors utilize an electronic controller to manage the flow of current to the motor windings. This eliminates the need for physical contact between the brushes and the commutator, resulting in reduced friction and wear.
Read More About
One of the main advantages of brushless motors over traditional brushed motors is their increased efficiency. Because they eliminate the need for brushes, brushless motors are able to reduce the amount of energy lost to heat and friction. Which results in a higher power output for a given input. Additionally, brushless motors are typically more reliable. They require less maintenance than brushed motors due to the absence of wear-prone components.
Another advantage of brushless motors is their ability to provide more precise control over motor speed and torque. The electronic controller in brushless motors allows for more accurate control of the motor’s rotation. Which makes them ideal for applications that require high precision and accuracy.
Overall, the use of brushless motors has revolutionized many industries, from aerospace and automotive to robotics and consumer electronics. With their improved performance, efficiency, and reliability, brushless motors are rapidly becoming the go-to choice for a wide range of applications.
Components of Brushless DC Motor
The main components of a brushless DC motor include the rotor, stator, permanent magnets, and electronic commutation system.

Rotor: The rotor of a BLDC motor contains permanent magnets that produce a magnetic field. The rotor rotates as a result of the interaction between this magnetic field and the magnetic field generated by the stator windings.
Stator: The stator of a BLDC motor contains multiple windings. That are arranged in a specific pattern to produce a rotating magnetic field. The stator windings are typically made of copper wire. Which wound around a soft iron core to increase the strength of the magnetic field.
Permanent Magnets: The permanent magnets on the rotor of a BLDC motor produce a magnetic field. That interacts with the magnetic field produced by the stator windings. The strength and orientation of the permanent magnets determine the speed, torque, and efficiency of the motor.
Electronic Commutation System: The electronic commutation system of a BLDC motor controls the timing and sequence of the current to the stator windings. This system typically consists of a sensor or sensorless feedback mechanism, a microcontroller or digital signal processor, and power electronics (transistors or MOSFETs) that switch the current to the windings.
How does a brushless motor work?
A brushless motor operates on the principles of electromagnetic induction, where a rotating magnetic field is created by the interaction of the stator and rotor windings. Unlike traditional brushed motors that rely on carbon brushes to transfer electrical current to the commutator, brushless motors use an electronic controller to manage the flow of current to the motor windings.
The stator of a brushless motor contains a series of stationary coils of wire, which are arranged in a specific pattern to create a magnetic field. The rotor, on the other hand, contains a series of permanent magnets that are arranged in a specific pattern to interact with the stator field.
When an electrical current is applied to the stator coils, a magnetic field is created that rotates around the motor. The magnetic field generated by the stator interacts with the magnetic field generated by the rotor, causing the rotor to rotate.
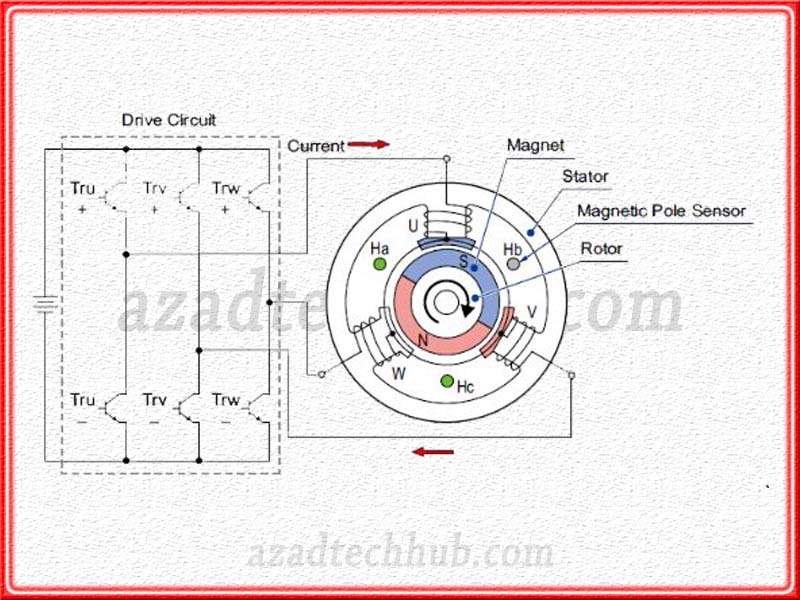
The electronic controller used in brushless motors manages the flow of current to the stator coils, ensuring that the magnetic field is generated in the correct sequence to maintain rotation. This eliminates the need for physical contact between the brushes and commutator, resulting in reduced friction and wear.
