Transformers: Important Types, Features & Components
Introduction
Welcome to our comprehensive introduction to transformers in electrical engineering, where we explore the fundamental role and significance of transformers in this field. Transformers, the essential devices in power transmission and distribution systems, play a pivotal role in ensuring efficient and reliable electricity supply.
Table of Contents
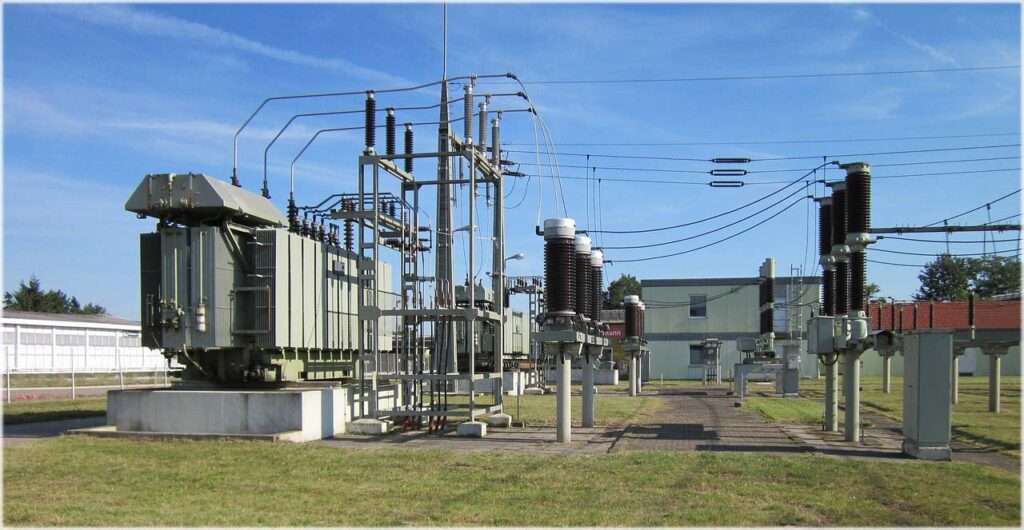
In this article, we will delve into the world of transformers, examining their working principles, applications, and the transformative impact they have on electrical power systems. Whether you’re a student, a professional engineer, or an enthusiast seeking to expand your knowledge of “transformers,” this article will provide you with valuable insights into their importance and applications. So, let’s embark on this enlightening journey into the world of transformers and uncover how they contribute to powering our modern society.
components of transformers
Understanding the components of transformers is essential for gaining insight into their functioning and design in electrical circuits. Transformers consist of several key elements that work together to enable efficient voltage transformation. In this article, we will explore the “components of transformers,” examining their roles, characteristics, and the crucial contributions they make to electrical circuits.
Here is a list of the main components of a transformer:
- Core: The core is typically made of laminated steel sheets and provides a low-reluctance path for the magnetic flux generated by the windings. It facilitates efficient energy transfer and helps reduce losses.
- Primary Windings: The primary windings are coils of insulated copper or aluminum wire that receive the input voltage and generate a changing magnetic field.
- Secondary Windings: The secondary windings are another set of coils that are wound around the core alongside the primary windings. They induce a voltage in response to the changing magnetic field created by the primary windings.
- Insulation System: The insulation system includes insulation materials and structures that electrically separate the primary and secondary windings and prevent electrical breakdown.
- Tank or Enclosure: The tank or enclosure houses the core and windings, providing mechanical support, protection, and insulation for the internal components of the transformer.
- Tap Changers: Tap changers allow for adjusting the voltage ratio by changing the connection points on the windings. They provide flexibility in voltage regulation and accommodating varying load conditions.
- Cooling System: Transformers may incorporate various cooling methods to dissipate heat generated during operation. This can include natural convection, forced air cooling, or liquid cooling using oil or water.
- Protective Devices: Transformers may include protective devices such as fuses, circuit breakers, and surge arresters to safeguard against overcurrents, short circuits, and voltage surges.
- Bushings: Bushings are insulating devices that connect the windings to external circuits. They provide electrical insulation and support for the incoming and outgoing connections.
- Breather: Transformers may feature a breather, which is a device that filters and regulates the exchange of air between the transformer and its surroundings, preventing moisture and contaminants from entering the system.
- Grounding System: Transformers typically have a grounding system to ensure electrical safety and protect against electrical faults. This system provides a safe path for fault currents to flow in the event of a ground fault.
- Monitoring and Control Devices: Advanced transformers may incorporate monitoring and control devices such as temperature sensors, pressure gauges, and on-load tap changers for monitoring and adjusting transformer parameters.
These are the main components of a transformer, and each plays a critical role in the transformer’s operation and performance.
core of a transformer
The core of a transformer is a crucial component that plays a vital role in its functioning and efficiency. It serves as a pathway for the magnetic flux generated by the primary winding, facilitating the efficient transfer of energy from the primary side to the secondary side. The core is typically made of laminated steel sheets to reduce eddy current losses and improve the overall performance of the transformer. Let’s explore the core of a transformer and its functions in more detail.
- Magnetic Flux Conduction: The primary function of the core is to provide a low-reluctance path for the magnetic flux generated by the primary winding. When an alternating current flows through the primary winding, it creates a changing magnetic field that induces a voltage in the secondary winding. The core ensures that the magnetic flux lines produced by the primary winding remain confined within the core, thereby enhancing the efficiency of energy transfer.
- Reduction of Reluctance: The core material, typically laminated steel, offers high magnetic permeability. This property enables the core to reduce the reluctance of the magnetic circuit. Lower reluctance means a lower opposition to the magnetic flux flow, allowing the magnetic field lines to flow easily through the core and minimizing the losses associated with magnetic resistance.
- Minimization of Eddy Current Losses: The core is constructed using thin laminated steel sheets that are insulated from one another. This lamination reduces the circulation of eddy currents within the core, minimizing eddy current losses. Eddy currents are induced currents that circulate within conductive materials when exposed to a changing magnetic field. By using laminations, the transformer’s core reduces these currents and the associated heat generated, improving the overall efficiency of the transformer.
- Reduction of Hysteresis Losses: Hysteresis loss occurs due to the magnetic properties of the core material. When the magnetic field in the core alternates, the magnetic domains within the material repeatedly align and realign, resulting in energy losses. Using materials with low hysteresis properties, such as specifically formulated silicon steel or amorphous metal alloys, helps reduce hysteresis losses in the core and improves the overall efficiency of the transformer.
- Support and Protection: The core provides mechanical support and protection for the windings within the transformer. It helps maintain the structural integrity of the transformer, ensuring that the windings are properly aligned and protected from external factors such as vibrations, physical stress, and moisture.
