Transformer Oil Testing: 9 Important Tests for Healthiness
Transformer Oil Testing
Transformer oil testing is a critical process in ensuring the reliability and longevity of power transformers. Through comprehensive analysis and evaluation of transformer oil, professionals can assess the condition of the transformer insulation and identify potential issues or degradation. Transformer oil testing plays a crucial role in preventive maintenance, enabling proactive measures to be taken before failures occur.
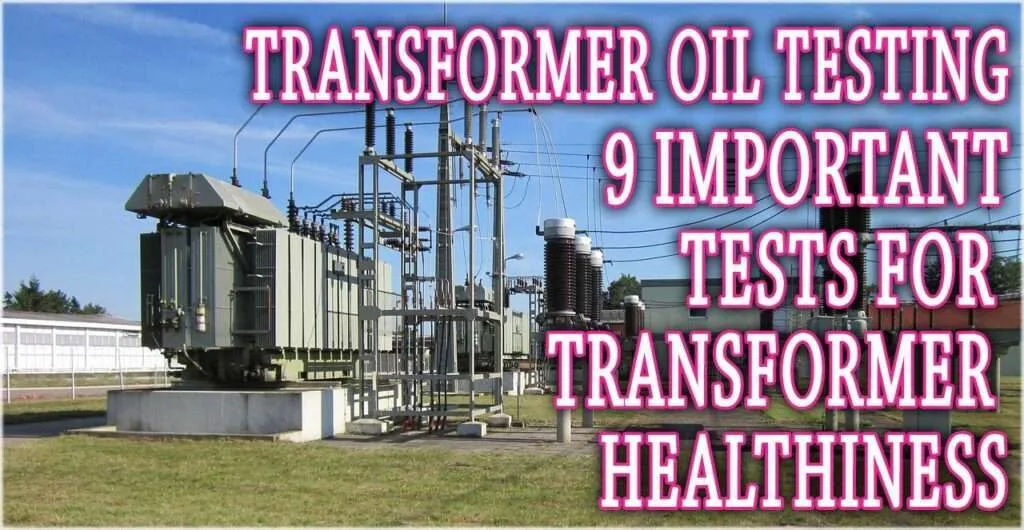
Read More About
By utilizing various testing methods throughout the transformer oil testing process, such as dissolved gas analysis (DGA), dielectric strength testing, interfacial tension testing (IFT), acid number testing (AN), water content testing, power factor testing, PCB analysis, furan analysis, and visual inspection, the overall health and performance of transformers can be optimized. Some of these tests are performed in transformer oil testing labs. Transformer oil testing is an essential practice that safeguards the efficiency and reliability of power transformers, promoting the seamless functioning of electrical systems and minimizing downtime.
Dissolved Gas Analysis (DGA)
Dissolved Gas Analysis (DGA) is a fundamental and indispensable component of transformer oil testing. It plays a crucial role in assessing the condition of transformer insulation and identifying potential faults or abnormalities. DGA is a reliable diagnostic technique that involves analyzing the gases dissolved in the transformer oil.
During transformer operation, various internal and external factors can cause degradation or faults within the insulation system. These issues often result in the generation of characteristic gases, which dissolve into the transformer oil. By analyzing the type and concentration of these gases, professionals can gain valuable insights into the transformer’s health and detect any potential problems before they escalate into major failures.
DGA is typically performed by extracting a representative oil sample from the transformer and subjecting it to specialized laboratory analysis. The oil sample is carefully degassed to remove any free or dissolved gases that may have accumulated during the sampling process. The degassed oil is then analyzed using techniques such as gas chromatography or Fourier transform infrared spectroscopy to identify and quantify the dissolved gases present.
The presence of specific gases can be indicative of particular types of faults within the transformer. For example, the presence of hydrogen (H₂) and methane (CH₄) gases may suggest thermal degradation or overheating of the oil and insulation system. Elevated levels of ethylene (C₂H₄) and acetylene (C₂H₂) gases can indicate partial discharges or arcing. Other gases such as carbon monoxide (CO), carbon dioxide (CO₂), and oxygen (O₂) can provide further insights into the transformer’s condition and the severity of any faults.
By monitoring and interpreting the results of DGA, experts can make informed decisions regarding maintenance, repairs, or replacements. Early detection of potential faults through DGA allows for proactive measures to be taken, minimizing the risk of unexpected transformer failures, reducing downtime, and optimizing the performance and lifespan of the transformer.
