Exploring the 28BYJ-48 Stepper Motor: A Comprehensive Guide
Read More About
Introduction to 28BYJ-48
The 28BYJ-48 stepper motor is a widely used motor known for its precise control and versatility in various applications. In this comprehensive guide, we will delve into the details of the 28BYJ-48, its specifications, working principles, and potential uses. Whether you are an electronics enthusiast, a hobbyist, or a professional, this guide will provide valuable insights into this popular stepper motor.
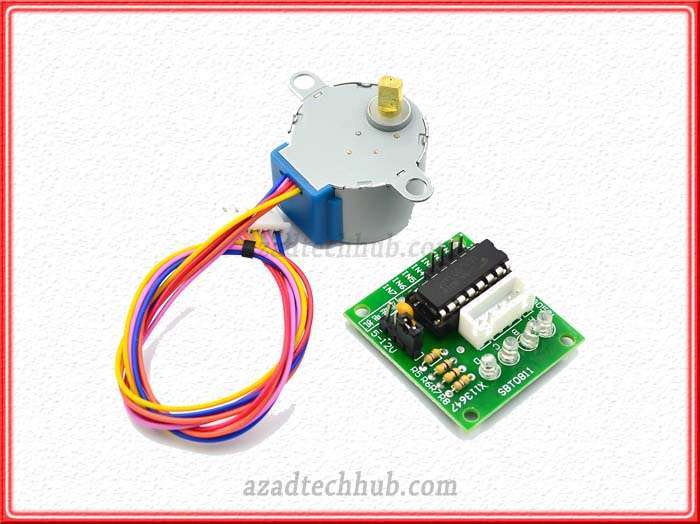
What is the 28BYJ-48 Stepper Motor?
The 28BYJ-48 stepper motor is a small, geared stepper motor widely used in various electronic and robotic applications. It is known for its low cost, compact size, and precise control capabilities. The “28BYJ-48” designation refers to its model number, which helps identify and differentiate it from other stepper motor models.
This stepper motor operates on the principle of electromagnetism and consists of multiple coils and gears. It is a unipolar stepper motor, meaning it has two windings per phase. The motor’s step angle is 5.625 degrees, and it requires 64 steps to complete a full revolution (360 degrees). However, by utilizing half-step or microstepping techniques, finer angular resolution can be achieved.
The 28BYJ-48 stepper motor is commonly used in robotics, automation, DIY projects, and prototyping. It finds applications in CNC machines, 3D printers, camera sliders, timelapse systems, and more. Its affordability and ease of use make it a popular choice for hobbyists and beginners in the field of electronics.
To control the 28BYJ-48 stepper motor, an appropriate motor driver is typically used, along with a microcontroller or a development board like Arduino. Programming languages and libraries such as C/C++, Python, and Arduino IDE can be utilized to interface with the motor and execute precise movements.
Overall, the 28BYJ-48 stepper motor offers a cost-effective and reliable solution for projects requiring accurate motion control in a compact form factor. Its versatility and widespread availability have made it a go-to choice for many electronics enthusiasts and professionals.
Specifications of the 28BYJ-48
Step Angle and Resolution:
- Step Angle: 5.625 degrees
- Steps per Revolution: 64 steps (360 degrees)
- Angular Resolution: By utilizing half-step or microstepping techniques, finer resolution can be achieved.
Operating Voltage and Current:
- Rated Voltage: 5V DC
- Rated Current: Typically around 100mA per phase
Gear Reduction Ratio:
- The 28BYJ-48 stepper motor is equipped with a built-in reduction gearbox that provides a gear reduction ratio of 1/64.
This means that the output shaft of the motor completes one full revolution for every 64 steps.
Holding Torque:
- The holding torque of the 28BYJ-48 stepper motor is relatively low compared to larger stepper motors.
It typically ranges between 34.3 to 39.2 mN·m (miliNewton-meter).
It’s important to note that these specifications may vary slightly between different manufacturers or specific versions of the 28BYJ-48 stepper motor. Therefore, it’s recommended to refer to the datasheet or documentation provided by the manufacturer for precise specifications related to a particular model or version of the motor.