The core of a transformer serves essential functions in facilitating the efficient transfer of energy from the primary winding to the secondary winding. It provides a low-reluctance pathway for the magnetic flux, reduces losses due to eddy currents and hysteresis, and offers mechanical support and protection for the windings. By employing laminated steel or specialized core materials, transformers can achieve high efficiency and optimal performance in various electrical applications.
primary winding and secondary winding of Transformer
The primary winding and secondary winding are two essential components of a transformer that work in tandem to facilitate the efficient transfer of electrical energy. Each winding has a specific function in the operation of the transformer. Let’s explore the functions of the primary and secondary windings in more detail:
Primary Winding: The primary winding is connected to the input voltage source, typically the power supply. Its main function is to receive the alternating current (AC) from the source and generate a magnetic field. When the AC current flows through the primary winding, it creates a changing magnetic field that links with the core. This changing magnetic field induces a voltage in the secondary winding.
Secondary Winding: The secondary winding is connected to the load or the device that requires a different voltage level than the input source. Its primary function is to receive the magnetic field generated by the primary winding and convert it back into an electrical voltage. When the changing magnetic field from the primary winding links with the secondary winding, it induces a voltage in the secondary winding proportional to the turns ratio of the transformer.
The ratio of the number of turns in the primary winding to the number of turns in the secondary winding determines the voltage transformation ratio of the transformer. For a step-up transformer, where the secondary voltage is higher than the primary voltage, the secondary winding has more turns than the primary winding. Conversely, for a step-down transformer, the secondary winding has fewer turns than the primary winding, resulting in a lower secondary voltage.
The secondary winding delivers the transformed voltage to the load or the electrical circuit connected to it. It enables the transfer of electrical energy from the primary side to the secondary side with minimal losses. The secondary winding ensures that the load receives the appropriate voltage level required for its operation.
Overall, the primary winding and secondary winding of a transformer work together to facilitate the conversion and transfer of electrical energy. The primary winding generates the changing magnetic field, while the secondary winding receives this field and converts it back into an electrical voltage suitable for the load. Through electromagnetic induction, the windings enable efficient voltage transformation in the transformer, making it a vital component in various electrical applications.
insulation system in a transformer
The insulation system in a transformer plays a critical role in ensuring the safe and reliable operation of the device. It comprises insulation materials and structures that electrically separate the primary and secondary windings and prevent electrical breakdown. The insulation system performs several important functions, which are essential for the overall performance and longevity of the transformer. Let’s explore the functions of the insulation system in more detail:
Electrical Isolation: One of the primary functions of the insulation system is to provide electrical isolation between the primary and secondary windings. This insulation prevents direct contact between the windings, which may have different voltage levels, and helps ensure that electrical energy is transferred only through electromagnetic induction. By maintaining proper electrical separation, the insulation system prevents short circuits and protects against electrical faults.
Dielectric Strength: The insulation system must have a high dielectric strength, which refers to its ability to withstand high voltages without breaking down. Transformer windings are subjected to significant voltage stresses, and the insulation material must be capable of withstanding these stresses without allowing current leakage or arcing. A robust insulation system helps maintain the integrity of the electrical insulation, preventing electrical breakdown and ensuring reliable performance.
Thermal Insulation: Transformers generate heat during operation due to the electrical losses in the windings and core. The insulation system provides thermal insulation, which helps manage and dissipate the heat effectively. Proper insulation materials and structures are selected to minimize heat transfer between the windings and the core, ensuring that the transformer operates within safe temperature limits. Effective thermal insulation helps prevent overheating, which can lead to insulation degradation or failure.
Mechanical Support: The insulation system also provides mechanical support for the windings. It helps hold the windings in place and maintains the required spacing and alignment between the primary and secondary coils. This mechanical support prevents the windings from moving or vibrating excessively, reducing the risk of insulation damage and ensuring the long-term stability of the transformer’s internal components.
Protection Against Contaminants: The insulation system acts as a barrier that protects the windings from external contaminants such as moisture, dust, and chemical substances. These contaminants can degrade the insulation properties, leading to insulation breakdown and reduced performance. The insulation system, along with the transformer’s tank or enclosure, helps create a sealed environment, safeguarding the windings and ensuring their reliability over time.
Electrical Safety: The insulation system contributes to the overall electrical safety of the transformer. It helps prevent electrical shocks by providing insulation between the live components and any exposed conductive parts. The insulation system also assists in the safe operation and maintenance of the transformer, allowing technicians to work on or around the transformer without risk of electrical hazards.
In summary, the insulation system in a transformer plays a vital role in ensuring electrical isolation, maintaining dielectric strength, providing thermal insulation, offering mechanical support, protecting against contaminants, and enhancing electrical safety. By selecting appropriate insulation materials and implementing sound insulation design principles, the insulation system ensures the reliable and safe operation of the transformer in various electrical applications.
What are Tap Changers?
Tap changers are devices used in transformers to vary the turns ratio of the windings and adjust the output voltage level. They are designed to change the connection points on the winding to tap into different portions of the coil, allowing for voltage regulation and accommodating varying load conditions. Tap changers enable transformers to deliver a consistent and stable output voltage even in the face of fluctuations in the input voltage or changes in the load.
The main function of tap changers is to modify the effective turns ratio of the transformer, thereby altering the voltage ratio between the primary and secondary windings. This adjustment is achieved by connecting the tap changer to specific taps or connection points along the winding.
There are two main types of tap changers commonly used in transformers:
On-Load Tap Changers (OLTC): On-load tap changers are designed to change the taps while the transformer is energized and under load. This type of tap changer allows for seamless adjustment of the voltage output without interrupting the power supply. On-load tap changers are often employed in applications where continuous voltage regulation is required, such as in power distribution networks or in transformers serving large industrial loads.
Off-Circuit Tap Changers (OCTC): Off-circuit tap changers, as the name suggests, require the transformer to be de-energized before changing the tap position. This type of tap changer is typically used in situations where the load can be temporarily disconnected, such as in small distribution transformers or certain industrial applications. Off-circuit tap changers are less complex and generally more economical than on-load tap changers.
Tap changers are usually controlled by a regulating device that monitors the output voltage and determines when a tap change is required. The regulating device may be manually operated or automated, depending on the application and the desired level of control.
By adjusting the tap position, tap changers allow transformers to compensate for voltage variations in the power system, maintain a stable output voltage, and ensure that the load receives the appropriate voltage level. They are an essential component for voltage regulation in electrical networks, enabling efficient and reliable operation of the transformer under different operating conditions.
Purpose of Bushings in a Transformer
In a transformer, a bushing is an insulating device that provides a means of connecting the internal windings to the external electrical system. It serves as a transition point between the internal components of the transformer and the external conductors or equipment, allowing for safe and reliable electrical connections.
The main functions of bushings in a transformer are as follows:
Electrical Insulation: The primary function of a bushing is to provide electrical insulation between the internal winding conductors and the external conductors. It prevents electrical current from flowing directly between the transformer windings and the surrounding environment or connected equipment. By ensuring proper insulation, bushings help prevent electrical breakdowns, short circuits, and other electrical faults.
