IGBT Transistor: Important Guide
The MOSFET and BJT benefits are combined in the Insulated Gate Bipolar Transistor, also known as the IGBT transistor. Due to its high voltage and current carrying capacity, as well as its superior switching characteristics, it is widely employed in a variety of applications. We will go into the IGBT transistor, its less-discussed properties, and its uses in this thorough discussion.
Tabel of Contents
Table of Contents
IGBT Transistor: PIN Configuration
The gate (G), collector (C), and emitter (E) are typically the three major terminals that make up the pin arrangement of an IGBT Transistor. Controlling the flow of current through the IGBT depends on these terminals. Let’s discuss the pin configuration and its purposes:
Gate (G): The gate terminal is used to control the IGBT’s conductivity. When a voltage is applied to the gate terminal, it creates an electric field that allows or inhibits the flow of current between the collector and the emitter. By varying the voltage on the gate, the IGBT can be switched between the on and off states.
Collector (C): The collector terminal is where the main current flows through the IGBT. It acts as the output terminal, carrying the load current from the power supply to the load. The collector terminal is connected to the positive side of the circuit in most applications.
Emitter (E): The emitter terminal is the output for the IGBT’s current. It allows the current to flow from the collector to the emitter when the IGBT is in the “on” state. The emitter terminal is connected to the load or ground in most applications.
The typical pin configuration of an IGBT is as follows:
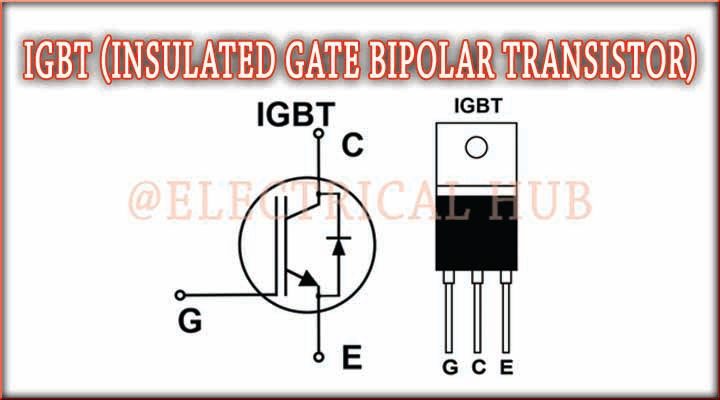
It’s vital to remember that the IGBT’s manufacturer and package type may affect the specific pin configuration. The pin configuration of the IGBT can vary slightly depending on the package used, including TO-220, TO-247, and module packages. Because of this, it’s crucial to refer to the datasheet supplied by the manufacturer when using IGBTs in your circuits for the precise pinout of the particular IGBT device you are dealing with.
Construction of IGBT Transistor
Each layer and component used in the development of an IGBT (Insulated Gate Bipolar Transistor) is essential to the device’s functionality.
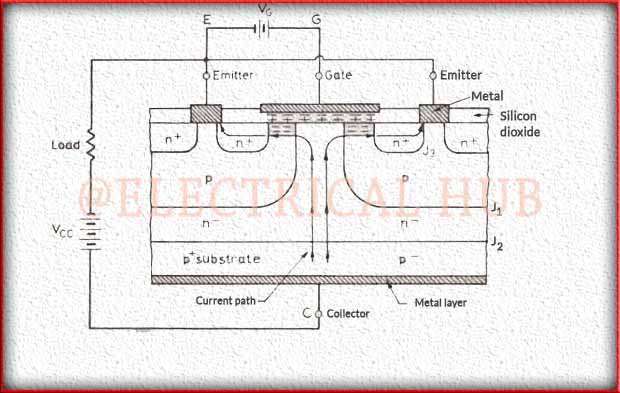
Here is a brief explanation of how an IGBT is built:
IGBTs are commonly built on silicon wafers, which act as the semiconductor’s foundation material. The semiconductor qualities of silicon, which enable precise control of current flow, led to its selection.
P-type Layer: The silicon wafer is doped with a small amount of P-type impurities, creating a region with an excess of positive charge carriers (holes). This region is known as the P-type layer.
N-type Layer: Adjacent to the P-type layer, another region of the silicon wafer is doped with N-type impurities, creating an excess of negative charge carriers (electrons). This region is called the N-type layer.
Gate Electrode: The N-type layer’s surface is covered by a metal or polysilicon gate electrode. Typically made of silicon dioxide (SiO2), the thin insulating layer that separates the semiconductor material from this gate electrode is formed of this substance.
