Star Delta Starter: A Comprehensive Guide
Read More About
Introduction to Star Delta Starter
A star delta starter, also known as a Wye-Delta starter, is an electrical control circuit used to start and control the speed of three-phase induction motors. It is widely employed in various industries where motors with high power ratings are used, such as manufacturing plants, refineries, and mining operations.
The primary purpose of a star delta starter is to reduce the starting current drawn by the motor during the initial phase, thereby minimizing the stress on the electrical system. By connecting the motor in a star (Y) configuration during the starting period and then switching it to a delta (∆) configuration for normal operation, the starter provides a smooth and controlled start for the motor.
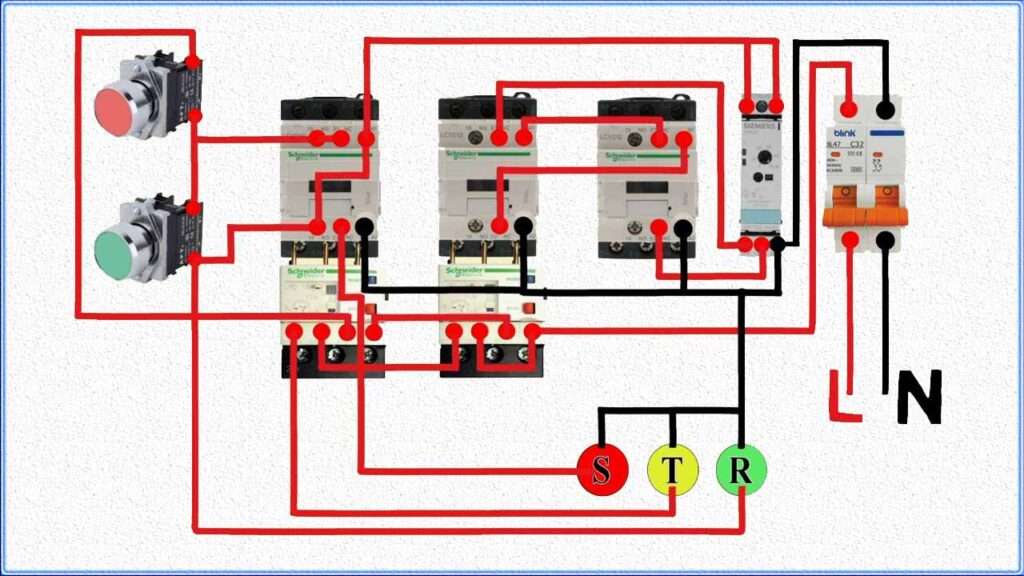
Here’s a step-by-step explanation of how a star delta starter works:
Initial State (Star Connection):
The motor windings are connected in a star configuration (Y) using three contactors. Each winding is connected to a phase of the power supply through its respective contactor. The motor receives a reduced voltage during the starting phase, typically around 30-50% of the full voltage.
Starting Phase:
When the start button is pressed, the contactors connected to the star points are energized, closing the circuit. The motor starts to run with reduced voltage and current, which minimizes the inrush current and torque. The motor accelerates gradually, allowing it to reach a predetermined speed.
Transition Phase:
After a specified time delay (usually a few seconds), the contactors connected to the star points open. The motor windings are disconnected from the star points. This transition phase two types including open transition and closed transition.
open transition
Open transition refers to a method of transitioning between two power sources or configurations without interrupting the power supply. In the context of motor control, open transition typically refers to the switching between the star and delta configurations in a star delta starter.
During an open transition in a star delta starter, the switching between the star and delta connections occurs with a momentary interruption in the power supply to the motor. The motor is temporarily disconnected from the power supply while transitioning from the star configuration to the delta configuration.
Here’s a step-by-step explanation of the open transition process in a star delta starter:
Starting Phase (Star Connection):
The motor windings are initially connected in a star (Y) configuration. The contactors responsible for the star connection (KM2) are energized, closing the circuit. The motor starts to run with reduced voltage and current in the star configuration.
Transition Phase:
After a specified time delay (typically a few seconds) set by the timer in the control circuit, the transition from star to delta connection begins. During this transition, the contactors responsible for the star connection (KM2) open, disconnecting the motor windings from the star configuration. There is a momentary interruption in the power supply to the motor as the switching takes place.