Mechanical Support: Bushings provide mechanical support and stability to the internal winding connections. They help secure the conductors in place and maintain the desired spacing and alignment between the windings. This support helps prevent excessive movement or vibration of the windings, ensuring the long-term reliability and performance of the transformer.
Voltage Grading: Bushings are designed to handle the voltage stresses associated with the transformer’s operating voltage. They have specific insulation properties to withstand high electrical voltages without breakdown. Bushings are designed and graded according to the voltage levels of the transformer, ensuring that the insulation can handle the voltage differentials and gradients without compromising safety or performance.
External Connection Point: Bushings provide a convenient and safe point of connection for external conductors or equipment. They have terminals or connectors that allow for the connection of cables, busbars, or other electrical components. The external conductors can be connected to the bushing terminals, enabling the transfer of electrical power to or from the transformer.
Protection Against Contaminants: Bushings help protect the internal winding connections from external contaminants, such as moisture, dust, or chemical substances. They provide a sealed interface between the internal and external environment, safeguarding the insulation system and preventing the ingress of harmful substances that could degrade the insulation or cause insulation breakdown.
Grounding: Some bushings may also incorporate grounding provisions. These bushings have an additional terminal or connection point specifically designated for grounding purposes. They provide a safe and reliable path for fault currents to flow in the event of a ground fault, enhancing the overall electrical safety of the transformer.
Overall, bushings in a transformer serve as critical components that provide electrical insulation, mechanical support, voltage grading, external connection points, and protection against contaminants. They play a crucial role in maintaining the integrity and performance of the transformer, ensuring safe and reliable operation in various electrical applications.
Function of Breather in Transformer
The function of a breather in a transformer is to regulate the exchange of air between the transformer’s internal components and the external environment. It is a device that helps maintain the dryness and cleanliness of the air inside the transformer tank, preventing moisture and contaminants from entering the system. The breather plays a crucial role in preserving the insulation system and ensuring the efficient operation of the transformer.
Here are the main functions of a breather in a transformer:
Moisture Control: One of the primary functions of a breather is to control the moisture content in the air that enters the transformer. Inside the transformer, the windings and other components are insulated with materials that can be sensitive to moisture. Moisture can degrade the insulation properties, leading to reduced performance and potentially causing electrical breakdown. The breather contains desiccant materials, such as silica gel, that absorb moisture from the air passing through it, helping to maintain dry conditions inside the transformer.
Contaminant Filtration: A breather is equipped with filters or screens that trap and remove contaminants present in the air. Dust, dirt, and other particles can accumulate on the transformer’s internal components, potentially causing insulation deterioration or affecting the transformer’s performance. The breather’s filtration system helps prevent these contaminants from entering the transformer, keeping the internal environment clean and extending the lifespan of the insulation system.
Pressure Equalization: The breather assists in equalizing the pressure inside the transformer tank with the external atmospheric pressure. As the transformer operates, temperature variations cause the internal air volume to expand and contract, resulting in pressure changes. The breather allows for the exchange of air with the external environment, preventing pressure differentials that could potentially damage the transformer’s seals or compromise its structural integrity.
Visual Indication: Some breathers are designed with visual indicators, such as color-changing silica gel or pressure gauges, to provide a visual indication of the breather’s condition. These indicators help monitor the saturation level of the desiccant material or detect pressure imbalances, enabling timely maintenance and replacement of the breather when necessary.
By maintaining dry and clean conditions inside the transformer, the breather helps preserve the insulation system, prevent moisture-related issues, and ensure the efficient and reliable operation of the transformer. It is an essential component that contributes to the overall longevity and performance of the transformer. Regular monitoring and maintenance of the breather are crucial to ensure its proper functioning and effectiveness in protecting the transformer.
function of grounding system
The grounding system in a transformer serves several important functions to ensure electrical safety and protect the transformer and its surrounding environment. Here are the main functions of the grounding system:
Personal Safety: The primary function of the grounding system is to provide a safe path for fault currents in the event of an electrical fault. By establishing a low-impedance connection to the earth, the grounding system ensures that fault currents are safely directed away from the transformer and other equipment, reducing the risk of electrical shock to personnel working on or near the transformer.
Fault Current Discharge: In the event of a ground fault, where one of the phase conductors comes into contact with a conductive surface or the earth, the grounding system provides a path for the fault current to flow. This helps discharge the fault current, preventing it from damaging the transformer or causing additional electrical faults within the system.
Overcurrent Protection: The grounding system also plays a role in overcurrent protection. When a fault occurs, the grounding system enables protective devices, such as fuses or circuit breakers, to detect and interrupt the fault current. This helps protect the transformer from excessive currents and potential damage.
Voltage Stabilization: The grounding system helps stabilize the system voltage by providing a reference point for voltage potential. It establishes a solid ground reference, reducing the risk of high voltage gradients and maintaining a balanced electrical system. This is particularly important in ungrounded or isolated systems where maintaining voltage stability is crucial.
Surge Protection: The grounding system contributes to surge protection in the transformer. In the event of a lightning strike or other transient overvoltage, the grounding system helps dissipate the excess energy safely into the earth, preventing damage to the transformer and connected equipment.
Electrostatic Shielding: Some transformers, such as large power transformers, are equipped with an electrostatic shield between the windings and the core. The grounding system connects this shield to the ground, providing an additional layer of protection against electrical interference and reducing the risk of stray currents or induced voltages.
System Grounding: The grounding system of a transformer is an integral part of the overall system grounding scheme. It ensures consistent grounding practices throughout the electrical system, maintaining system reliability and reducing the potential for ground potential rise or circulating ground currents.
By fulfilling these functions, the grounding system in a transformer enhances electrical safety, protects the transformer and connected equipment from faults and surges, and contributes to the overall stability and reliability of the electrical system. It is essential to adhere to proper grounding practices and regularly inspect and maintain the grounding system to ensure its effectiveness and mitigate potential hazards.
Monitoring and control devices in Transformer
Monitoring and control devices are integral components of advanced transformers, providing real-time data and enabling precise control over various parameters. These devices enhance the operational efficiency, reliability, and safety of transformers. Let’s explore some of the key monitoring and control devices commonly found in advanced transformers:
Temperature Sensors: Temperature sensors are strategically placed within the transformer to monitor the temperature of critical components such as windings, core, and oil. By continuously measuring the temperature, these sensors provide valuable data that helps in assessing the transformer’s thermal performance and preventing overheating. Abnormal temperature rise can indicate faults or excessive loads, prompting timely corrective actions.
