Induction Motor: Important Types, Construction & Working
Table of Contents
Introduction to Induction Motor
Induction motor is the most widely used type of electric motors in various industrial and commercial applications. They are known for their simplicity, reliability, and efficiency, making them an essential component in numerous devices and machinery.
The invention of the induction motor by Nikola Tesla in the late 19th century revolutionized the world of electrical power and played a significant role in the industrial revolution.
An induction motor is an AC (alternating current) motor that operates based on the principles of electromagnetic induction. It converts electrical energy into mechanical energy, making it ideal for applications that require rotating machinery.
Induction motors are commonly found in appliances, pumps, fans, compressors, conveyors, and other equipment where mechanical power is essential.
The fundamental working principle of an induction motor involves the interaction of a rotating magnetic field with the rotor. The stator, the stationary part of the motor, consists of a laminated core with evenly spaced windings.
When an AC voltage is applied to the stator windings, it creates a rotating magnetic field that rotates at the same frequency as the applied voltage.
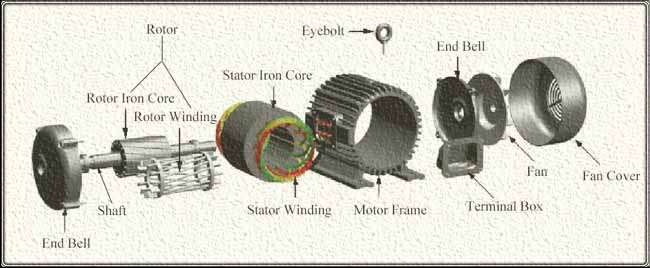
The rotor, on the other hand, is the rotating part of the motor. It can be constructed with various types of rotors, such as squirrel cage and wound rotor. The squirrel cage rotor is the most common type due to its simplicity and ruggedness.
It consists of laminated iron cores with conducting bars placed in slots and shorted at both ends. When the rotating magnetic field from the stator cuts across the rotor conductors, it induces a voltage and current, creating a magnetic field in the rotor.
According to Lenz’s law, the induced current in the rotor produces a magnetic field that opposes the rotating magnetic field of the stator. As a result, the rotor experiences a torque that tries to catch up with the rotating magnetic field.
This difference in speed between the rotating magnetic field and the rotor causes the rotor to rotate in the same direction as the rotating magnetic field but at a slightly slower speed, known as slip.
The slip is necessary for the induction motor to generate torque. As the rotor accelerates, the slip decreases until it reaches a steady-state value where the torque produced by the motor balances the load torque.
This operating point is called the synchronous speed, which is determined by the number of poles and the frequency of the applied voltage.
One of the significant advantages of induction motors is their self-starting capability. When an AC voltage is applied, the rotating magnetic field is established, and the interaction with the rotor induces currents, providing the necessary torque to initiate rotation.
This eliminates the need for external starting devices in most applications, simplifying the motor’s design and reducing costs.
Induction motors are known for their robustness, as they have no brushes or commutators that require maintenance or cause wear. They are also highly efficient, typically ranging from 85% to 97%, depending on the motor size and design.
Furthermore, induction motors can operate at various speeds by utilizing methods such as variable frequency drives (VFDs) or changing the number of poles.
Induction motors are versatile, reliable, and efficient devices that have become the workhorses of modern industries. Their ability to convert electrical energy into mechanical energy through electromagnetic induction makes them indispensable for countless applications.
From small household appliances to large industrial machinery, These motors play a crucial role in powering the world around us.
Induction Motor working principle
The working principle of an induction motor is based on the principles of electromagnetic induction. It involves the interaction of a rotating magnetic field with the rotor, which enables the motor to convert electrical energy into mechanical energy.
The basic components of motor include the stator, rotor, and the air gap between them. The stator is the stationary part of the motor and is comprised of a laminated iron core with evenly spaced windings.
These windings are typically made of copper or aluminum and are connected to an AC power supply. The number of windings and their arrangement determine the motor’s operating characteristics.
When an AC voltage is applied to the stator windings, it generates an alternating magnetic field that rotates at the same frequency as the applied voltage. This rotating magnetic field induces voltage and current in the rotor. The rotor, which is the rotating part of the motor, consists of a laminated iron core with conducting bars or “squirrel cage” placed in slots. The conducting bars are short-circuited at both ends.