Operational Phase (Delta Connection):
Once the contactors responsible for the star connection (KM2) have opened, the contactors for the delta connection (KM3) are energized, closing the circuit. The motor windings are now connected in a delta (∆) configuration. The power supply is restored, and the motor continues to run in the delta configuration.
During the transition phase, the momentary interruption in power can cause a brief loss of torque or deceleration in the motor. This interruption is typically very short and does not significantly affect the motor’s overall performance.
It’s important to note that open transition is just one method of transitioning between the star and delta connections. There is another method called closed transition, where the switching occurs without any interruption in power supply. Closed transition methods involve additional equipment and control circuitry to ensure a seamless transition between the configurations.
The selection of open or closed transition depends on the specific motor and application requirements. It is recommended to refer to the manufacturer’s documentation or consult an expert for guidance on the appropriate transition method for a given motor control system.
closed transition
Closed transition refers to a method of transitioning between two power sources or configurations without interrupting the power supply. In the context of motor control, closed transition typically refers to the switching between the star and delta configurations in a star delta starter.
During a closed transition in a star delta starter, the switching between the star and delta connections occurs without any noticeable interruption in the power supply to the motor. The motor remains connected to the power supply at all times during the transition, ensuring a smooth and continuous operation.
Here’s a step-by-step explanation of the closed transition process in a star delta starter:
Starting Phase (Star Connection):
The motor windings are initially connected in a star (Y) configuration. The contactors responsible for the star connection (KM2) are energized, closing the circuit. The motor starts to run with reduced voltage and current in the star configuration.
Transition Phase:
During the transition from star to delta connection, a parallel path is established between the star and delta configurations. Before opening the contactors for the star connection (KM2), the contactors for the delta connection (KM3) are closed. This ensures that the motor remains connected to the power supply during the transition, maintaining a continuous power supply.
Operational Phase (Delta Connection):
Once the contactors for the delta connection (KM3) are closed, the contactors for the star connection (KM2) are opened. The motor windings are now connected in a delta (∆) configuration. The motor continues to run without any noticeable interruption in the power supply.
By maintaining a continuous power supply during the transition, closed transition methods ensure a seamless switching between the star and delta configurations. This eliminates the brief interruption in power that occurs in open transition methods, preventing any loss of torque or deceleration in the motor.
It’s important to note that closed transition methods require additional equipment and control circuitry to establish the parallel path between the configurations. This includes interlocking mechanisms, additional contactors, and precise timing coordination to ensure a smooth transition.
Operational State (Delta Connection):
The motor windings are reconfigured into a delta (∆) configuration using the contactors. The motor now receives the full supply voltage and is capable of running at its rated speed. The current drawn by the motor increases due to the higher voltage applied across the windings.
The transition from star to delta configuration allows the motor to operate at full load and provides a smoother transition from the starting phase to the operational phase. The star delta starter ensures that the motor is protected from excessive current during startup while maintaining its performance during normal operation.
It’s worth noting that the control of a star delta starter is typically handled by a motor control panel, which includes timers, relays, and other necessary components to automate the switching between star and delta connections. This automation eliminates the need for manual intervention during the startup process.
The star delta starter is an efficient and reliable method for starting and controlling induction motors, particularly for motors with high power ratings. It helps prolong the motor’s lifespan, reduces electrical stress, and provides a smooth and controlled acceleration, making it a preferred choice in many industrial applications.
star delta starter features
The star delta starter, also known as the star delta or wye-delta starter, offers several features that make it a popular choice for starting and controlling three-phase induction motors. Here are some key features of a star delta starter:
Reduced Starting Current:
One of the main features of a star delta starter is its ability to significantly reduce the starting current during motor startup. By starting the motor in the star configuration, the current is reduced to approximately one-third of the delta connection. This helps prevent voltage drops, reduces stress on the electrical system, and avoids overloads.
Reduced Starting Torque:
The star delta starter also reduces the starting torque during motor startup. The star connection limits the torque, which is advantageous when starting motors connected to high-inertia loads or when a gentle start is required. This helps prevent excessive mechanical stress and protects the motor and driven equipment.