Working Principle of the 28BYJ-48
Unipolar Stepper Motor: The 28BYJ-48 stepper motor is a type of unipolar stepper motor. It consists of two windings per phase, with each winding having a center tap. The center taps of the windings are usually connected to the positive power supply, while the remaining ends are connected to the motor driver.
Electromagnetic Coils and Phases: The motor has four electromagnetic coils, labeled A, B, C, and D. These coils are energized in a specific sequence to create a magnetic field that drives the motor’s rotor.
The coils are divided into two phases: Phase 1 consists of coils A and C, while Phase 2 consists of coils B and D. By energizing the coils in the appropriate sequence, the motor can rotate in a controlled manner.
Full-Step and Half-Step Modes: The 28BYJ-48 stepper motor can operate in two main stepping modes: full-step and half-step modes.
Full-Step Mode: In this mode, the coils of each phase are alternately energized. The stepping sequence for full-step mode is typically:
- Phase 1 (A and C) energized.
- Phase 2 (B and D) energized.
- Phase 1 (A and C) reversed polarity.
- Phase 2 (B and D) reversed polarity.
This sequence completes one full step, which corresponds to the motor’s step angle (5.625 degrees). The motor rotates with a higher torque in this mode, but the angular resolution is lower compared to the half-step mode.
Half-Step Mode: In this mode, the coils are energized in a specific sequence that allows for smaller angular movements between steps, effectively doubling the motor’s resolution. The stepping sequence for half-step mode is typically:
- Phase 1 (A and C) energized.
- Phase 1 (A and C) and Phase 2 (B and D) energized simultaneously.
- Phase 2 (B and D) energized.
- Phase 1 (A and C) reversed polarity.
- Phase 1 (A and C) and Phase 2 (B and D) energized simultaneously (opposite polarity).
- Phase 2 (B and D) reversed polarity.
This sequence allows for smaller angular increments and smoother motion, but the torque output is slightly reduced compared to the full-step mode.
By controlling the sequence and timing of the coil energization, the 28BYJ-48 stepper motor can achieve precise angular control and rotational movement in both full-step and half-step modes.
Wiring and Connection for the 28BYJ-48 Stepper Motor:
Pin Configuration: The 28BYJ-48 stepper motor typically has five or six wires, depending on the version or model. The wires are color-coded and have specific functions. The standard wire colors and their corresponding functions are as follows:
- Orange: Phase 1 (A)
- Pink: Phase 2 (B)
- Yellow: Phase 1 (C)
- Blue: Phase 2 (D)
- Red: Center Tap (common positive connection)
(Some versions may not have a center tap wire)
To identify the specific pinout of your motor, you can refer to the datasheet or documentation provided by the manufacturer.
Power Supply Requirements:
The 28BYJ-48 stepper motor operates at a rated voltage of 5V DC. It is important to use a power supply that matches this voltage to ensure proper motor performance.
The motor typically requires a current of around 100mA per phase. Ensure that your power supply can provide enough current to meet the motor’s requirements.
Motor Driver Selection:
To control the 28BYJ-48 stepper motor, you will need a motor driver capable of providing the necessary current and controlling the stepping sequence.
A commonly used motor driver for this stepper motor is the ULN2003 driver, which is designed specifically for unipolar stepper motors. It provides the required current amplification and can handle the motor’s voltage and current specifications.
Other motor drivers capable of driving unipolar stepper motors can also be used, such as the A4988 or DRV8825.
When selecting a motor driver, consider factors such as voltage compatibility, current handling capability, and control interface (e.g., GPIO pins, SPI, I2C) based on your specific application and microcontroller/Arduino board.
Ensure to follow the manufacturer’s instructions and datasheets when wiring and connecting the 28BYJ-48 stepper motor. Properly connect the motor wires to the motor driver, and then connect the motor driver to the microcontroller or Arduino board using the appropriate interface and control signals.
It’s crucial to note that incorrect wiring or power supply selection may damage the motor or motor driver. Therefore, double-check the pinout, voltage, and current requirements before making the connections.