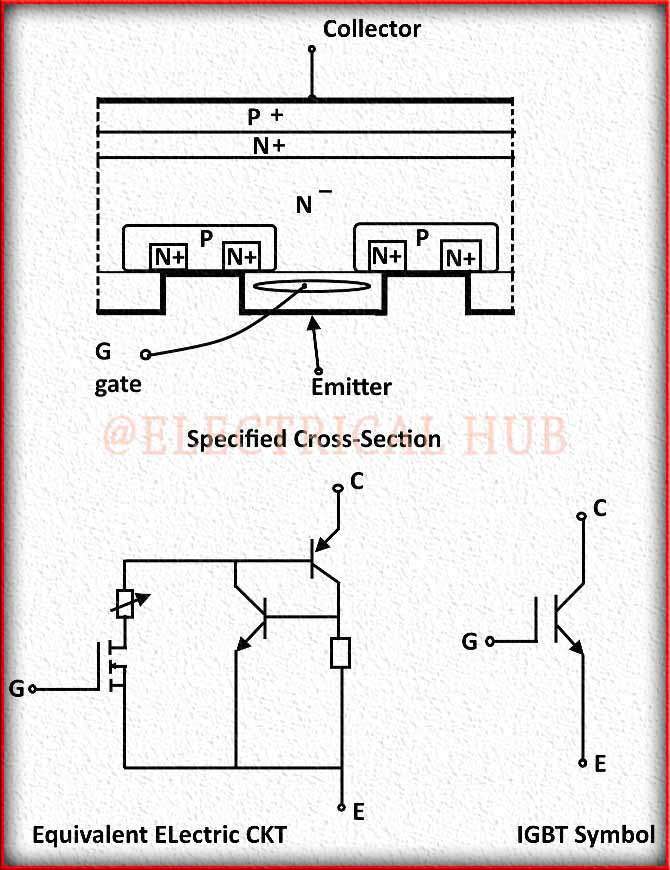
The development of an N-channel (conductive conduit) between the collector and emitter is made possible by an electric field created in the N-type layer when a voltage is supplied to the gate electrode. The gate voltage regulates this channel.
Insulating Layer: To avoid leakage current between the gate and the rest of the device, an insulating layer is placed between the gate electrode and the semiconductor material.
IGBT modules are frequently installed on a baseplate that also has a heatsink to disperse heat produced during operation. The performance and dependability of the IGBT must be kept in good condition.
The gate voltage regulates the IGBT’s conductivity during operation, enabling it to switch current between the collector and emitter. IGBTs are widely utilized in many different applications, such as voltage regulation in electrical systems, power inverters, and motor drives. They are suitable for handling high-voltage and high-current applications due to their build and design.
Equivalent Circuit of IGBT Transistor
The equivalent circuit of an IGBT transistor can be shown below:
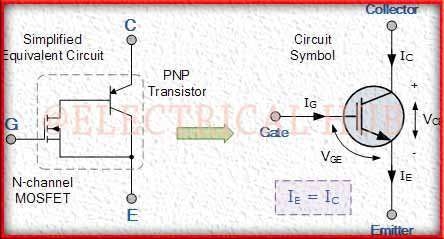
Features of IGBT Transistor
Operating Principle: The IGBT transistor has a gate (G), collector (C), and emitter (E), making it a three-terminal device. It functions using both MOSFET and BJT principles. The gate regulates the movement of current between the emitter and collector. The transistor may alternate between the on and off states by applying a voltage to the gate.
Voltage Rating: A few hundred volts to several thousand volts are the voltage ratings that IGBT transistors can withstand. This qualifies them for high-power uses such as power inverters and motor drives for renewable energy systems.
Current-Carrying Capability: IGBTs have a high current carrying capacity that can range from a few amperes to several hundred amperes, depending on the device’s size and design. Power electronics are widely employed in industrial applications, so having a high current-handling capacity is crucial.
Low On-State Voltage Drop: IGBT transistors have a low on-state voltage drop (Vce), which is one of their special characteristics. This characteristic reduces power losses during conduction, which increases their efficiency.
Fast Switching Characteristics: Turn-on and turn-off times for IGBTs are typically in the microsecond range. This characteristic is essential in applications that call for precise control, like variable-speed motor drives and induction heating.
Temperature Tolerance: IGBTs are renowned for their durability in high-temperature situations because of their tolerance to temperature. Some variations can endure extremely high temperatures, which qualifies them for use in demanding industries like energy systems, aerospace, and automobiles.
Short-Circuit Current Rating (SCCR): A crucial but frequently ignored component is short-circuit current rating (SCCR). The IGBT’s SCCR rating shows how well it can survive short-circuit circumstances without irreparable damage. In industrial environments where short-circuit events can happen, IGBT transistors with a high SCCR are more secure to utilize.