Sequential Switching:
The star delta starter employs a sequential switching mechanism to transition the motor from the star configuration to the higher-voltage delta configuration. This switching is typically controlled by a timer or a control circuit, ensuring a smooth and controlled transition without sudden jolts or disturbances.
Cost-effective Solution:
The star delta starter is relatively simple in design, requiring fewer components compared to other starting methods such as soft starters or variable frequency drives (VFDs). This simplicity translates into cost savings in terms of equipment costs, installation, and maintenance.
Suitable for Low to Medium Starting Torque Applications:
The star delta starter is well-suited for applications with low to medium starting torque requirements. It is commonly used in industries such as pumps, fans, compressors, and conveyor systems. However, for applications with high starting torque demands, alternative starting methods may be more appropriate.
Compliance with Standards:
The star delta starter design and implementation adhere to established industry standards and guidelines. This ensures compatibility, safety, and reliability in motor control applications.
Easy Installation and Maintenance:
The star delta starter is relatively straightforward to install and maintain, as it does not involve complex control circuitry or additional equipment. This simplifies troubleshooting and reduces downtime in case of any issues.
Energy Efficiency:
By reducing the starting current and torque, the star delta starter helps improve energy efficiency during motor startup. This can lead to cost savings in terms of energy consumption and contribute to overall energy conservation efforts.
It’s important to consider the specific requirements of the motor and application when deciding whether to use a star delta starter. Factors such as load characteristics, starting torque demands, speed control needs, and the overall electrical system should be evaluated to determine the most appropriate starting method.
equations of star delta starter
A star delta starter is used to start and control three-phase induction motors. It allows the motor to start in a low-voltage, low-current “star” configuration and then switch to a higher-voltage, higher-current “delta” configuration once the motor has reached a certain speed. This transition helps in reducing the starting current and torque, minimizing mechanical stress on the motor, and improving overall system efficiency. Let’s derive the equations that explain the working principle of a star delta starter.
In a star delta starter, the motor windings are initially connected in a star (Y) configuration during the starting phase. The voltage and current in the star connection are reduced compared to the delta connection, which helps limit the starting current and torque. The equations for the star connection are as follows:
Phase Voltage (V_ph) = Line Voltage (V_L) Phase Current (I_ph) = Line Current (I_L) / √3
The power equation in the star connection is given by:
Power (P) = √3 * V_L * I_L * Power Factor (cos(θ))
Once the motor has reached a certain speed, the transition phase begins, and the motor windings are switched from the star configuration to the delta (∆) configuration. In the delta connection, the voltage and current increase, providing higher torque and power. The equations for the delta connection are as follows:
Line Voltage (V_L) = √3 * Phase Voltage (V_ph) Line Current (I_L) = Phase Current (I_ph)
The power equation in the delta connection is given by:
Power (P) = √3 * V_L * I_L * Power Factor (cos(θ))
During the transition phase, the motor windings are briefly disconnected from the power supply to switch the connection from star to delta. This interruption in power causes a momentary drop in torque and acceleration. However, the reduction in starting current helps protect the motor and reduces electrical stresses on the system.
The transition from the star to delta configuration is typically controlled by a timer. The time delay allows the motor to reach a sufficient speed before switching to the higher-voltage delta connection. The specific time delay can be adjusted based on the motor characteristics and application requirements.
It’s important to note that the above equations provide a simplified explanation of the working principle of a star delta starter. In practical applications, other factors such as motor characteristics, load conditions, and system requirements need to be considered for proper sizing, design, and implementation of a star delta starter. Consulting relevant standards, guidelines, and professional expertise is recommended for accurate calculations and proper utilization of a star delta starter.
power circuit of star delta starter
The power circuit of a star delta starter involves the connections between the power supply lines, the motor windings, and the contactors.