Where to Buy?
[wptb id=11142]Block Diagram Representation
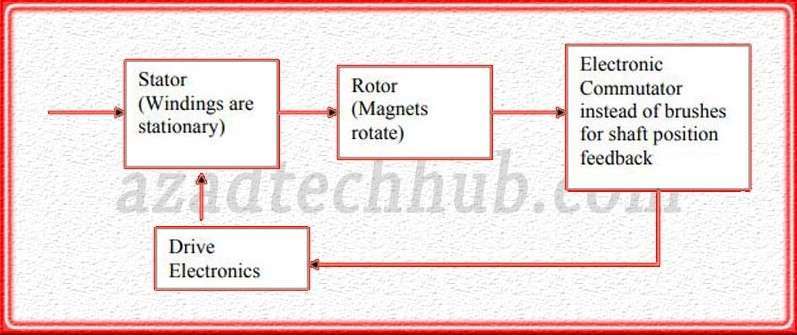
Compared to traditional brushed motors, brushless motors offer several advantages. First and foremost, they are more efficient, as they eliminate the energy lost to friction and heat caused by the brushes. Brushless motors also tend to be more reliable and require less maintenance due to the absence of wear-prone components.
In addition, brushless motors offer greater control over motor speed and torque, thanks to the electronic controller. This allows for greater precision and accuracy, making them ideal for applications that require high performance and precision.
Because they outperform conventional brushed motors in terms of performance, efficiency, and dependability, brushless motors have generally grown in popularity in recent years.
As technology continues to advance, it is likely that brushless motors will become even more widespread in a wide range of applications.
Types of brushless motors
There are several different types of brushless motors available on the market today, each with its own unique characteristics and benefits. Two of the most common types are outrunner and inrunner motors.
Outrunner motors
Outrunner motors, also known as external rotor motors, are a type of brushless motor that are commonly used in a variety of applications. With their large cylindrical rotor that surrounds the stator, outrunner motors provide several advantages over other types of motors, including high torque, smooth operation, and low maintenance.
One of the primary advantages of outrunner motors is their high torque output. The large rotor size allows for a greater surface area for the magnetic field to interact with the stator, resulting in a greater amount of torque being produced. This makes outrunner motors ideal for applications that require high torque output, such as electric bikes, scooters, and large propellers.
Advantages & Disadvantages of Outrunner motors
In addition to their high torque output, outrunner motors also provide smooth operation. Because the rotor is located on the outside of the motor, there is less vibration and noise generated during operation. This makes outrunner motors ideal for applications that require quiet and smooth operation, such as camera gimbals and robotic arms.
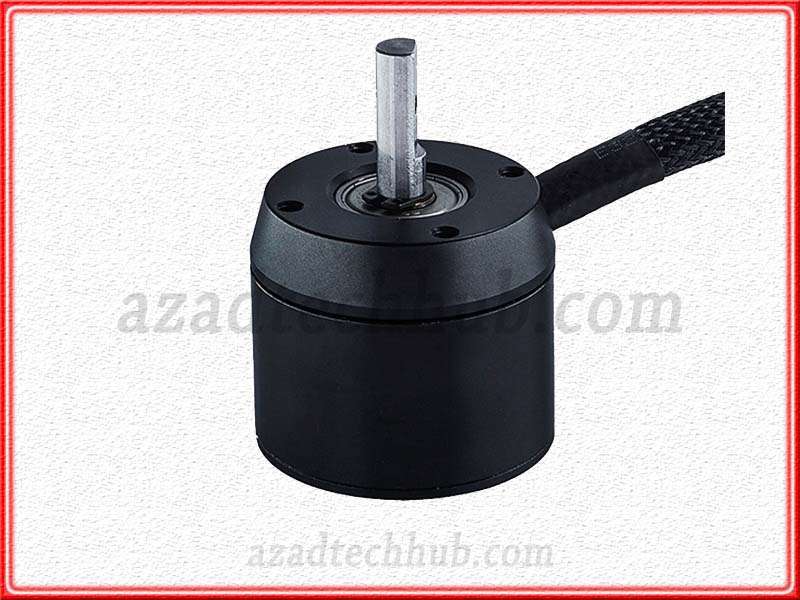
Outrunner motors also require less maintenance than other types of motors. Because there are no brushes or commutators to wear down, there is less chance of mechanical failure. This makes outrunner motors ideal for applications that require high reliability and low maintenance, such as industrial automation and medical equipment.