Controlling the 28BYJ-48 Stepper Motor
Arduino and Microcontroller Integration: The 28BYJ-48 stepper motor can be easily integrated with microcontrollers like Arduino for control and programming. Arduino boards provide a convenient platform for interfacing with the motor and executing precise movements.
To integrate the motor with Arduino, follow these general steps:
- Connect the motor driver (such as the ULN2003) to the Arduino board according to the motor driver’s pinout and the Arduino’s GPIO pins.
- Connect the 28BYJ-48 motor wires to the motor driver outputs, ensuring proper alignment of the phases.
- Upload the appropriate code to the Arduino that controls the motor driver and specifies the desired motor movement.
- Programming Languages and Libraries: Various programming languages can be used to control the 28BYJ-48 stepper motor, depending on the microcontroller or development board being used. Some common programming languages include:
- Arduino IDE: Arduino boards are often programmed using the Arduino IDE, which is based on C/C++ language.
- Python: Python can be used with libraries like RPi.GPIO or pySerial for controlling the motor through microcontrollers like Raspberry Pi or Arduino with Python support.
- Other languages: Depending on the microcontroller or development board, other languages such as C/C++, Java, or JavaScript may be applicable. It’s important to check the specific programming language support for the chosen platform.
- Additionally, there are libraries available that simplify the motor control process by providing pre-built functions and abstractions. For example:
- Arduino Stepper Library: The official Arduino Stepper library provides a set of functions to control stepper motors, including the 28BYJ-48. It allows you to define motor parameters and execute movements with ease.
- RPi.GPIO: This Python library provides functions to control GPIO pins on a Raspberry Pi, enabling the control of the stepper motor through the GPIO interface.
- Stepper Motor Control Techniques: The 28BYJ-48 stepper motor can be controlled using different techniques to achieve various motion patterns. Some common control techniques include:
- Full-Step Control: In this technique, the motor is driven in full-step mode, where each step corresponds to the motor’s step angle (5.625 degrees). This technique provides higher torque output but lower resolution.
- Half-Step Control: By utilizing the half-step mode, the motor can be driven with smaller angular increments, effectively doubling the resolution. This technique results in smoother motion but slightly reduced torque.
- Microstepping: Microstepping techniques use intermediate current levels to achieve even smaller angular increments between steps, providing smoother motion and higher resolution. Microstepping requires motor drivers capable of microstepping control, such as the A4988 or DRV8825.
The choice of control technique depends on the desired application and the specific requirements of the project. It is important to consider factors such as torque, resolution, and speed when selecting the appropriate control technique.
By integrating the 28BYJ-48 stepper motor with a microcontroller, utilizing the suitable programming language and libraries, and applying the desired control techniques, you can achieve precise control and execute various motion patterns with the motor in your projects.
Applications of the 28BYJ-48 Stepper Motor
Robotics and Automation: The 28BYJ-48 stepper motor finds applications in robotics and automation systems. It can be used to control robotic arms, grippers, or other mechanisms that require precise and controlled movement. The motor’s compact size and precise control make it suitable for various robotic applications.
CNC Machines and 3D Printers: The 28BYJ-48 stepper motor can be utilized in CNC (Computer Numerical Control) machines and 3D printers. It can drive the movement of the printer’s extruder or control the positioning of the CNC machine’s cutting tool. With its ability to provide accurate and repeatable motion, the motor contributes to the precise fabrication and additive manufacturing processes.
Camera Sliders and Timelapse Systems: The motor’s ability to provide controlled movement is valuable in camera sliders and timelapse systems. It can be used to drive the linear movement of the camera slider, allowing for smooth and precise tracking shots in cinematography or time-lapse photography. The stepper motor’s accuracy helps achieve consistent and repeatable camera movements.
DIY Projects and Prototyping: The 28BYJ-48 stepper motor is popular in various do-it-yourself (DIY) projects and prototyping endeavors. Its affordability, ease of use, and availability make it a go-to choice for hobbyists and beginners. It can be used in DIY robotic projects, automated systems, motion control experiments, or other creative applications.