Pressure Gauges: Pressure gauges are used to monitor the pressure levels within the transformer’s tank. They are typically installed in the oil-filled transformers to detect any abnormal pressure variations caused by internal faults or external factors. Deviations from normal pressure levels can indicate leaks, insulation degradation, or internal arcing. Monitoring pressure helps prevent potential failures and ensures the safety of the transformer.
On-Load Tap Changers (OLTC): On-load tap changers enable the adjustment of the transformer’s turns ratio while the transformer is energized and under load. These devices allow for real-time control of the output voltage, compensating for fluctuations in the input voltage or load variations. On-load tap changers ensure efficient voltage regulation, optimizing the performance of the transformer in dynamic electrical systems.
Buchholz Relay: Buchholz relay is a gas and oil-operated device that detects and provides an alarm or trip signal for internal faults such as arcing, insulation failure, or low oil level. It is typically installed in oil-immersed transformers and acts as an early warning system, providing protection against severe faults that can lead to transformer damage or failure.
Dissolved Gas Analysis (DGA) Monitoring: DGA monitoring is a technique used to analyze the gases dissolved in the transformer oil. Faults within the transformer, such as arcing or insulation breakdown, produce characteristic gases that can be detected and analyzed. DGA monitoring helps identify the type and severity of faults, allowing for proactive maintenance and minimizing the risk of catastrophic failures.
Remote Monitoring and SCADA Systems: Advanced transformers may be equipped with remote monitoring capabilities, allowing operators to monitor the transformer’s parameters and receive real-time data remotely. Supervisory Control and Data Acquisition (SCADA) systems can be employed to centralize the monitoring and control of multiple transformers, facilitating efficient management of the electrical network.
By integrating these monitoring and control devices, advanced transformers enable proactive maintenance, early fault detection, and precise control over important parameters. This improves the reliability, operational efficiency, and lifespan of the transformers, ensuring optimal performance in various electrical applications. Read More about Transformer oil testing in detail.
Function of breather in a transformer
The function of a breather in a transformer is to regulate the exchange of air between the transformer’s internal components and the external environment. It is a device that helps maintain the dryness and cleanliness of the air inside the transformer tank, preventing moisture and contaminants from entering the system. The breather plays a crucial role in preserving the insulation system and ensuring the efficient operation of the transformer.
Here are the main functions of a breather in a transformer:
Moisture Control: One of the primary functions of a breather is to control the moisture content in the air that enters the transformer. Inside the transformer, the windings and other components are insulated with materials that can be sensitive to moisture. Moisture can degrade the insulation properties, leading to reduced performance and potentially causing electrical breakdown. The breather contains desiccant materials, such as silica gel, that absorb moisture from the air passing through it, helping to maintain dry conditions inside the transformer.
Contaminant Filtration: A breather is equipped with filters or screens that trap and remove contaminants present in the air. Dust, dirt, and other particles can accumulate on the transformer’s internal components, potentially causing insulation deterioration or affecting the transformer’s performance. The breather’s filtration system helps prevent these contaminants from entering the transformer, keeping the internal environment clean and extending the lifespan of the insulation system.
Pressure Equalization: The breather assists in equalizing the pressure inside the transformer tank with the external atmospheric pressure. As the transformer operates, temperature variations cause the internal air volume to expand and contract, resulting in pressure changes. The breather allows for the exchange of air with the external environment, preventing pressure differentials that could potentially damage the transformer’s seals or compromise its structural integrity.
Visual Indication: Some breathers are designed with visual indicators, such as color-changing silica gel or pressure gauges, to provide a visual indication of the breather’s condition. These indicators help monitor the saturation level of the desiccant material or detect pressure imbalances, enabling timely maintenance and replacement of the breather when necessary.
By maintaining dry and clean conditions inside the transformer, the breather helps preserve the insulation system, prevent moisture-related issues, and ensure the efficient and reliable operation of the transformer. It is an essential component that contributes to the overall longevity and performance of the transformer. Regular monitoring and maintenance of the breather are crucial to ensure its proper functioning and effectiveness in protecting the transformer.
Grounding system of a transformer
The grounding system in a transformer serves several important functions to ensure electrical safety and protect the transformer and its surrounding environment. Here are the main functions of the grounding system:
Personal Safety: The primary function of the grounding system is to provide a safe path for fault currents in the event of an electrical fault. By establishing a low-impedance connection to the earth, the grounding system ensures that fault currents are safely directed away from the transformer and other equipment, reducing the risk of electrical shock to personnel working on or near the transformer.
Fault Current Discharge: In the event of a ground fault, where one of the phase conductors comes into contact with a conductive surface or the earth, the grounding system provides a path for the fault current to flow. This helps discharge the fault current, preventing it from damaging the transformer or causing additional electrical faults within the system.
Overcurrent Protection: The grounding system also plays a role in overcurrent protection. When a fault occurs, the grounding system enables protective devices, such as fuses or circuit breakers, to detect and interrupt the fault current. This helps protect the transformer from excessive currents and potential damage.
Voltage Stabilization: The grounding system helps stabilize the system voltage by providing a reference point for voltage potential. It establishes a solid ground reference, reducing the risk of high voltage gradients and maintaining a balanced electrical system. This is particularly important in ungrounded or isolated systems where maintaining voltage stability is crucial.
Surge Protection: The grounding system contributes to surge protection in the transformer. In the event of a lightning strike or other transient overvoltage, the grounding system helps dissipate the excess energy safely into the earth, preventing damage to the transformer and connected equipment.
Electrostatic Shielding: Some transformers, such as large power transformers, are equipped with an electrostatic shield between the windings and the core. The grounding system connects this shield to the ground, providing an additional layer of protection against electrical interference and reducing the risk of stray currents or induced voltages.
System Grounding: The grounding system of a transformer is an integral part of the overall system grounding scheme. It ensures consistent grounding practices throughout the electrical system, maintaining system reliability and reducing the potential for ground potential rise or circulating ground currents.
By fulfilling these functions, the grounding system in a transformer enhances electrical safety, protects the transformer and connected equipment from faults and surges, and contributes to the overall stability and reliability of the electrical system. It is essential to adhere to proper grounding practices and regularly inspect and maintain the grounding system to ensure its effectiveness and mitigate potential hazards.
types of oil used in transformers
Transformers commonly use insulating oils to provide electrical insulation and cooling. The choice of oil depends on factors such as transformer design, voltage class, operating conditions, and safety considerations. Here are some types of oils commonly used in transformers:
Mineral Oil: Mineral oil, also known as transformer oil or insulating oil, is the most commonly used oil in transformers. It is a petroleum-based oil that offers good electrical insulation properties, high flash and fire point, and good heat dissipation. Mineral oil is cost-effective and readily available, making it suitable for a wide range of transformer applications.
Silicone Oil: Silicone oil, or silicone-based insulating oil, is an alternative to mineral oil. It has excellent thermal stability, high flash and fire point, and good electrical insulation properties. Silicone oil is often used in high-temperature applications or where a higher level of fire safety is required. It has a wider temperature operating range compared to mineral oil and better resistance to oxidation.