As the rotating magnetic field from the stator cuts across the rotor conductors, it induces a voltage and current in the rotor. According to Faraday’s law of electromagnetic induction, the changing magnetic field induces a voltage in the rotor conductors, causing a flow of current. This current generates a magnetic field in the rotor, known as the rotor magnetic field.
According to Lenz’s law, the induced current in the rotor produces a magnetic field that opposes the rotating magnetic field of the stator. As a result, the rotor experiences a torque that tries to catch up with the rotating magnetic field. This torque causes the rotor to rotate in the same direction as the rotating magnetic field but at a slightly slower speed.
The difference in speed between the rotating magnetic field of the stator and the rotor is called slip. Slip is necessary for the induction motor to generate torque. If the rotor were to rotate at the same speed as the stator’s rotating magnetic field, there would be no relative motion between the two, and no torque would be produced.
The rotor’s slip enables the induction motor to produce torque, which allows it to drive mechanical loads. As the rotor accelerates, the slip decreases until it reaches a steady-state value where the torque produced by the motor balances the load torque.
This operating point is called the synchronous speed, which is determined by the number of poles and the frequency of the applied voltage.
The speed of the rotating magnetic field, and therefore the synchronous speed, is determined by the frequency of the applied voltage and the number of poles in the motor. The synchronous speed (Ns) of an induction motor can be calculated using the formula:
Ns = (120 x f) / P
where Ns is the synchronous speed in revolutions per minute (RPM), f is the frequency of the applied voltage in hertz (Hz), and P is the number of poles.
It’s important to note that the induction motor does not reach the synchronous speed. The actual speed of the rotor is always slightly lower than the synchronous speed due to slip, which allows the motor to produce torque.
The working principle of an induction motor involves the creation of a rotating magnetic field in the stator, which induces voltage and current in the rotor. The interaction between the rotating magnetic field and the rotor’s induced current generates torque, enabling the motor to rotate and drive mechanical loads.
The slip between the rotating magnetic field and the rotor allows the motor to operate at a speed slightly lower than the synchronous speed, ensuring torque production.
Induction Motor construction
Induction motors are composed of several essential components that work together to convert electrical energy into mechanical energy.
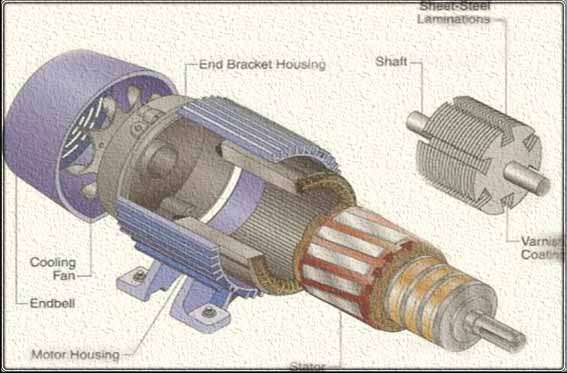
Let’s explore the construction of an induction motor in detail:
Stator
The stator is the stationary part of the motor and is responsible for generating the rotating magnetic field. It consists of a laminated iron core, which reduces eddy current losses, and slots for housing the stator windings. The stator windings are typically made of copper or aluminum and are placed in the slots. The number of windings and their arrangement determine the motor’s operating characteristics, such as the number of poles.
Rotor
The rotor is the rotating part of the induction motor. It is responsible for reacting to the rotating magnetic field generated by the stator and producing mechanical torque. Induction motors can have different types of rotors, such as squirrel cage rotors, wound rotors, or double squirrel cage rotors.
Squirrel Cage Rotor
The squirrel cage rotor is the most common type of rotor in induction motors. It consists of a laminated iron core with conducting bars placed in slots. The conducting bars are typically made of aluminum or copper and are shorted at both ends by conducting end rings.
This design resembles a squirrel cage, giving it the name “squirrel cage rotor.” The simplicity and ruggedness of the squirrel cage rotor make it widely used in various applications.
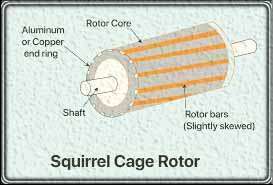
Wound Rotor
The wound rotor, also known as a slip ring rotor, consists of a laminated iron core with separate rotor windings. These windings are made of insulated coils and are connected to external resistors through slip rings and brushes.