Dissolved Gas Analysis (DGA) is a vital aspect of transformer oil testing. It enables the assessment of transformer insulation condition by analyzing the dissolved gases in the oil. By identifying and quantifying these gases, professionals can detect potential faults, diagnose issues, and take proactive steps to maintain the transformer’s health. DGA is a valuable diagnostic tool that enhances the reliability and longevity of transformers, ensuring the seamless functioning of electrical systems.
Dielectric Strength Test
The Dielectric Strength Test is a significant component of transformer oil testing, contributing to the overall assessment of insulation quality and reliability. This test plays a crucial role in determining the oil’s ability to withstand electrical stress without breakdown, making it an essential diagnostic tool in transformer oil testing.
During the Dielectric Strength Test, a high voltage is applied to a sample of transformer oil. The voltage is gradually increased until the oil experiences a breakdown, leading to a flow of current. The voltage at which this breakdown occurs is known as the breakdown voltage or dielectric strength. By measuring the dielectric strength, professionals can evaluate the oil’s insulation properties and determine its ability to prevent electrical failures.
The dielectric strength of transformer oil is a critical parameter as it directly reflects the effectiveness of the insulation system. If the dielectric strength is low, it indicates a higher risk of electrical breakdown, which can result in transformer malfunctions or failures. Therefore, regular dielectric strength testing is necessary to ensure the oil’s optimal condition and the reliable performance of the transformer.
By monitoring the dielectric strength over time, trends and changes in insulation quality can be identified. A gradual decrease in dielectric strength may indicate aging or degradation of the oil and insulation materials. It can be caused by factors such as thermal stress, moisture absorption, or the presence of contaminants. Identifying such changes in dielectric strength allows maintenance professionals to take timely corrective actions to prevent further deterioration and ensure the transformer’s long-term reliability.
Furthermore, dielectric strength testing provides valuable data for comparing different types of transformer oils. It helps in selecting the most suitable oil for specific transformer applications, ensuring optimal performance and longevity. By considering the dielectric strength characteristics of various oils, manufacturers and operators can make informed decisions regarding oil selection, minimizing the risk of electrical breakdown and maximizing the transformer’s efficiency.
The Dielectric Strength Test is a critical component of transformer oil testing. It assesses the oil’s ability to withstand electrical stress and prevent breakdowns. By measuring the dielectric strength, professionals can evaluate insulation quality, identify potential issues, and take proactive measures to maintain the transformer’s reliability. Regular dielectric strength testing is essential for ensuring optimal performance and extending the lifespan of transformers.
Interfacial Tension (IFT) Test
The Interfacial Tension (IFT) Test is a significant method used in transformer oil testing to evaluate the oil’s cleanliness and its resistance to contamination. This test plays a crucial role in determining the oil’s ability to separate from water or solid particles, making it an essential diagnostic tool in transformer oil testing.
The IFT test measures the interfacial tension between the oil and water or solid particles present in the transformer system. Interfacial tension refers to the force at the boundary between two immiscible substances, such as oil and water. By quantifying this tension, professionals can assess the oil’s ability to resist mixing or emulsifying with water or solid contaminants.
The IFT value obtained from the test indicates the oil’s cleanliness and its resistance to contamination. A higher IFT value suggests that the oil has a stronger tendency to separate from water or solid particles, indicating better resistance to contamination. On the other hand, a lower IFT value indicates reduced cleanliness and a higher risk of emulsification or mixing with water or solid contaminants.
In transformer systems, maintaining a high IFT value is crucial for optimal performance and longevity. Contamination in the form of water or solid particles can significantly impact the insulation properties of the oil and lead to decreased transformer efficiency or even failure. By regularly monitoring the IFT value, maintenance professionals can identify any deviations from the desired cleanliness levels and take appropriate actions to mitigate potential risks.
The IFT test is typically conducted using specialized equipment that measures the force required to separate the oil and water phases in a sample. The test is performed under controlled conditions to ensure accurate and consistent results. It is essential to follow standardized procedures and protocols during the IFT test to maintain reliability and comparability of the results.
In transformer oil testing, the IFT test serves as a valuable tool for assessing the overall condition of the oil and its resistance to contamination. By monitoring the IFT value over time, professionals can identify trends and changes that may indicate the presence of water or solid contaminants. Prompt detection of such contaminants allows for timely corrective actions to be taken, preventing further damage to the transformer and ensuring its reliable operation.
The Interfacial Tension (IFT) Test is an integral part of transformer oil testing. It evaluates the oil’s cleanliness and its ability to resist contamination. By measuring the interfacial tension between the oil and water or solid particles, the IFT test provides valuable insights into the oil’s condition and its separation properties. Regular IFT testing is essential for maintaining optimal performance, minimizing the risk of contamination-related issues, and ensuring the longevity of transformers.