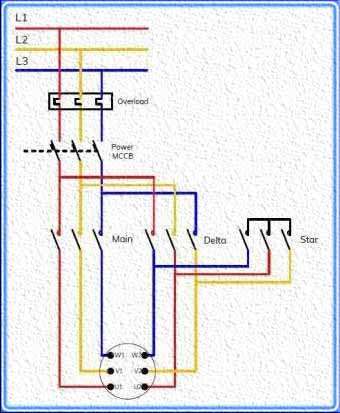
Here’s a description of the power circuit connections in a star delta starter:
Power Supply Connections:
Connect the three-phase power supply lines (L1, L2, and L3) to the main power terminals of the starter. Typically, the power supply lines are connected directly to the Main Contactor (KM1).
Motor Connections:
Connect the motor windings to the starter using three contactors: Main Contactor (KM1), Star Contactor (KM2), and Delta Contactor (KM3). The motor windings are labeled U, V, and W.
U1, V1, and W1:
Connect one end of each motor winding (U1, V1, and W1) to the corresponding contact on the Main Contactor (KM1). These connections establish the primary circuit between the power supply and the motor windings.
U2, V2, and W2:
Connect the other end of each motor winding (U2, V2, and W2) to the corresponding contact on the Star Contactor (KM2). These connections create the star (Y) configuration of the motor windings during the starting phase.
U3, V3, and W3:
Connect the other end of each motor winding (U3, V3, and W3) to the corresponding contact on the Delta Contactor (KM3). These connections form the delta (∆) configuration of the motor windings during the operational phase.
Control Circuit Power Supply:
Connect a control circuit power supply, typically a separate low voltage supply (e.g., 24V), to the control circuit of the starter. The control circuit power supply provides power to the control components, such as relays, timers, and push buttons.
The power circuit connections ensure that the motor windings are properly connected to the power supply and the contactors, allowing for the controlled switching between the star and delta configurations during the motor’s starting and operational phases.
It’s essential to follow electrical standards, safety regulations, and consult a qualified electrician or engineer for accurate power circuit connections and installation procedures specific to your motor and starter configuration.
control circuit of star delta starter
The control circuit of a star delta starter is responsible for controlling the switching between the star and delta configurations of the motor windings. It typically includes various components such as push buttons, timers, relays, and contactors.
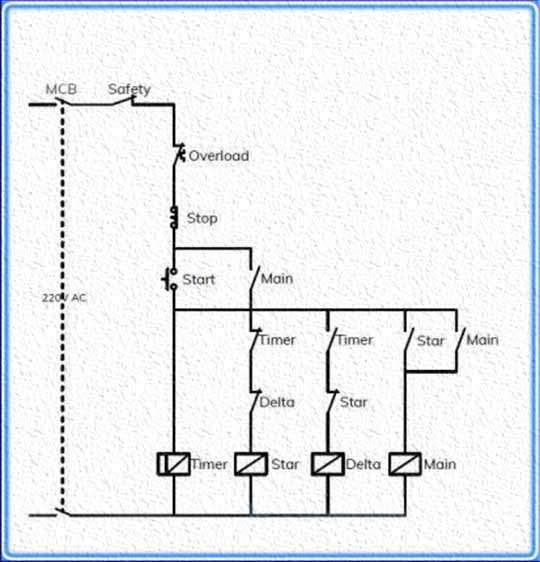
Here’s a description of the control circuit components and their connections in a star delta starter:
Start Button (normally open):
Connect one terminal of the start button to the control circuit’s positive voltage (+) terminal. Connect the other terminal of the start button to the control circuit’s Start (ST) input.
Stop Button (normally closed):
Connect one terminal of the stop button to the control circuit’s positive voltage (+) terminal. Connect the other terminal of the stop button to the control circuit’s Stop (SP) input.
Overload Relay:
Connect the normally open contacts of the overload relay in series with the control circuit’s positive voltage (+) terminal. The overload relay protects the motor from excessive current by sensing the current drawn by the motor.
Timer:
Connect the timer to control the switching between the star and delta connections. Connect one terminal of the timer to the control circuit’s positive voltage (+) terminal. Connect the output terminal of the timer to the coil of the Star Contactor (KM2).
The timer determines the duration of the star connection and automatically switches to the delta connection after a preset time delay. The timer should have a normally closed contact connected in parallel with the timer coil to maintain the circuit’s continuity during the transition phase.