Synthetic Ester Oil: Synthetic ester oils are derived from vegetable or synthetic sources and are biodegradable and environmentally friendly. They offer good electrical insulation properties, high thermal stability, and excellent fire safety characteristics. Synthetic ester oils have a wide temperature operating range and are often used in environmentally sensitive areas, indoor installations, or where fire safety is a critical concern.
Natural Ester Oil: Natural ester oils, such as vegetable oils derived from renewable sources like soybeans or rapeseeds, are also used as insulating oils in transformers. They are biodegradable, have high flash and fire points, and offer good electrical insulation properties. Natural ester oils are non-toxic, environmentally friendly, and have excellent moisture absorption characteristics.
It’s important to note that different transformer designs and applications may have specific oil requirements. The choice of oil should comply with relevant standards, regulations, and manufacturer recommendations. Additionally, regular oil testing and maintenance are essential to monitor the oil condition and ensure the transformer’s optimal performance and longevity.
Types of Transformers
When it comes to electrical circuits, understanding the various types of transformers is crucial for designing efficient and reliable systems. Transformers are versatile devices that can step up or step down voltage levels while ensuring minimal power loss. In this article, we will explore the different “types of transformers” commonly used in electrical circuits, highlighting their unique characteristics and applications.
Firstly, one of the most common types of transformers is the “step-up transformer.” As the name suggests, this transformer increases the voltage level from the input to the output side. Step-up transformers are commonly used in power transmission systems, where they elevate voltage levels for efficient long-distance transmission, reducing power losses along the way.
Conversely, we have the “step-down transformer,” which does the opposite. It lowers the voltage level from the input to the output side, making it suitable for various applications such as residential, commercial, and industrial power distribution. Step-down transformers are often found in substations and electrical panels, ensuring safe and reliable power supply to end-users.
Another type of transformer is the “isolation transformer.” It provides electrical isolation between the input and output circuits, protecting sensitive equipment from electrical disturbances and reducing the risk of electrical shocks. Isolation transformers find applications in hospitals, laboratories, and other environments where electrical safety is paramount.
Additionally, there are “autotransformers” that combine the primary and secondary winding into a single continuous winding. Autotransformers are known for their compact size, cost-effectiveness, and ability to step up or step down voltage levels. They are commonly used in voltage regulation applications and variable speed motor drives.
Lastly, we have “special-purpose transformers” designed for specific applications. These include instrument transformers used for measuring voltage and current in power systems, audio transformers used in audio amplifiers, and high-frequency transformers used in electronic devices.
Understanding the “types of transformers” in electrical circuits is essential for designing efficient and reliable systems. Whether it’s stepping up or stepping down voltage levels, providing isolation, or serving specific applications, each type of transformer plays a vital role in powering our modern world. By familiarizing yourself with these transformer types, you can make informed decisions and ensure optimal performance in your electrical circuit designs.
step-up transformers
In electrical circuits, “step-up transformers” play a crucial role in elevating voltage levels for efficient power transmission and distribution. Understanding the working principles and applications of step-up transformers is essential for designing and optimizing electrical systems. In this article, we will delve into the world of “step-up transformers,” exploring their functionality, characteristics, and significant contributions to electrical circuits.
A step-up transformer is designed to increase the voltage from the input (primary) side to the output (secondary) side. It consists of two sets of windings, namely the primary winding and the secondary winding. The primary winding is connected to the power source, while the secondary winding is connected to the load. By having a greater number of turns in the secondary winding compared to the primary winding, the step-up transformer can magnify the voltage.
One of the primary applications of step-up transformers is in power transmission systems. When electricity is generated at power plants, it undergoes step-up transformation to extremely high voltages for efficient long-distance transmission. By elevating the voltage, step-up transformers reduce power losses that occur during transmission. This allows electricity to be transmitted over long distances with minimal loss, ensuring efficient power delivery to distant regions.
Step-up transformers also find application in electrical substations. Here, they are used to increase the voltage level for further distribution to residential, commercial, and industrial areas. By stepping up the voltage, step-up transformers enable efficient power distribution over a wider area, ensuring that the delivered voltage remains within acceptable limits even at distant locations.
Furthermore, step-up transformers are essential in certain industrial processes that require higher voltage levels. For example, in arc furnaces used for metal smelting, step-up transformers are utilized to increase the voltage to the necessary levels for melting and refining metals.
Step-up transformers are indispensable in electrical circuits, especially in power transmission and distribution systems. Their ability to increase voltage levels efficiently allows for long-distance transmission with minimal power loss. By understanding the functionality and applications of step-up transformers, engineers and designers can optimize electrical systems, ensuring reliable and efficient power delivery. Whether it’s powering cities or enabling industrial processes, step-up transformers play a vital role in the functioning of our modern electrical infrastructure.
step-down transformers
In electrical circuits, “step-down transformers” are crucial components that play a significant role in reducing voltage levels for safe and efficient power distribution. Understanding the working principles and applications of step-down transformers is essential for designing and optimizing electrical systems. In this article, we will explore the world of “step-down transformers,” examining their functionality, characteristics, and the important contributions they make to electrical circuits.
A step-down transformer is specifically designed to decrease the voltage from the input (primary) side to the output (secondary) side. It consists of two sets of windings, where the primary winding is connected to the power source, and the secondary winding is connected to the load. By having a smaller number of turns in the secondary winding compared to the primary winding, the step-down transformer can reduce the voltage.
One of the primary applications of step-down transformers is in power distribution systems. After electricity is transmitted at high voltages through long-distance transmission lines, step-down transformers are used at substations to decrease the voltage to safer levels suitable for residential, commercial, and industrial use. This ensures that the voltage delivered to end-users remains within acceptable limits and prevents potential damage to electrical equipment.
Step-down transformers also find extensive use in various household appliances and electronic devices. These transformers convert the higher voltage levels supplied by the power grid into lower voltage levels that are suitable for safe operation of devices like refrigerators, televisions, computers, and smartphones. By stepping down the voltage, these transformers provide a stable and reliable power supply to the devices, protecting them from potential damage due to excessive voltage.
Additionally, step-down transformers are commonly used in industrial applications where specific machinery and equipment require lower voltage levels. These transformers enable the operation of motors, control systems, and other industrial devices at the appropriate voltage, ensuring optimal performance and safety.
Step-down transformers are integral to electrical circuits, particularly in power distribution and consumer electronics. Their ability to reduce voltage levels allows for safe and efficient power delivery to end-users. By understanding the functionality and applications of step-down transformers, engineers and designers can optimize electrical systems, ensuring reliable and stable power supply to a wide range of devices. Whether it’s powering our homes or driving industrial processes, step-down transformers play a vital role in the functioning of our modern electrical infrastructure.
isolation transformer
In electrical circuits, an “isolation transformer” is a vital component that provides electrical isolation between the input and output circuits. Understanding the working principles and applications of isolation transformers is essential for ensuring electrical safety and mitigating the risks of electrical disturbances. In this article, we will explore the concept of the “isolation transformer,” examining its functionality, characteristics, and significant contributions to electrical circuits.