Acid Number (AN) Test
The Acid Number (AN) Test is a vital component of transformer oil testing that helps assess the acidity level of the oil. This test plays a crucial role in evaluating the oil’s condition, detecting potential oxidation or contamination, and ensuring the optimal performance of transformers.
During the Acid Number Test, a sample of the transformer oil is taken and titrated with a standardized solution of potassium hydroxide (KOH). The titration process determines the quantity of KOH required to neutralize the acid present in the oil. The Acid Number is expressed as the milligrams of KOH required to neutralize one gram of oil.
The Acid Number provides a quantitative measurement of the acidity level in the transformer oil. An increase in the Acid Number indicates a higher concentration of acids, suggesting potential oxidation or contamination within the oil. Oxidation can occur due to the oil’s exposure to oxygen and high temperatures, while contamination can result from external sources or degradation of insulation materials.
Regular Acid Number testing is crucial for monitoring the oil’s condition and identifying any deviations from the acceptable acidity levels. By tracking the Acid Number over time, maintenance professionals can detect abnormal trends and take appropriate actions to prevent further degradation or potential damage to the transformer.
A high Acid Number can have detrimental effects on the transformer’s performance and reliability. Acidic components can corrode metal surfaces, degrade insulation materials, and lead to the formation of sludge or deposits. These issues can result in reduced insulation effectiveness, increased heat generation, and even electrical failures.
By performing Acid Number testing, professionals gain valuable insights into the transformer oil’s condition and can take proactive measures to maintain its optimal performance. Regular oil analysis, including Acid Number testing, allows for timely detection of potential issues, enabling the implementation of corrective actions before significant damage occurs.
It is important to note that different standards and guidelines may define acceptable Acid Number ranges for transformer oil. Therefore, it is essential to adhere to industry-specific recommendations and consult with experts to interpret the test results accurately.
The Acid Number (AN) Test is a critical aspect of transformer oil testing. By measuring the acidity level in the oil, this test helps evaluate the oil’s condition, detect potential oxidation or contamination, and ensure the optimal performance of transformers. Regular Acid Number testing, along with other oil analysis techniques, allows maintenance professionals to identify and address potential issues, ensuring the longevity and reliability of transformer systems.
Water Content Test
The Water Content Test is an essential component of transformer oil testing that focuses on measuring the amount of water present in the oil. This test plays a crucial role in evaluating the oil’s moisture level, as excessive water content can have detrimental effects on the transformer’s insulation and overall performance.
Water can enter transformer oil through various sources, such as external leaks, improper maintenance procedures, or degradation of insulation materials. Once present in the oil, water can significantly impact the oil’s dielectric properties, leading to reduced insulation effectiveness and increased risk of electrical failures.
During the Water Content Test, a representative sample of the transformer oil is extracted, and the water content is measured using specialized techniques. One commonly used method is Karl Fischer titration, which involves a chemical reaction between the water in the oil sample and a Karl Fischer reagent. The reaction allows for precise quantification of the water content in the oil.
Monitoring the water content in transformer oil is critical for several reasons. First, water can lead to the formation of acidic byproducts through hydrolysis, accelerating the oil’s degradation and reducing its useful life. Second, water can cause insulation materials, such as paper, to deteriorate, compromising the transformer’s performance and reliability. Third, water can create a conducive environment for the growth of microbiological organisms, leading to further contamination and degradation of the oil.
Regular Water Content testing allows maintenance professionals to assess the oil’s moisture level and take appropriate corrective actions. By maintaining the water content within acceptable limits, the risk of insulation degradation, reduced dielectric strength, and other associated problems can be minimized. Additionally, periodic water content analysis helps identify potential sources of water ingress and aids in the detection of leaks or malfunctioning components.
It is important to note that different transformer applications and standards may specify varying acceptable water content levels. Therefore, it is crucial to follow industry-specific guidelines and consult with experts to interpret the test results accurately.
The Water Content Test is a crucial aspect of transformer oil testing. By measuring the amount of water present in the oil, this test allows for the assessment of moisture levels and the identification of potential risks to the transformer’s insulation and performance. Regular water content analysis, alongside other oil testing methods, ensures the optimal functioning and longevity of transformers. By keeping the water content within acceptable limits, maintenance professionals can minimize the risk of electrical failures and preserve the transformer’s reliability.