Control Circuit Power Supply:
Connect a control circuit power supply, typically a separate low voltage supply (e.g., 24V), to the control circuit. Connect the positive voltage (+) terminal of the power supply to the start button, stop button, overload relay, timer, and other control circuit components. Connect the negative voltage (-) terminal of the power supply to the control circuit’s common ground.
Contactor Control:
Connect the control coil of each contactor (Main Contactor KM1, Star Contactor KM2, and Delta Contactor KM3) to the control circuit. The control circuit energizes and de-energizes the contactor coils to open or close the contactors based on the control inputs (start, stop, timer, etc.).
The control circuit components work together to provide control and automation in the star delta starter, allowing for a smooth and controlled start of the motor.
Note: The specific wiring and connections of the control circuit may vary depending on the design and manufacturer of the star delta starter. It’s essential to refer to the manufacturer’s documentation or consult a qualified electrician for accurate control circuit connections specific to your star delta starter configuration.
size of over load relay
The size or rating of an overload relay for a motor depends on several factors, including the motor’s power rating, full-load current, and the desired level of overload protection. Here’s a general guideline for selecting the size of an overload relay:
Determine the Full-Load Current (FLC) of the motor:
The full-load current is the maximum current drawn by the motor when operating at its rated power. The full-load current rating is typically specified by the motor manufacturer and can be found on the motor nameplate or in the motor’s technical documentation.
Select the Overload Relay Current Range:
The overload relay should have a current range that accommodates the full-load current of the motor. The selected overload relay should have a current range that matches or slightly exceeds the full-load current of the motor.
For example, if the motor has a full-load current of 10 Amperes, you might select an overload relay with a current range of 6-12 Amperes or 10-16 Amperes.
Consider the Desired Level of Overload Protection:
Overload relays are available in different classes or trip curves, which determine the response time and sensitivity to over currents. Consider the level of overload protection required for the motor and the application.
Common overload relay classes include Class 10, Class 20, and Class 30, which represent different levels of trip curves.
Verify Compatibility and Standards:
Ensure that the selected overload relay is compatible with the motor’s control circuit and is suitable for the intended application. Follow applicable standards, regulations, and codes for motor protection and sizing of overload relays in your region.
It’s crucial to consult the motor manufacturer’s documentation, electrical codes, and standards specific to your region for precise guidance on selecting the appropriate size of the overload relay for a motor. Additionally, seeking assistance from a qualified electrical engineer or professional is recommended to ensure proper selection and installation.
size of main contactors
The size or rating of main contactors for a motor is typically determined based on the motor’s power rating, voltage, and the intended application. The main contactor is responsible for connecting and disconnecting the motor from the power supply. Here are some general guidelines for selecting the size of main contactors:
Motor Power Rating:
Determine the motor’s power rating, usually expressed in kilowatts (kW) or horsepower (HP). The power rating can typically be found on the motor nameplate or in the motor’s technical documentation.
Voltage Rating:
Check the motor’s voltage rating to ensure that the main contactor is rated for the same voltage. Common voltage ratings for main contactors include 240V, 480V, or 690V, depending on the motor and application.
Full-Load Current (FLC):
Calculate or determine the motor’s full-load current (FLC), which represents the maximum current drawn by the motor at rated power. The full-load current is typically specified by the motor manufacturer and can be found on the motor nameplate or in the motor’s technical documentation.
Derating Factors:
Consider any derating factors that may apply to the main contactor selection. These factors account for variables such as ambient temperature, duty cycle, and motor starting conditions. Derating factors help ensure that the main contactor can handle the actual current and load conditions it will encounter in the application.
Selecting the Contactor:
Choose a main contactor with a current rating that matches or exceeds the motor’s full-load current (including any applicable derating factors). It is common to select a main contactor with a current rating slightly higher than the motor’s full-load current to allow for some margin.
It’s important to consult the motor manufacturer’s documentation, electrical codes, and standards specific to your region for precise guidance on selecting the appropriate size of main contactors for a motor. Additionally, seeking assistance from a qualified electrical engineer or professional is recommended to ensure proper selection and installation.
star delta starter advantages and dis-advantages
Advantages of Star Delta Starter:
Reduced Starting Current:
One of the key advantages of a star delta starter is that it significantly reduces the starting current during motor startup. By starting the motor in the star configuration, the current is reduced to approximately one-third of the delta connection. This helps in minimizing voltage drops in the electrical system and prevents overload conditions.