The slip rings allow external electrical connections to the rotor windings, providing flexibility in controlling the motor’s speed and torque characteristics.
Air Gap
The air gap is the space between the stator and the rotor. It plays a crucial role in the motor’s operation by allowing the magnetic field from the stator to interact with the rotor.
The air gap is carefully designed to ensure an optimal magnetic coupling between the stator and the rotor, maximizing the motor’s performance.
Bearings
Bearings support the rotor and allow it to rotate smoothly. Induction motors typically use two types of bearings: sleeve bearings and ball bearings. Sleeve bearings are plain bearings that provide support and reduce friction between the rotor and the stator. Ball bearings, on the other hand, use rolling balls to reduce friction and provide smoother rotation.
Frame
The frame is the outer structure of the motor that encloses and protects the internal components. It is usually made of cast iron or aluminum and provides mechanical strength and stability to the motor.
The frame also serves as a mounting point for the motor and provides cooling through external fins or ventilation systems.
Terminal Box
The terminal box is located on the motor’s exterior and provides access to the motor’s electrical connections. It houses terminals for connecting the stator windings to the external power supply. The terminal box ensures proper electrical connection and allows for easy maintenance and troubleshooting.
The construction of an induction motor involves the stator, rotor, air gap, bearings, frame, and terminal box. These components work together to convert electrical energy into mechanical energy. The specific design and arrangement of these components vary depending on the motor’s type, size, and intended application.
Induction Motor torque speed characteristics
The torque-speed characteristics of an induction motor describe the relationship between the motor’s torque and its rotational speed. These characteristics are essential for understanding the motor’s performance and determining its suitability for various applications.
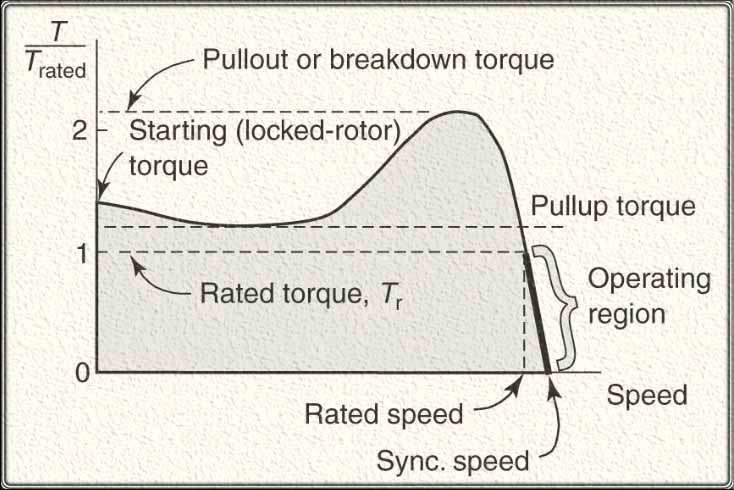
Let’s explore the torque-speed characteristics of an induction motor:
Starting Torque
The starting torque is the torque produced by the motor when it is initially energized. Induction motors provide high starting torque, known as “pull-up” torque. The starting torque is typically 1.5 to 2 times the full-load torque.
This high starting torque allows the motor to overcome the initial inertia and accelerate the load from a stationary position.
Pull-up Torque
The pull-up torque is the minimum torque required to accelerate the motor to its rated speed without stalling or falling out of synchronism. It is the torque at which the motor transitions from a static condition to a rotating condition.
The pull-up torque is an important characteristic as it determines the motor’s ability to start and accelerate loads.
Full-Load Torque
The full-load torque is the torque produced by the motor when operating at its rated load. It is the torque required to maintain the motor’s rated speed under normal operating conditions.
The motor should be capable of delivering sufficient full-load torque to meet the demands of the connected load.
Breakdown Torque
The breakdown torque is the maximum torque that the motor can produce without stalling or damaging itself. If the load torque exceeds the breakdown torque, the motor will stall and stop rotating.
The breakdown torque is an important consideration when selecting a motor for applications with high starting or intermittent peak torque requirements.
Torque-Speed Curve
The torque-speed curve is a graphical representation of the torque-speed characteristics of an induction motor. It illustrates how the motor’s torque output varies with changes in speed. The curve typically exhibits the following characteristics:
- Starting Torque: The torque at zero speed, which is the maximum torque produced by the motor.