Power Factor Test
The Power Factor Test is a significant component of transformer oil testing that helps assess the quality of the oil’s insulation and the overall condition of the transformer. This test plays a crucial role in measuring the power factor, which is an indicator of the dielectric loss and efficiency of the insulation system.
The power factor is a dimensionless quantity that represents the phase difference between the voltage and current in an AC circuit. In the context of transformer oil testing, the power factor is determined by applying an AC voltage to a sample of the oil and measuring the phase angle between the applied voltage and the resulting current. A high power factor indicates higher dielectric losses and decreased insulation efficiency.
By conducting the Power Factor Test, professionals can evaluate the effectiveness of the transformer oil in minimizing dielectric losses. The test is particularly useful in detecting potential issues such as contamination, degradation, or aging of the insulation materials. Higher power factors may indicate the presence of contaminants, moisture, or carbonized materials in the oil, leading to reduced insulation performance.
Regular Power Factor testing allows for the monitoring of the oil’s insulation condition over time. By comparing the power factor values obtained during different testing periods, maintenance professionals can identify trends and changes that may indicate insulation degradation or the need for maintenance. Early detection of increasing power factors can prompt further investigations or corrective actions to prevent potential failures.
The Power Factor Test is typically performed at a specific temperature, often close to the operating temperature of the transformer, to ensure accurate and reliable results. It is important to adhere to standardized procedures and guidelines during the test to maintain consistency and comparability of results.
In transformer oil testing, the Power Factor Test is an essential tool for evaluating insulation performance and identifying potential issues. By measuring the power factor, professionals can assess the quality of the oil’s insulation, detect any abnormalities, and take proactive measures to ensure the optimal performance and reliability of the transformer.
The Power Factor Test is a crucial aspect of transformer oil testing. By measuring the power factor, this test provides insights into the quality of the oil’s insulation and identifies potential issues that may affect transformer performance. Regular Power Factor testing allows for the monitoring of insulation condition and facilitates timely maintenance actions to prevent failures. Transformer oil testing, including the Power Factor Test, plays a vital role in maintaining the reliability and efficiency of transformers.
PCB (Polychlorinated Biphenyl) Analysis
PCB (Polychlorinated Biphenyl) Analysis is an integral part of transformer oil testing, specifically designed to identify and quantify the presence of PCBs in the oil. This analysis plays a crucial role in ensuring the safety and environmental compliance of transformer operations.
PCBs are synthetic organic compounds that were commonly used in electrical equipment, including transformers, due to their desirable electrical properties and heat resistance. However, due to their persistence in the environment and harmful effects on human health and ecosystems, the production and use of PCBs have been banned or restricted in many countries.
Transformer oil testing, including PCB Analysis, aims to detect the presence of PCBs and assess the level of contamination. PCBs can enter the transformer oil through leakage or improper disposal of old transformers that contained PCBs. The analysis involves extracting a representative oil sample and subjecting it to laboratory analysis using specialized techniques.
Gas chromatography (GC) is commonly employed in PCB Analysis. The oil sample is processed to separate and identify individual PCB congeners present in the oil. By comparing the chromatographic peaks with known reference standards, the type and concentration of PCBs in the oil can be determined.
Regular PCB Analysis is critical to ensure compliance with environmental regulations and prevent the release of harmful PCBs into the environment. The presence of PCBs in transformer oil poses risks to human health and ecosystems, and their proper handling and disposal are essential to avoid contamination.
If PCBs are detected in the oil, appropriate actions must be taken to address the situation. This may involve oil purification, transformer decontamination, or even replacement of the transformer if the PCB levels exceed regulatory limits. Proper disposal of PCB-contaminated oil is essential to prevent environmental pollution and protect public health.
Transformer oil testing, including PCB Analysis, plays a significant role in safeguarding the integrity of transformer operations. By detecting the presence of PCBs and assessing their levels, professionals can take necessary measures to ensure compliance with regulations, mitigate risks, and protect the environment. Regular testing and monitoring are essential to detect any changes in PCB levels and address potential contamination promptly.
PCB Analysis is a crucial component of transformer oil testing. It helps identify and quantify the presence of PCBs in transformer oil, ensuring compliance with environmental regulations and minimizing risks to human health and ecosystems. Regular testing and monitoring are essential to maintain the integrity of transformer operations and protect the environment from PCB contamination.
Furan Analysis
Furan Analysis is a significant component of transformer oil testing that focuses on measuring the levels of furanic compounds in the oil. This analysis plays a crucial role in assessing the condition of the transformer and the extent of degradation of its solid insulation materials.