Reduced Starting Torque:
The star delta starter also reduces the starting torque during motor startup. The star connection limits the torque, which is beneficial when starting large motors or when the driven load requires a gentle start. This helps in preventing excessive mechanical stress and reduces the likelihood of equipment damage.
Lower Power Demand:
Due to the reduced starting current and torque, the star delta starter reduces the power demand during motor startup. This is particularly advantageous in applications where multiple motors are started simultaneously, as it helps prevent voltage fluctuations and ensures stable operation of the electrical system.
Cost Savings:
The star delta starter is relatively simple in design and does not require complex control circuitry or additional equipment. This simplicity translates into cost savings, both in terms of equipment costs and installation/maintenance expenses.
Dis-advantages of Star Delta Starter
Momentary Power Interruption:
During the transition from the star to delta configuration, there is a momentary interruption in the power supply to the motor. This can result in a brief loss of torque and deceleration, which may not be desirable in certain applications that require continuous operation or where rapid acceleration is needed.
Limited Application Range:
The star delta starter is most effective for applications where the load torque and inertia are relatively low. In applications with high starting torque requirements, such as heavy-duty machinery or high-inertia loads, other starting methods like soft starters or variable frequency drives (VFDs) may be more suitable.
Increased Motor Stress:
While the star delta starter helps reduce starting current and torque, it still imposes some level of stress on the motor during the transition phase. This stress can affect the motor’s lifespan and efficiency, particularly if frequent starts and stops are required.
Limited Speed Control:
The star delta starter does not provide speed control capabilities. Once the motor transitions to the delta configuration, it operates at a fixed speed determined by the electrical frequency. If speed control or variable speed operation is necessary, alternative methods like VFDs should be considered.
It’s important to consider the specific requirements of the motor and application when deciding whether to use a star delta starter. Factors such as load characteristics, starting torque demands, speed control needs, and the overall electrical system should be evaluated to determine the most appropriate starting method.
Subscribe to our Newsletter “Electrical Insights Daily” to get the latest updates in Electrical Engineering. You can also Follow us LinkedIn to see our latest posts.
Frequently Asked Questions
What is a star delta starter?
A star delta starter is a type of motor starter used to control and start three-phase induction motors.
How does a star delta starter work?
A star delta starter initially connects the motor windings in a star configuration for a gentle start, and then switches to a delta configuration for full-speed operation.
What are the advantages of using a star delta starter?
Advantages of using a star delta starter include reduced starting current and torque, lower power demand during startup, and cost-effectiveness.
What are the applications of a star delta starter?
Star delta starters are commonly used in applications such as pumps, fans, compressors, and conveyor systems.
How do you select the appropriate star delta starter for a specific motor?
The selection of a star delta starter for a specific motor depends on factors such as motor power, voltage, and starting torque requirements.
What are the key components of a star delta starter?
Key components of a star delta starter include contactors, overload relays, timers, and a control circuit.
Can a star delta starter be used for motors with high starting torque requirements?
Star delta starters are not suitable for motors with high starting torque requirements, as they are designed for low to medium starting torque applications.
What are the limitations of a star delta starter?
Limitations of a star delta starter include momentary power interruption during transition, limited speed control, and increased motor stress during switching.
How do you wire a star delta starter?
Wiring a star delta starter involves connecting the motor windings, contactors, overload relays, and control circuit as per the specific wiring diagram.
Are there any safety considerations when using a star delta starter?
Safety considerations when using a star delta starter include proper grounding, insulation, and following electrical codes and regulations. Additionally, caution should be exercised during maintenance or troubleshooting to avoid electrical hazards.
- Electrical Wiring Standards and Insurance: Best Guide
- Smart Home Technologies and Their Influence on Electrical Insurance
- Electrical System Design and Insurance Premiums: Important Overview
- The Role of Surge Protection in Electrical Insurance Policies
- Latest Jobs to Apply
Recent Posts on Blog