- Pull-up Torque: The torque at which the motor transitions from zero speed to acceleration.
- Full-Load Torque: The torque at the motor’s rated speed when operating at full load.
- Breakdown Torque: The maximum torque that the motor can produce before stalling.
Synchronous Speed
The speed at which the motor operates when the rotor speed matches the speed of the rotating magnetic field generated by the stator.
Slip
The difference between the synchronous speed and the actual rotor speed of the motor. The slip is necessary for torque generation in an induction motor.
The torque-speed characteristics of an induction motor are influenced by factors such as the motor’s design, rotor resistance, supply voltage, and load conditions. Understanding these characteristics helps in selecting the appropriate motor for specific applications, ensuring efficient and reliable motor operation.
equations of induction motor
The equations governing the operation of an induction motor are derived from the fundamental principles of electromagnetism and motor theory. Here are some of the key equations related to induction motors:
Slip (S): Slip is the difference between the synchronous speed (Ns) and the actual rotor speed (N). It is given by the equation:
S = (Ns – N) / Ns
Rotor Frequency (fr): The rotor frequency is the frequency of the rotor currents induced by the rotating magnetic field of the stator. It is related to slip and the supply frequency (f) by the equation:
fr = S × f
Rotor Slip Frequency (s): The rotor slip frequency is the frequency of the rotor currents relative to the synchronous speed. It is given by the equation:
s = S × f / p
where p is the number of poles of the motor.
Torque (T): The torque produced by the motor is directly proportional to the square of the stator current (I1), the number of poles (p), and the rotor slip frequency (s). The torque equation is:
T = (3 × V1 × I1 × cos(θ)) / (2 × π × fr) × (1 – S)
where V1 is the stator voltage and θ is the angle between the stator voltage and stator current.
Power Factor (PF): The power factor of motor is the cosine of the angle between the stator voltage and stator current. It is given by the equation:
PF = cos(θ)
Electrical Power (P): The electrical power consumed by the motor is given by the equation:
P = Sqrt (3) × V1 × I1 × PF
Speed (N): The actual speed of the rotor is related to the synchronous speed and slip by the equation:
N = (1 – S) × Ns
These equations provide a mathematical representation of the performance characteristics of an induction motor. They are used in motor design, analysis, and control to understand and predict the motor’s behavior under different operating conditions.
Induction Motor types
Induction motors are available in different types, each designed for specific applications and operating conditions. The two most common types of induction motors are squirrel cage induction motors and wound rotor induction motors.
Squirrel Cage Induction Motors
Squirrel cage motors are the most widely used type of induction motors due to their simplicity, ruggedness, and low maintenance requirements. They are called “squirrel cage” motors because of the rotor design, which resembles a squirrel cage wheel.
In a squirrel cage induction motor, the rotor consists of a laminated iron core with short-circuited conducting bars placed in slots. The conducting bars are typically made of aluminum or copper.
The ends of the bars are shorted together by conducting end rings. This rotor design allows for robust construction and high resistance to mechanical stress.
Squirrel cage motors do not have any external electrical connections to the rotor. Instead, the rotor bars and end rings are permanently short-circuited. When the rotating magnetic field from the stator cuts across the rotor conductors, it induces a voltage and current in the rotor.
The induced current creates a magnetic field in the rotor, which interacts with the rotating magnetic field from the stator to produce torque. The torque causes the rotor to rotate in the same direction as the stator’s rotating magnetic field but at a slightly slower speed.
Squirrel cage motors are known for their reliability, high starting torque, and self-starting capability. They are commonly used in applications such as pumps, fans, compressors, conveyors, and other industrial machinery.
Wound Rotor Induction Motors
Wound rotor induction motors, also known as slip ring motors, have a rotor design that differs from squirrel cage motors. Instead of short-circuited rotor bars, the rotor windings are made of insulated coils that are connected to external resistors through slip rings and brushes. The slip rings allow for external electrical connections to the rotor windings.
Wound rotor motors offer certain advantages over squirrel cage motors. The external electrical connections to the rotor windings provide flexibility in controlling the motor’s speed and torque characteristics.
By adjusting the resistance connected to the rotor windings through the slip rings, the starting torque and speed can be controlled. This makes wound rotor motors suitable for applications that require high starting torque, such as large pumps, crushers, mills, and hoists.