Furanic compounds are formed as a result of the thermal degradation of cellulose, which is a primary component of the solid insulation materials in transformers. By analyzing the concentration of furans in transformer oil, professionals can gain valuable insights into the extent of degradation and the overall health of the transformer.
During the Furan Analysis, a representative sample of transformer oil is extracted, and the furanic compounds are quantified using analytical techniques such as gas chromatography (GC) or high-performance liquid chromatography (HPLC). The concentrations of specific furans, such as 2-furfural and its derivatives, are measured.
The levels of furans in transformer oil serve as indicators of the extent of degradation of the solid insulation materials. Higher concentrations of furans suggest increased thermal stress and degradation of cellulose, which can lead to reduced insulation performance and increased risk of electrical failures.
Regular Furan Analysis is essential for monitoring the condition of transformers over time. By comparing the furan concentrations obtained during different testing periods, maintenance professionals can identify trends and changes that may indicate accelerated degradation or the need for maintenance. Early detection of increasing furan levels can prompt further investigations or actions to prevent potential failures.
Furan Analysis provides valuable information for making informed decisions regarding transformer maintenance and asset management. By assessing the extent of insulation degradation, professionals can determine the appropriate course of action, such as oil purification, drying processes, or even the replacement of insulation materials.
The interpretation of furan analysis results requires considering various factors, including the transformer’s design, operating conditions, and historical data. Comparative analysis with established benchmarks or guidelines helps in assessing the severity of the insulation degradation and determining the appropriate actions.
Furan Analysis is a crucial aspect of transformer oil testing. By measuring the levels of furanic compounds in the oil, this analysis provides insights into the extent of degradation of the solid insulation materials and the overall condition of the transformer. Regular furan testing, alongside other oil analysis techniques, allows for the monitoring of insulation degradation and facilitates timely maintenance actions to ensure the longevity and reliability of transformers. Transformer oil testing, including Furan Analysis, is essential for effective asset management and preventing potential failures.
Visual Inspection
Visual Inspection is an essential component of transformer oil testing that involves a thorough examination of the transformer and its components to identify any visible signs of damage, corrosion, leaks, or other issues. This inspection is crucial for ensuring the overall condition and reliability of the transformer.
In transformer oil testing, visual inspection serves as a preliminary assessment tool before conducting more specific tests. It allows maintenance professionals to visually inspect the external condition of the transformer, oil storage tanks, cooling systems, bushings, and other components.
During a visual inspection, professionals look for various indicators that may suggest potential problems. These include:
- Physical Damage: Signs of physical damage such as dents, cracks, or deformities can indicate stress on the transformer and may require further investigation.
- Leaks: Any signs of oil leaks, coolant leaks, or moisture accumulation around the transformer should be carefully examined as they may indicate potential problems with seals, gaskets, or other components.
- Corrosion: Visual inspection helps identify any signs of corrosion on metal surfaces, including the transformer tank, radiators, or cooling fans. Corrosion can weaken the structural integrity of the transformer and lead to leaks or failures.
- Insulation Condition: The condition of insulation materials, such as the condition of bushings, gaskets, or cable connections, can be assessed during visual inspection. Any signs of deterioration, cracking, or degradation should be noted for further evaluation.
- Cooling Systems: The visual inspection includes checking the cooling systems, such as radiators or fans, to ensure they are clean and free from obstructions that could impede proper cooling.
Visual inspection is a valuable tool for detecting obvious visual defects and irregularities in transformer components. It helps in identifying potential areas of concern that may require further testing or maintenance actions. Regular visual inspections are recommended as part of a comprehensive maintenance program to ensure the safe and reliable operation of transformers.
While visual inspection is a critical step in transformer maintenance, it is important to note that it does not provide a comprehensive evaluation of the internal condition or oil quality. Therefore, it should be supplemented with more specific transformer oil testing methods to obtain a comprehensive assessment.
In conclusion, visual inspection is a crucial component of transformer oil testing. By visually examining the transformer and its components, maintenance professionals can identify visible signs of damage, leaks, corrosion, or other issues that may require further investigation or maintenance actions.
Regular visual inspections, along with other testing techniques, contribute to the overall assessment and maintenance of transformers, ensuring their reliability and longevity. Transformer Tests Before Commissioning are also vital for transformer long life span.
Follow us on LinkedIn”Electrical Insights” to get the latest updates in Electrical Engineering. You can also Follow us LinkedIn to see our latest posts.
Well Thanks. You can Try Rank Math. Further You can send your Queries at info@azadtechhub.com.
Casey Faulkner