The 28BYJ-48 stepper motor’s versatility, compact size, and precise control capabilities contribute to its widespread use in various fields. Its applications extend beyond the examples mentioned above, as it can be adapted to meet specific project requirements in numerous domains, including home automation, art installations, scientific experiments, and more.
Tips for Optimizing 28BYJ-48 Performance
Microstepping: Implementing microstepping techniques can significantly improve the performance of the 28BYJ-48 stepper motor. Microstepping allows for finer angular resolution and smoother motion by driving the motor with intermediate current levels between steps. By utilizing a motor driver capable of microstepping control, such as the A4988 or DRV8825, you can achieve improved precision and reduced vibration or resonance effects.
Power Management: Proper power management is crucial for optimizing motor performance and preventing damage. Consider the following aspects:
- Ensure that the power supply voltage matches the motor’s rated voltage (5V DC).
- Provide a stable and adequate power supply to the motor, considering its current requirements (typically around 100mA per phase).
- Avoid exceeding the motor’s maximum current limits to prevent overheating and potential damage.
- Implement appropriate current limiting mechanisms, such as current-limiting resistors or adjustable motor drivers, to regulate the current flowing through the motor coils.
- Mechanical Considerations: To enhance the performance and longevity of the 28BYJ-48 stepper motor, consider the following mechanical considerations:
- Ensure proper alignment and tension of belts or mechanisms connected to the motor to minimize backlash and improve accuracy.
- Reduce friction and mechanical resistance in the motor’s mechanical system by using suitable bearings, lubrication, and proper alignment of mechanical components.
- Avoid overloading the motor beyond its holding torque capacity to prevent stalling or damage.
- Additionally, if the motor exhibits excessive noise or vibration during operation, implementing mechanical damping techniques, such as shock absorbers or vibration dampers, can help reduce unwanted vibrations and improve overall performance.
By implementing microstepping techniques, managing power supply effectively, and considering mechanical factors, you can optimize the performance of the 28BYJ-48 stepper motor. Remember to refer to the motor’s datasheet and consider the specific requirements of your application for the best results.
Troubleshooting Common Issues
Motor Stalling: If the motor stalls or fails to move, consider the following troubleshooting steps:
- Check the power supply voltage: Ensure that the motor is receiving the correct voltage (5V DC) and that the power supply can deliver sufficient current.
- Verify the motor driver connections: Double-check the wiring connections between the motor and the motor driver. Ensure that the phases are correctly connected and aligned.
- Adjust the current limit: If the current limit is set too low, the motor may not have enough power to overcome the load. Adjust the current limit to an appropriate level based on the motor’s specifications.
- Reduce the load: If the motor is being overloaded, try reducing the load or friction on the motor shaft to prevent stalling.
- Verify the control signals: Check that the control signals to the motor driver are being sent correctly. Ensure that the correct stepping sequence is being executed.
Overheating: If the motor is getting excessively hot during operation, consider the following steps:
- Check the current limit: Make sure that the current limit is set within the safe operating range specified for the motor. If it is set too high, it can cause excessive heat generation.
- Verify power supply voltage: Ensure that the power supply voltage is not exceeding the motor’s specified voltage. Higher voltages can cause increased heat dissipation.
- Improve ventilation: Provide adequate ventilation and airflow around the motor to dissipate heat. Avoid enclosing the motor in a confined space that restricts airflow.
- Reduce duty cycle: If the motor is being operated continuously at high torque, consider reducing the duty cycle by introducing rest periods between movements. This allows the motor to cool down periodically.
- Wiring Problems: If you are experiencing issues with the motor’s operation, consider the following troubleshooting steps related to wiring:
- Verify wire connections: Check that the motor wires are properly connected to the motor driver and microcontroller or Arduino board. Ensure that there are no loose or disconnected wires.
- Check for damaged wires: Inspect the motor wires for any signs of damage, such as fraying, cuts, or breaks. Replace any damaged wires.
- Ensure correct phase connections: Verify that the motor phases (A, B, C, D) are connected in the correct sequence and aligned properly with the motor driver’s outputs.
- Verify the ground connection: Ensure that there is a common ground connection between the motor driver, power supply, and microcontroller or Arduino board.