Additionally, wound rotor motors can be used with external devices called rheostats or variable resistors to control motor speed. This makes them suitable for applications where speed control is necessary, such as conveyors, mixers, and cranes.
However, wound rotor motors have a higher initial cost due to the additional components (slip rings, brushes, and external resistors) and require periodic maintenance of the slip rings and brushes.
Double Squirrel Cage Induction Motors
Double squirrel cage induction motors are a specialized type of squirrel cage motor that provides enhanced performance characteristics. They have two sets of rotor windings, the main cage winding, and the auxiliary winding.
The main cage winding is similar to the rotor winding in a regular squirrel cage motor, while the auxiliary winding consists of higher-resistance rotor bars placed closer to the rotor surface.
The presence of the auxiliary winding provides improved torque characteristics and higher starting torque.
Double squirrel cage motors are commonly used in applications where high torque is required during starting or where the load conditions vary widely, such as in crushers, pumps, and fans.
In conclusion, squirrel cage motors, wound rotor induction motors, and double squirrel cage motors are the main types of induction motors. Each type offers specific advantages and is suited for different applications.
Squirrel cage motors are simple, reliable, and widely used, while wound rotor motors provide speed and torque control. Double squirrel cage motors offer enhanced torque characteristics for demanding applications.
Applications of Induction Motor
Induction motors are widely used in various industrial, commercial, and residential applications due to their reliability, efficiency, and versatility. Let’s explore the applications of induction motors in detail:
Industrial Machinery
Induction motors are extensively used in industrial machinery, such as pumps, compressors, fans, blowers, mixers, conveyors, and machine tools. These motors provide the necessary mechanical power to drive these devices efficiently. Their robust construction and ability to handle heavy loads make them ideal for demanding industrial environments.
HVAC Systems
Heating, ventilation, and air conditioning (HVAC) systems heavily rely on induction motors. They are used in air handling units, fans, blowers, and condenser units. Induction motors provide efficient and reliable operation for air circulation, cooling, and heating in residential, commercial, and industrial buildings.
Water Treatment and Pumping Systems
Induction motors play a crucial role in water treatment plants and pumping systems. They are used to drive pumps that transport water for various purposes, including water supply, wastewater management, irrigation, and drainage. The high starting torque and robust construction of motors make them suitable for pumping applications.
Automotive Industry
Induction motors are increasingly being utilized in electric and hybrid vehicles. They power the vehicle’s propulsion system, providing torque and speed control. Induction motors offer high efficiency and reliability, contributing to the overall performance of electric vehicles.
Household Appliances
Numerous household appliances utilize induction motors for their operation. Examples include refrigerators, washing machines, dryers, dishwashers, vacuum cleaners, and kitchen appliances like blenders and mixers. Induction motors deliver the necessary rotational motion and power for various functions in these appliances.
Renewable Energy Systems
Induction motors are employed in renewable energy systems, such as wind turbines and hydroelectric generators. They convert the rotational motion of wind or water into electrical energy. Induction motors in these applications are often coupled with generators to produce electricity from renewable sources.
Material Handling and Conveyor Systems
Induction motors are widely used in material handling equipment and conveyor systems found in factories, warehouses, and airports. They provide the power and control needed to move goods and materials efficiently along the conveyor belts or within handling equipment like cranes, lifts, and forklifts.
Mining and Extraction
In the mining industry, induction motors are employed in crushers, grinders, pumps, fans, and hoists. These motors withstand harsh operating conditions and deliver reliable performance in extracting and processing minerals.
Agriculture and Farming
Induction motors find applications in agriculture and farming equipment, including irrigation systems, crop processing machinery, grain handling systems, and livestock feeders. They power machinery for planting, harvesting, and processing agricultural products.
Commercial Appliances
Commercial appliances, such as commercial refrigerators, freezers, ovens, and food processors, utilize induction motors for their operations. These motors offer efficient and reliable performance in commercial kitchens, food processing facilities, and other commercial establishments.
In summary, induction motors are utilized in a wide range of applications, including industrial machinery, HVAC systems, water treatment, automotive industry, household appliances, renewable energy systems, material handling, mining, agriculture, and commercial appliances.
Their versatility, reliability, and efficiency make them indispensable in various sectors, driving essential processes and providing mechanical power for countless applications.