Another advantage of outrunner motors is their ability to generate a large amount of heat without overheating. The large rotor size and efficient cooling mechanisms allow for efficient heat dissipation, which helps to prevent damage to the motor and increase its lifespan.
However, there are also some disadvantages to using outrunner motors. One of the main drawbacks is their relatively low maximum speed. Because the rotor is located on the outside of the motor, it is limited in its ability to spin at high speeds. This makes outrunner motors less suitable for applications that require high speeds, such as RC airplanes.
In conclusion, outrunner motors provide several advantages over other types of motors, including high torque, smooth operation, and low maintenance. While they may not be suitable for all applications, their unique design and performance characteristics make them ideal for a wide range of industrial, commercial, and hobbyist applications.
Inrunner motors
Inrunner motors, also known as internal rotor motors, are a type of brushless motor that are commonly used in a variety of applications. With their small, cylindrical rotor located inside the stator, inrunner motors provide several advantages over other types of motors, including high speed, compact size, and low weight.
One of the primary advantages of inrunner motors is their high speed output. The small rotor size allows for a greater RPM range and faster acceleration, making them ideal for applications that require high speed output, such as drones, small electric vehicles, and RC airplanes.
In addition to their high speed output, inrunner motors also provide a compact and lightweight design. The small rotor size and location within the stator allow for a smaller overall motor size and weight, making them ideal for applications where space and weight are limited, such as small drones and portable devices.

Advantages & Disadvantages of Inrunner motors
Inrunner motors also provide precise control and responsiveness, making them ideal for applications that require accurate and quick movements, such as robotics and industrial automation. This is due to their efficient magnetic field generation, which allows for precise and quick adjustments in motor speed and torque.
However, there are also some disadvantages to using inrunner motors. One of the main drawbacks is their lower torque output compare to outrunner motors. The small rotor size and location within the stator limit the amount of torque that can generate, makes them less suitable for applications that require high torque output.
Another disadvantage of inrunner motors is their lower efficiency at high loads. The small rotor size and high speed output can lead to increased heat generation and lower overall efficiency, which can limit their use in applications that require high continuous load capacity.
In short, inrunner motors provide several advantages over other types of motors, including high speed, compact size, and precise control. While they may not be suitable for all applications, their unique design and performance characteristics make them ideal for a wide range of industrial, commercial, and hobbyist applications.
While outrunner and inrunner motors each have their own unique strengths and weaknesses, both types of brushless motors offer significant advantages over traditional brushed motors. By eliminating the need for brushes and commutators, brushless motors are able to provide increased efficiency, reliability, and performance for a wide range of applications.
When selecting a brushless motor, it is important to consider the specific requirements of the application in question. Whether you need high torque, high speed, or a combination of both, there is likely a brushless motor available that will meet your needs and provide reliable, efficient performance for years to come.
Applications of Brushless Motor
Industries across the board rely on the numerous benefits of brushless motors. Aerospace, automotive, and robotics are just a few examples of industries. Where brushless motors employ for their superior performance and efficiency.
In the aerospace industry, brushless motors power a range of critical systems, including propulsion systems, landing gear actuators, and control surfaces. With their high power-to-weight ratio and high efficiency, brushless motors are the ideal choice for meeting the demands of this industry. They offer reliable and efficient operation, which is essential for space exploration and satellite missions.