An isolation transformer is designed to physically and electrically separate the primary (input) and secondary (output) windings. Unlike other transformers that have a direct electrical connection between the input and output, an isolation transformer offers a high degree of isolation, protecting sensitive equipment and users from electrical disturbances.
One of the primary applications of an isolation transformer is in medical environments, where patient safety is of utmost importance. By providing electrical isolation, these transformers protect patients and medical personnel from the risk of electrical shocks. Isolation transformers are commonly used in hospitals, clinics, and other medical facilities, ensuring a safe electrical environment for diagnostic equipment, surgical tools, and patient monitoring systems.
Isolation transformers are also employed in laboratory settings where precise measurements and sensitive experiments are conducted. By isolating the equipment from the power source, these transformers minimize the effects of electrical noise and ground loops, preserving the accuracy of measurements and preventing potential damage to sensitive devices.
Additionally, isolation transformers find application in various industrial environments, especially where electrical noise or voltage fluctuations are a concern. By providing galvanic isolation, they protect electronic equipment from power surges, voltage spikes, and electromagnetic interference (EMI). Isolation transformers are widely used in control systems, automation equipment, and data centers, safeguarding critical components and ensuring reliable operation.
Furthermore, isolation transformers are utilized in audio systems, particularly for eliminating ground loops and reducing unwanted hum or noise. They are commonly found in recording studios, sound systems, and broadcast setups, ensuring high-quality audio reproduction without interference.
The isolation transformer is a crucial component in electrical circuits, providing a high level of electrical isolation and protecting sensitive equipment and users from electrical disturbances. Whether in medical environments, laboratories, or industrial settings, isolation transformers play a vital role in ensuring electrical safety, minimizing noise, and preserving the integrity of electrical systems. By understanding the functionality and applications of isolation transformers, engineers and designers can incorporate these transformers to enhance the reliability and performance of their electrical circuits.
Autotransformers
Autotransformers are versatile devices that find significant application in electrical circuits due to their compact size, cost-effectiveness, and ability to step up or step-down voltage levels. Understanding the working principles and applications of autotransformers is essential for designing and optimizing electrical systems. In this article, we will explore the concept of “autotransformers,” examining their functionality, characteristics, and important contributions to electrical circuits.
An autotransformer is a type of transformer that combines the primary and secondary windings into a single continuous winding. This configuration allows for voltage transformation by tapping different points along the winding. The tapped connection point determines whether the autotransformer functions as a step-up or step-down transformer.
The versatility of autotransformers lies in their ability to provide variable voltage ratios with a smaller physical size compared to conventional transformers. By utilizing a shared winding, autotransformers achieve higher efficiency as there is no need for separate windings, resulting in reduced copper and core losses.
Autotransformers find applications in various scenarios where voltage transformation is required. One common application is in voltage regulation. By adjusting the tap point along the winding, the output voltage can be regulated to match the specific requirements of the load. This flexibility makes autotransformers suitable for applications such as variable speed motor drives, where precise control of voltage and speed is necessary.
Moreover, autotransformers are commonly used in power transmission and distribution systems to interconnect systems with different voltage levels. They facilitate the efficient transfer of power by stepping up or stepping down voltages to match the requirements of the interconnected systems.
Another significant advantage of autotransformers is their ability to handle high power levels efficiently. Due to the shared winding design, autotransformers have lower impedance compared to conventional transformers, resulting in reduced voltage drops and improved voltage regulation.
Furthermore, autotransformers are utilized in specialized applications where specific voltage ratios are required. For instance, they are commonly used in audio equipment and radio frequency (RF) circuits for impedance matching and signal level adjustment.
Autotransformers are versatile components in electrical circuits, offering variable voltage ratios, compact size, and cost-effectiveness. Their ability to step up or step down voltages efficiently makes them suitable for a wide range of applications, including voltage regulation, power transmission, and specialized applications in audio and RF circuits. By understanding the functionality and advantages of autotransformers, engineers and designers can incorporate these transformers to enhance the performance and efficiency of their electrical systems.
Special-purpose transformers
Special-purpose transformers are an integral part of electrical circuits, designed to cater to specific applications and unique requirements. These transformers offer specialized functionalities and features that make them invaluable in various industries. In this article, we will explore the concept of “special-purpose transformers,” examining their diverse applications, characteristics, and the significant contributions they make to electrical circuits.
Special-purpose transformers are designed to meet specific needs that cannot be adequately addressed by standard transformers. These transformers are tailored to deliver precise voltage levels, accommodate specific load types, or provide enhanced performance in specialized applications. Let’s delve into some examples of special-purpose transformers and their applications.
One notable type of special-purpose transformer is the instrument transformer. Instrument transformers are used for accurate measurement of voltage and current in power systems. They are commonly employed in metering and protection applications, allowing accurate monitoring and control of electrical parameters. Instrument transformers ensure that the signals provided to measuring instruments or protective relays are proportionate to the actual voltage and current levels, facilitating reliable system operation and monitoring.
Another application of special-purpose transformers is found in audio equipment. Audio transformers are utilized in audio amplifiers to match and balance impedance levels, ensuring high-fidelity sound reproduction and minimizing signal distortion. These transformers play a vital role in achieving optimal audio quality in recording studios, sound systems, and public address systems.
High-frequency transformers are another type of special-purpose transformers. These transformers are designed to handle high-frequency signals in electronic devices such as telecommunication equipment, power electronics, and radio frequency (RF) circuits. High-frequency transformers are crucial for efficient power conversion, signal transmission, and impedance matching in these applications.
Additionally, special-purpose transformers include custom-designed transformers for specific industrial processes or equipment. For example, transformers used in electric arc furnaces are specially designed to withstand high currents and provide the necessary power for metal smelting and refining operations. Transformers for traction systems in trains and electric vehicles are tailored to handle high voltages and deliver power efficiently to drive motors.
Special-purpose transformers offer tailored solutions for specific applications and requirements in electrical circuits. From instrument transformers and audio transformers to high-frequency transformers and custom-designed transformers, these specialized devices contribute to the reliable and efficient operation of various industries. By understanding the diverse applications and benefits of special-purpose transformers, engineers can select and implement these transformers to optimize performance and address unique challenges in their electrical systems.
Distribution transformers
Distribution transformers are a type of electrical transformer used in power distribution systems to step down the voltage from high voltage transmission lines to lower voltages suitable for distribution to homes, businesses, and other end-users. They play a crucial role in delivering electricity safely and efficiently to consumers.