Induction Motor vs synchronous motor
Induction motors and synchronous motors are two types of AC motors with distinct operating principles and characteristics. Let’s compare them in detail:
Operating Principle:
Induction Motor: An induction motor operates based on the principle of induction. It generates a rotating magnetic field in the stator, which induces voltage and current in the rotor.
The rotor currents produce a magnetic field that interacts with the stator’s rotating magnetic field, generating torque and causing the rotor to rotate. The speed of the rotor is slightly lower than the synchronous speed due to slip.
Synchronous Motor: A synchronous motor operates by synchronizing its rotor’s speed with the speed of the rotating magnetic field generated by the stator. The rotor has either permanent magnets or DC excitation windings. When the stator’s rotating magnetic field interacts with the rotor’s magnetic field, the rotor locks in sync with the rotating magnetic field, resulting in zero slip. As a result, the rotor speed is always equal to the synchronous speed.
Speed Control:
Induction Motor: Induction motors have inherent speed control limitations. The speed of an induction motor is primarily determined by the frequency of the applied voltage and the number of poles.
Changes in load conditions may cause slight variations in speed, but significant speed control is not achievable without additional devices or complex control methods.
Synchronous Motor: Synchronous motors offer precise speed control. By adjusting the field excitation or the frequency of the applied voltage, the speed of a synchronous motor can be precisely controlled.
This feature makes synchronous motors suitable for applications that require constant speed control, such as industrial processes and power generation.
Starting Torque:
Induction Motor: Induction motors provide high starting torque, known as the “pull-up” torque. This torque allows the motor to start and accelerate loads without requiring additional starting devices.
The high starting torque makes induction motors suitable for applications that demand high initial torque, such as pumps, fans, and conveyors.
Synchronous Motor: Synchronous motors have lower starting torque compared to induction motors. They require additional starting devices, such as damper windings or external prime movers, to overcome the initial inertia and achieve synchronous operation.
Synchronous motors are commonly used in applications where high starting torque is not critical, such as power generation and industrial processes with constant loads.
Power Factor:
Induction Motor: Induction motors have a power factor that can vary based on load conditions. Under light load or no-load conditions, induction motors have a lower power factor, which can lead to inefficient power usage. Power factor correction capacitors are often used to improve the power factor of induction motors and reduce reactive power consumption.
Synchronous Motor: Synchronous motors operate at a unity power factor, which means they have a power factor of 1. They do not consume reactive power, making them efficient in terms of power factor. Synchronous motors are often used in applications where maintaining a high power factor is crucial, such as in power plants and large industrial installations.
Efficiency:
Induction Motor: Induction motors are known for their high efficiency. They can achieve efficiency levels of 85% to 95%, depending on the motor size and operating conditions. The efficiency of induction motors remains relatively high across a wide range of loads.
Synchronous Motor: Synchronous motors also offer high efficiency. However, their efficiency is typically lower compared to induction motors. Efficiency levels of synchronous motors range from 85% to 95%, similar to induction motors. Synchronous motors achieve their highest efficiency at full load and unity power factor.
Induction motors and synchronous motors have different operating principles and characteristics. Induction motors provide high starting torque, operate at a slightly lower speed than the synchronous speed, and have inherent speed limitations.
On the other hand, synchronous motors offer precise speed control, operate at synchronous speed, and have a unity power factor. The choice between the two depends on specific application requirements, such as the need for speed control, starting torque, and power factor considerations.
Induction Motor Controller and Protection System:
To ensure the safe and reliable operation of induction motors, various control and protection systems are employed. These systems help monitor and control motor performance, prevent damage, and ensure efficient operation. Let’s explore the typical controller and protection systems used for induction motors:
Motor Starter:
A motor starter is used to control the motor’s start and stop operations. It typically consists of a contactor, overload relay, and control circuitry. The motor starter allows for manual or automatic control of motor operations, providing protection against motor overheating and overloading.
Variable Frequency Drive (VFD):
A Variable Frequency Drive, also known as a VFD or AC drive, is an electronic controller that regulates the speed and torque of an induction motor. It allows for precise control of motor speed by varying the frequency and voltage supplied to the motor. VFDs are commonly used in applications where speed control, energy efficiency, and process optimization are required.
Soft Starter:
A soft starter is an electronic device used to gradually start and stop the motor by controlling the voltage applied during startup. It reduces the inrush current, minimizing stress on the motor and associated equipment. Soft starters provide smoother acceleration, reducing mechanical shocks and extending motor life.