The automotive industry also benefits from the use of brushless motors. They function in electric power steering systems, hybrid and electric vehicles, and braking systems, among other applications. Brushless motors provide excellent power density and efficiency, which translates to better fuel economy and lower emissions. They also require less maintenance, resulting in lower costs over the life of the vehicle.
Robotics is another industry where brushless motors employ. They power robots used in manufacturing, assembly, and logistics, among other applications. With their precise control and high torque output, brushless motors enable robots to perform tasks with speed and accuracy. They also offer a longer lifespan and require less maintenance compared to traditional brushed motors.
Overall, the benefits of brushless motors make them a versatile and reliable solution for numerous industries. They offer superior performance, efficiency, and durability, which translate to cost savings and improved productivity in a wide range of applications.
Advancements in Brushless Motor Technology
Advancements in brushless motor technology have led to significant improvements in their efficiency and performance, making them an increasingly attractive option for a wide range of applications. Here are some recent advancements in brushless motor technology that are making waves in the industry.
One of the most significant advancements is the development of improved motor control algorithms, such as field-oriented control (FOC). FOC enables brushless motors to achieve higher efficiency and better performance by controlling the current and voltage applied to the motor in a more precise and efficient manner.
Another key development is the use of new materials for the construction of brushless motors. For example, the use of high-performance magnets made of rare earth materials like neodymium, samarium cobalt, and dysprosium has resulted in significant improvements in motor efficiency and power output.
Advancements in sensor technology have also played a significant role in the development of brushless motors. The use of sensors like Hall effect sensors and encoders has enabled more precise control of the motor’s speed and position, leading to improved efficiency and performance.
Furthermore, the integration of brushless motors with advanced control systems and communication protocols has led to improved automation and reliability. For example, brushless motors can now connect to industrial networks, enabling real-time monitoring and control of motor performance.
Overall, these recent advancements in brushless motor technology are transforming the way they are used in a variety of applications. With higher efficiency, improved performance, and greater reliability, brushless motors are becoming an increasingly attractive option for industries looking to improve their productivity and reduce their environmental impact.
Selecting the right brushless motor
Selecting the right brushless motor for a specific application can be a challenging task, but taking the time to carefully consider key factors can make all the difference. Here are some important factors to consider when choosing a brushless motor:
Power requirements: The first step in selecting a brushless motor is to determine the power requirements of the application. This includes the required torque, speed, and power output. It is important to select a motor that can meet these requirements without overloading or underperforming.
Motor size: The size of the motor is also an important consideration. It should be small enough to fit into the space available, yet powerful enough to meet the application’s power requirements.
Operating environment: The operating environment of the motor is another crucial factor. Consider the temperature, humidity, and vibration levels. That the motor exposes to, and select a motor that can operate reliably under those conditions.
Cost: The cost of the motor is also an important consideration. Determine the budget for the project and select a motor that meets the power and size requirements within that budget.
Efficiency: The efficiency of the motor is another key factor to consider. Higher efficiency motors consume less power and generate less heat, resulting in cost savings and longer lifespan.
Control options: Finally, consider the control options available for the motor. Does it have the necessary sensors and control systems to provide precise control of speed and position? Can it integrate with existing control systems in the application?
Conclusion
By considering these key factors, it is possible to select the right brushless motor for a specific application. It is important to carefully evaluate the motor’s specifications and compare them to the requirements of the application before making a final decision.
Follow us on LinkedIn”Electrical Insights” to get the latest updates in Electrical Engineering. You can also Follow us on LinkedIn and Facebook to see our latest posts on Electrical Engineering Topics.
Worth Read Posts
- Ultrasonic Motor: A Comprehensive Overview
- Servo Motors: High-Precision Control in Modern Technology
- Arduino Stepper Motor Projects: A Quick Guide
- Induction Motor: Important Types, Construction & Working
- Wound Rotor Induction Motor: Working & Important Applications
- Squirrel Cage Induction Motor: Working and Best Applications
- Brushless Motor(BLDC): Construction, Types & Applications
- Stepper Motor Position Control with Arduino: A Quick Guide