Here are some key characteristics and features of distribution transformers:
Step-Down Voltage: Distribution transformers primarily function as step-down transformers, converting high voltage levels typically ranging from 2.4 kV to 33 kV to lower voltage levels suitable for local distribution. Common distribution voltage levels include 400 V, 230 V, and 120/240 V, depending on the region and local requirements.
Compact and Efficient Design: Distribution transformers are designed to be compact, lightweight, and efficient. They are typically installed on utility poles, in substations, or in pad-mounted enclosures, depending on the specific application. The compact design allows for easier installation and maintenance.
Oil-Immersed Cooling: Distribution transformers often utilize oil-immersed cooling systems. The transformer windings and core are immersed in insulating mineral oil, which provides both electrical insulation and efficient cooling. The oil transfers heat away from the core and windings, ensuring optimal performance and preventing overheating.
Transformer Taps: Distribution transformers may have multiple taps on the winding to allow for voltage regulation. These taps enable slight adjustments to the output voltage to compensate for variations in the supply voltage or to meet specific local requirements. Tap changers can be either off-load (de-energized) or on-load (energized) depending on the design.
Protective Devices: Distribution transformers are equipped with various protective devices to ensure safe operation and prevent damage. These may include fuses, overcurrent protection devices, temperature sensors, and pressure relief devices. These protective devices help detect faults, control excessive currents, and mitigate potential hazards.
Reliability and Longevity: Distribution transformers are designed to be highly reliable and durable, with a typical operational lifespan of several decades. Regular maintenance, including monitoring oil quality, insulation testing, and visual inspections, helps ensure their continued performance and longevity.
Distribution transformers are an essential component of the power distribution infrastructure, stepping down voltage levels for safe and efficient delivery of electricity to end-users. They are widely used in urban, suburban, and rural areas to provide electrical power for residential, commercial, and industrial applications. The proper selection, installation, and maintenance of distribution transformers are critical for ensuring a reliable and stable power supply to consumers.
Power transformers
Power transformers are a type of electrical transformer used in high voltage transmission systems to transfer electrical energy efficiently between different voltage levels. They play a vital role in the transmission and distribution of electricity over long distances, ensuring that power is delivered reliably and at the required voltage levels.
Here are some key characteristics and features of power transformers:
High Voltage Transformation: Power transformers are primarily designed for high voltage applications, typically in the range of hundreds of kilovolts (kV) to several hundreds of kilovolts (kV). They step up the voltage from the generating station to facilitate long-distance transmission, reducing losses and optimizing efficiency.
Efficient Energy Transfer: Power transformers efficiently transfer electrical energy from the primary side (high voltage) to the secondary side (lower voltage) by electromagnetic induction. The transformer core and windings are designed to minimize energy losses and ensure efficient power transmission.
Three-Phase Design: Most power transformers are designed as three-phase transformers to accommodate the three-phase AC power system commonly used in electrical grids. Three-phase transformers enable balanced power distribution and efficient transmission of electrical energy over long distances.
Large Power Ratings: Power transformers are capable of handling high power ratings, ranging from a few megawatts (MW) to several hundred megawatts (MW). These transformers are used in substations, power plants, and other utility installations where large amounts of power need to be stepped up or down.
Oil-Immersed Cooling: Power transformers often use oil-immersed cooling systems for efficient heat dissipation. The transformer windings and core are immersed in insulating mineral oil, which serves as both an electrical insulator and a cooling medium. The oil helps remove heat generated during operation, ensuring the transformer operates within optimal temperature limits.
High Insulation Levels: Power transformers have robust insulation systems to withstand high voltages and ensure electrical safety. The windings are insulated using materials such as paper, varnish, and pressboard, which provide excellent dielectric strength and insulation properties.
Monitoring and Protection Systems: Power transformers are equipped with sophisticated monitoring and protection systems. These systems include devices for measuring voltage, current, temperature, and other parameters to ensure safe and reliable operation. Protective devices, such as Buchholz relays, pressure relief devices, and temperature alarms, are incorporated to detect and respond to abnormal conditions or faults.
Power transformers are critical components in electricity transmission networks, enabling efficient transfer of electrical energy over long distances. They ensure voltage transformation, power transmission, and distribution at different levels, contributing to the reliable and stable supply of electricity to consumers. Proper design, installation, and maintenance of power transformers are essential for ensuring the integrity and longevity of the power transmission system.
common transformer tests
Various tests are conducted on transformers to ensure their proper functioning, reliability, and adherence to safety standards. Here are some common transformer tests:
Transformer Turns Ratio Test: This test measures the turns ratio of the transformer by applying a known voltage to the primary winding and measuring the resulting voltage on the secondary winding. It helps verify the transformer’s winding configuration and ensure proper voltage transformation.
Insulation Resistance Test: The insulation resistance test checks the insulation integrity of the transformer windings. A high voltage is applied between the windings and the transformer’s core or ground, and the resulting current is measured. It helps identify any insulation weaknesses or moisture ingress in the windings.
Winding Resistance Test: This test measures the DC resistance of the transformer windings. By passing a known DC current through the windings and measuring the resulting voltage drop, the resistance can be calculated. It helps detect any high resistance connections, shorted turns, or faulty winding sections.
Transformer Oil Analysis: The oil in the transformer is analyzed to assess its condition and detect any potential issues. Tests performed on the transformer oil include dissolved gas analysis (DGA) to detect gas levels indicative of internal faults, moisture content analysis, acidity testing, and dielectric breakdown voltage measurement. Oil analysis helps evaluate the insulation condition and identify any required maintenance or corrective actions.
Transformer Impedance Test: The impedance test determines the impedance or voltage drop of the transformer under specified operating conditions. It helps assess the transformer’s ability to withstand short-circuit currents and determines its contribution to system fault levels.
No-Load Loss and Excitation Current Test: This test measures the no-load loss and excitation current of the transformer. The transformer is energized at rated voltage and frequency with no load connected, and the power consumed and current drawn are measured. It helps evaluate the core losses and magnetic characteristics of the transformer.
Load Loss and Impedance Voltage Test: This test measures the load loss and impedance voltage of the transformer under specified load conditions. The transformer is subjected to a specified load, and the losses and voltage drop are measured. It helps determine the transformer’s efficiency and its voltage regulation capabilities.
Partial Discharge Test: The partial discharge test is performed to detect any partial discharge activity occurring within the transformer insulation. It helps identify insulation weaknesses or defects that may lead to insulation breakdown or failure.
These are some of the common tests conducted on transformers to assess their electrical and mechanical characteristics, insulation integrity, and overall performance. Regular testing and maintenance are essential to ensure the reliable operation and longevity of transformers in electrical systems. Read more about Transformer Tests Before Commissioning.
common transformer testing labs
There are various testing labs and facilities that specialize in transformer testing and provide comprehensive assessment and certification services. Here are some well-known transformer testing labs:
KEMA Laboratories: KEMA Laboratories, a part of DNV GL, is a globally recognized independent testing and certification laboratory for power and distribution transformers. They offer a wide range of transformer testing services, including type tests, routine tests, special tests, and certification according to international standards.