Overcurrent Protection: Integrated overcurrent protection techniques are frequently included with IGBT modules. These safeguards may be crucial in avoiding harm to the transistor and the system as a whole.
IGBT Transistor Types
Insulated Gate Bipolar Transistors (IGBTs) come in a variety of forms and combinations, each suited to certain uses and specifications. The voltage and current ratings, switching rates, packaging, and other properties of these IGBT types vary. Here are a few prevalent IGBT types:
Standard IGBT:
- These are the IGBTs that are used most frequently.
- They are appropriate for a variety of uses, including motor drives, power inverters, and welding equipment.
- offered in a range of voltage and current levels.
High-Voltage IGBT:
- Designed for high-voltage applications that often require capabilities between 1,200 and several thousand volts.
- Used in electric grid systems, high-voltage inverters, and power transmission and distribution.
Low-Voltage IGBT:
- Ideal for applications requiring low voltage, often 600 volts or less.
- used in compact inverters, low-power motor drives, and consumer electronics.
Fast-Switching IGBT:
- These IGBTs have quicker turn-on and turn-off timings and improved switching speeds.
- suitable for uses like high-frequency inverters and resonant converters that call for precise control and minimal switching losses.
Soft-Switching IGBT:
- Designed to minimize electromagnetic interference (EMI) and switch losses.
- Used in applications like induction heating and resonant converters where EMI minimization and efficiency enhancement are crucial.
IGBT Modules:
- IGBTs are frequently sold as modules that also include built-in diodes and protection systems in addition to the IGBT itself.
- Available in a range of configurations, including three-phase, full-bridge, and half-bridge modules.
- Frequently employed in high-power applications such as traction systems, wind turbine inverters, and motor drives.
Reverse Conducting IGBT (RC-IGBT):
- These IGBTs have an inbuilt diode that enables the flow of reverse current.
- used in applications like motor drives and regenerative braking systems where bidirectional current flow is necessary.
Ultra-Fast IGBT:
- designed for applications requiring minimal switching losses and incredibly high switching rates.
- frequently employed in pulse-width modulation (PWM) inverters for server and telecom power supplies, among other high-frequency applications.
IGBT Stacks:
- To manage even higher voltage and current demands, these systems combine several IGBTs coupled in series or parallel.
- frequently employed in specialized applications, such as high-voltage DC transmission systems.
Integrated IGBT (I-IGBT):
- The design of power electronic systems is made simpler by the incorporation of other components like gate drivers and protective circuits on the same chip in these IGBTs.
- Used in applications where the amount of space and components is limited, like automotive power modules.
It’s critical to take switching characteristics, required level of integration, voltage and current requirements into account when choosing an IGBT for a particular application. Your power electronics systems will run as effectively and efficiently as possible if you choose the proper IGBT type.
IGBT Transistor Applications
Motor Drives: The precise control of electric motors is made possible by the widespread usage of IGBT transistors in motor drives. They are perfect for uses like electric vehicles, industrial robots, and CNC machines thanks to their quick switching rates and high current capacities.
Power Inverters: IGBTs, which transform DC power into AC power, are at the center of power inverters. Effective energy conversion is essential in renewable energy systems like solar inverters and wind turbine converters.
Induction Heating: IGBTs are suited for induction heating applications such as in the metalworking sector for hardening, annealing, and brazing processes because to their quick switching and high current handling capabilities.
Welding Machines: IGBT transistors are widely used in welding machines because of their propensity for handling large currents and voltages. For diverse welding procedures, they provide the necessary power control, providing high-quality welds.
Uninterruptible Power Supplies (UPS): IGBT transistors provide for a smooth transition between grid power and backup power sources in UPS systems. They are essential for maintaining important loads during power outages because of their efficiency and dependability.
In conclusion, the IGBT transistor has evolved into a critical part in numerous industrial and power electronics applications due to its exceptional combination of high voltage and current ratings, low on-state voltage drop, and fast switching capabilities.
IGBT transistor characteristics, like SCCR and temperature endurance, let it become widely used in challenging conditions and ensure reliable and effective operation across a variety of industries. Engineers and designers can choose wisely when integrating IGBT transistors into their systems once they are armed with this knowledge.
Worth Read Posts
Follow Us on Social:
Subscribe our Newsletter on Electrical Insights to get the latest updates in Electrical Engineering.
#IGBT, #TransistorTechnology, #PowerElectronics, #SemiconductorDevices, #IGBTModule, #IGBTApplications, #IGBTSwitch, #ElectronicComponents, #HighPowerTransistor, #MOSFETvsIGBT, #ElectricalEngineering, #IGBTCircuit, #TechExplained, #IGBTBasics, #IGBTFunction