Motor Protection Relays:
Motor protection relays monitor the operating conditions of the motor and provide protection against various electrical faults and abnormalities. Some common protection features provided by motor protection relays include:
Overload Protection: Monitors the motor’s current and protects against excessive current that could lead to overheating and damage.
Overvoltage/Undervoltage Protection: Monitors the voltage supply to the motor and protects against voltage fluctuations outside the acceptable range.
Phase Loss/Phase Imbalance Protection: Detects phase loss or imbalance, preventing the motor from running under abnormal conditions.
Short Circuit Protection: Protects the motor against short circuits by quickly disconnecting the power supply in case of a fault.
Thermal Protection: Monitors the motor’s temperature and activates alarms or trips the motor if the temperature exceeds safe limits.
Ground Fault Protection: Detects ground faults and provides protection against insulation breakdown or electrical shock hazards.
Reverse Power Protection: Protects the motor from damage due to reverse power flow when the motor acts as a generator.
Communication and Diagnostic Functions: Some advanced motor protection relays offer communication capabilities to monitor motor performance, record fault events, and provide diagnostic information for maintenance and troubleshooting purposes.
Grounding and Earthing Systems: Proper grounding and earthing systems are essential for the safe operation of induction motors. Grounding provides a path for fault currents, protecting equipment and personnel from electrical hazards. Effective grounding reduces the risk of electrical shocks, helps clear ground faults quickly, and ensures stable motor operation.
Induction motor control and protection systems include motor starters, variable frequency drives (VFDs), soft starters, motor protection relays, and grounding/earthing systems.
These systems help regulate motor speed, protect against electrical faults, prevent damage, and ensure safe and efficient motor operation. The selection and implementation of these systems depend on the specific requirements of the motor application and the level of protection desired.
frequently asked questions
What is an induction motor?
An induction motor is an AC motor that operates based on the principle of induction, where a rotating magnetic field in the stator induces voltage and current in the rotor, resulting in the generation of torque and rotation.
How does an induction motor work?
An induction motor works by inducing a magnetic field in the rotor through the interaction of the rotating magnetic field in the stator. This induced magnetic field creates a force that produces torque and causes the rotor to rotate.
What are the types of induction motors?
The two main types of induction motors are squirrel cage induction motors and wound rotor induction motors. Squirrel cage motors have a rotor with short-circuited conductors, while wound rotor motors have a rotor with externally connected variable resistors or windings.
The two main types of induction motors are squirrel cage induction motors and wound rotor induction motors. Squirrel cage motors have a rotor with short-circuited conductors, while wound rotor motors have a rotor with externally connected variable resistors or windings.
What are the advantages of induction motors?
Some advantages of induction motors include their simple and robust construction, high reliability, low cost, and ability to provide high starting torque.
What are the applications of induction motors?
Induction motors are widely used in various applications, including industrial machinery, pumps, fans, compressors, conveyor systems, HVAC systems, and household appliances.
Can induction motors be controlled for speed?
While induction motors have inherent speed limitations, their speed can be controlled to some extent using methods such as changing the supply frequency, using variable frequency drives (VFDs), or employing mechanical methods like gears or belts.
How efficient are induction motors?
Induction motors are known for their high efficiency. Depending on the motor size and operating conditions, they can achieve efficiency levels ranging from 85% to 95%.
Do induction motors require maintenance?
Induction motors are relatively low-maintenance machines. Regular maintenance involves inspecting and lubricating the motor, checking for proper alignment, and monitoring the motor’s temperature and vibration levels.
Can induction motors generate electricity?
While induction motors are primarily used as motors, they can also operate in reverse as generators under certain conditions. This phenomenon is known as regenerative braking or regenerative operation.
How do induction motors differ from synchronous motors?
Induction motors and synchronous motors differ in their operating principles. Induction motors operate at a speed slightly lower than the synchronous speed and do not require external DC excitation. In contrast, synchronous motors operate at synchronous speed and require either permanent magnets or DC excitation to synchronize with the rotating magnetic field.
Worth Read Posts
Follow us on LinkedIn”Electrical Insights” to get the latest updates in Electrical Engineering. You can also Follow us on LinkedIn and Facebook to see our latest posts on Electrical Engineering Topics.