CESI: CESI is an international provider of testing, consulting, and engineering services for the energy sector. They have state-of-the-art laboratories for transformer testing and certification, offering a comprehensive range of tests, including type tests, routine tests, and special tests.
ABB Testing Laboratories: ABB, a leading power and automation technology company, operates testing laboratories for transformers and other electrical equipment. Their testing services cover various transformer types, ratings, and standards, ensuring compliance and reliability.
KERI: The Korea Electrotechnology Research Institute (KERI) is a prominent research and testing organization in South Korea. They have dedicated transformer testing facilities offering a wide range of tests, including type tests, routine tests, and special tests, to ensure the performance and safety of transformers.
OMICRON Electronics: OMICRON Electronics is a global provider of testing and diagnostic solutions for electrical power systems. They offer advanced diagnostic equipment and software for transformer testing, including insulation diagnostics, dynamic resistance measurement, and frequency response analysis.
Transformer Test and Research Center (TTRC): The Transformer Test and Research Center, based in India, is a specialized laboratory for transformer testing and research. They provide a comprehensive range of transformer tests, including type tests, routine tests, and specialized tests, adhering to national and international standards.
National High Voltage Testing Laboratory (NHVTL): NHVTL, based in India, is a government-run facility specializing in high-voltage testing, including transformer testing. They offer testing services for power transformers, instrument transformers, and other electrical equipment, ensuring compliance with national standards.
These are just a few examples of well-known transformer testing labs and facilities. Many other reputable laboratories worldwide provide transformer testing services, often accredited by relevant certification bodies and recognized within the industry. It is important to choose a testing lab that has the necessary expertise, accreditation, and experience to ensure accurate and reliable transformer testing results.
Steps in designing a transformer
Designing a transformer involves several steps to ensure its optimal performance, efficiency, and reliability. While the specific design process can vary depending on the transformer’s application and specifications, here are the general steps involved in designing a transformer:
Determine Design Specifications: Define the required electrical specifications of the transformer, including voltage levels, power rating, frequency, and any special requirements such as impedance, regulation, or temperature rise limits. Consider the intended application and environmental factors that may influence the design.
Magnetic Design: Determine the core material and size based on the desired power rating, frequency, and efficiency. Calculate the core dimensions and number of turns required to achieve the desired magnetic flux density and minimize core losses. Consider factors like magnetic saturation, hysteresis losses, and eddy current losses.
Electrical Design: Determine the appropriate wire size, number of turns, and winding configuration for both the primary and secondary windings. Calculate the wire gauge, taking into account the desired current-carrying capacity and resistance. Consider factors such as voltage drop, insulation requirements, and winding connections.
Cooling System Design: Select the cooling method for the transformer, which can include air, oil, or liquid cooling. Determine the cooling system design based on factors such as anticipated load, ambient temperature, and required temperature rise limits. Size the cooling system components, such as radiators, fans, or oil pumps, accordingly.
Insulation Design: Determine the insulation system for the transformer to ensure proper electrical insulation and withstand voltage requirements. Choose appropriate insulation materials, such as paper, pressboard, or synthetic materials, based on the voltage class and environmental conditions. Consider factors like dielectric strength, thermal class, and aging characteristics.
Mechanical Design: Design the mechanical structure of the transformer, including the core and coil assembly, winding supports, tank, and mounting arrangements. Ensure proper alignment, clearances, and mechanical strength to withstand mechanical stresses, transportation, and environmental factors.
Losses and Efficiency Calculation: Calculate the transformer losses, including copper losses in the windings and core losses. Evaluate the overall efficiency of the transformer and make necessary adjustments in the design to optimize efficiency.
Prototype Development and Testing: Build a prototype of the designed transformer and conduct various tests, including electrical tests, temperature rise tests, short-circuit tests, and insulation tests. Analyze the test results and make any necessary adjustments or improvements to the design.
Documentation and Standards Compliance: Prepare detailed design documentation, including schematics, drawings, and specifications. Ensure compliance with relevant international standards, such as IEC, ANSI, or specific customer requirements.
Production and Quality Assurance: Once the design is finalized, proceed with manufacturing the transformer using appropriate production methods and quality control processes. Conduct regular quality assurance checks throughout the manufacturing process to ensure adherence to the design specifications and standards.
It’s important to note that designing a transformer requires expertise in electrical engineering, magnetic design principles, insulation technology, and manufacturing processes. The design process may involve iterative steps and considerations based on specific project requirements and industry best practices.
What is a transformer?
A transformer is an electrical device that transfers electrical energy between two or more circuits through electromagnetic induction. It consists of two coils (windings) linked by a magnetic core.
What are the main types of transformers?
The main types of transformers include:
Step-Up Transformer: Increases voltage.
Step-Down Transformer: Decreases voltage.
Isolation Transformer: Provides electrical isolation between input and output.
Auto Transformer: Single-winding transformer with a tapped winding acting as both primary and secondary.
What is the purpose of a step-up transformer?
A step-up transformer increases voltage, typically used in power transmission to reduce energy losses over long distances.
Why is isolation important in transformers?
Isolation transformers provide electrical separation between input and output, preventing the transfer of direct current (DC) and minimizing the risk of electric shock.
What are the primary components of a transformer?
The primary components include:
Core: Provides a magnetic path.
Windings: Coils of wire carrying alternating current.
Insulation: Prevents electrical leakage.
Tank: Encases the core and windings in oil-filled transformers.
Cooling System: Maintains the operating temperature.
What is the role of the transformer core?
The transformer core is typically made of laminated iron or steel and provides a low-reluctance path for the magnetic flux, facilitating efficient energy transfer.
Why are transformers often filled with oil?
Oil serves as a coolant and insulator in transformers. It helps dissipate heat generated during operation and enhances insulation properties.
What is the difference between a power transformer and a distribution transformer?
Power transformers are used in power transmission, while distribution transformers step down voltage for local distribution.
How is transformer efficiency calculated?
Transformer efficiency is calculated as the ratio of output power to input power, expressed as a percentage. Efficiency (%) = (Output Power / Input Power) x 100.
What are some common applications of transformers?
Transformers are used in various applications, including power distribution, electrical appliances, electronics, lighting, and industrial machinery.
Can transformers work with direct current (DC)?
Transformers rely on alternating current (AC) for electromagnetic induction. They do not work with direct current (DC) unless converted to AC using electronic devices.
Worth Read Posts
Follow us on LinkedIn”Electrical Insights” to get the latest updates in Electrical Engineering. You can also Follow us on LinkedIn and Facebook to see our latest posts on Electrical Engineering Topics.