By troubleshooting and addressing these common issues related to motor stalling, overheating, and wiring problems, you can improve the performance and functionality of the 28BYJ-48 stepper motor. If the issues persist, consult the motor’s datasheet or seek further assistance from the manufacturer or relevant community forums for additional troubleshooting guidance.
Comparison with Other Stepper Motors:
NEMA 17 Stepper Motor:
Size and Torque: NEMA 17 stepper motors are larger and more powerful compared to the 28BYJ-48. They typically have a higher torque output, allowing them to handle heavier loads.
Step Angle and Resolution: NEMA 17 motors usually have a step angle of 1.8 degrees, providing a higher angular resolution compared to the 28BYJ-48’s 5.625 degrees. This results in finer control and smoother motion.
Power and Voltage: NEMA 17 motors often require a higher voltage and current to operate effectively. They are commonly used with power supplies ranging from 12V to 48V, depending on the specific motor model.
Applications: NEMA 17 motors are frequently used in robotics, CNC machines, 3D printers, and other applications where higher torque and precision are required.
NEMA 23 Stepper Motor
Size and Torque: NEMA 23 stepper motors are larger and more powerful than both NEMA 17 and the 28BYJ-48. They are capable of delivering even higher torque, making them suitable for demanding applications.
Step Angle and Resolution: Similar to NEMA 17 motors, NEMA 23 motors typically have a step angle of 1.8 degrees, providing fine resolution and accurate positioning.
Power and Voltage: NEMA 23 motors generally require higher voltages and currents for operation. They are commonly used with power supplies ranging from 24V to 48V.
Applications: NEMA 23 motors are commonly used in CNC machines, industrial automation, robotics, and applications where higher torque and precision are essential.
Other Small Stepper Motors
There are various small stepper motors available in the market, each with its own specifications and characteristics. Some common examples include:
17HS series: These motors are similar to NEMA 17 motors and offer a balance between size, torque, and cost. They are widely used in 3D printers, CNC machines, and automation projects.
42BYG series: These motors are compact and offer decent torque for their size. They are commonly used in small automation systems, camera sliders, and robotics projects.
20BYJ series: These motors are similar to the 28BYJ-48 but with slight variations in size, torque, and electrical characteristics. They are often used in small robotics, home automation, and prototyping projects.
When selecting a stepper motor for a specific application, consider factors such as torque requirements, resolution, power supply compatibility, physical size constraints, and cost. Each motor type has its strengths and is suitable for different applications based on their specific requirements.
Where to Buy the 28BYJ-48 Stepper Motor
The 28BYJ-48 stepper motor is widely available for purchase from various online and offline sources. Here are some options for purchasing the motor:
Online Marketplaces:
Amazon: Amazon offers a wide selection of 28BYJ-48 stepper motors from various sellers. You can find both individual motors and motor kits that include motor drivers and other accessories.
eBay: eBay is another popular online marketplace where you can find new and used 28BYJ-48 motors at competitive prices. It allows you to buy from individual sellers or specialized stores.
AliExpress: AliExpress is an online marketplace that offers a range of products, including the 28BYJ-48 stepper motor. You can find different variants of the motor and compare prices from different sellers.
Electronics Suppliers of 28BYJ-48
Adafruit: Adafruit is an online electronics store that specializes in DIY electronics components and kits. They offer the 28BYJ-48 motor and related accessories.
SparkFun: SparkFun is another popular electronics supplier that carries a variety of components and development boards. They often have the 28BYJ-48 stepper motor in stock.
Local Electronics Stores: Check local electronics stores, hobby shops, or robotics suppliers in your area. They may carry stepper motors, including the 28BYJ-48, or be able to order them for you.
Conclusion
The 28BYJ-48 stepper motor is readily available for purchase from online marketplaces like Amazon, eBay, and AliExpress. Additionally, electronics suppliers like Adafruit and SparkFun may offer the motor along with other components and kits. Be sure to compare prices, read customer reviews, and check the seller’s reputation before making a purchase.
Subscribe to our Newsletter “Electrical Insights Daily” to get the latest updates in Electrical Engineering. You can also Follow us LinkedIn to see our latest posts.