Demand Factor For Motor Loads: Important Examples
Demand factor for motor loads refers to the ratio between the actual power consumed by a group of motors and the maximum potential power that could be consumed if all the motors were running simultaneously at full load. It is an essential parameter used in electrical engineering and design to determine the total electrical demand of a system accurately.
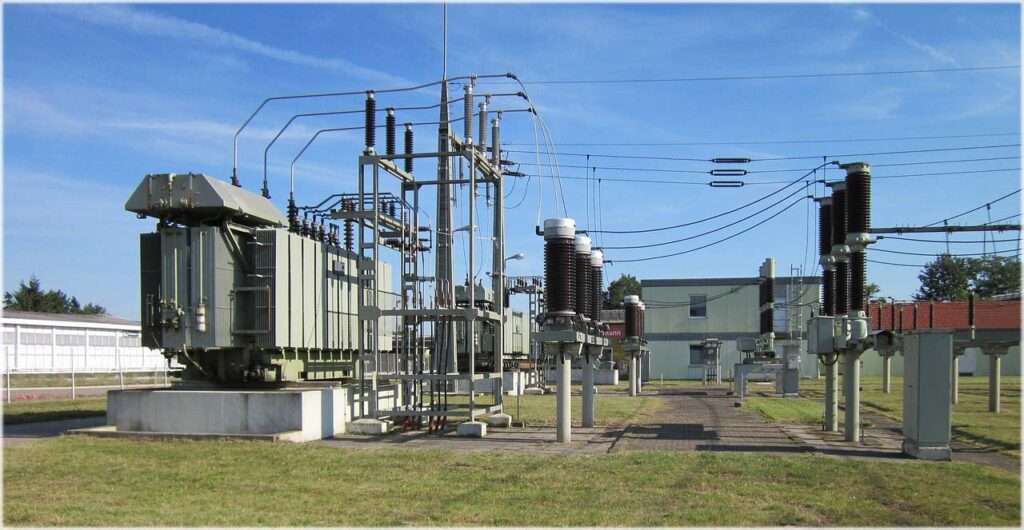
The demand factor for motor loads is crucial for sizing electrical equipment, such as generators, transformers, and switchgear, to ensure they can handle the load effectively.
Read More
Understanding the demand factor for motor loads is crucial to avoid overloading the electrical system and to optimize its efficiency. By considering the varying operational characteristics of motors, the demand factor takes into account the probability that all motors will not run at full capacity simultaneously. This factor accounts for the fact that motors often operate intermittently or at partial loads, resulting in lower overall power consumption compared to the sum of individual motor ratings.
Let’s consider an example to illustrate the concept of the demand factor for motor loads. Suppose a manufacturing plant has ten motors, each with a rating of 10 kW. If we assume a demand factor of 0.8 for these motors, it means that the maximum simultaneous demand for all the motors is calculated as follows:
Maximum demand = (Motor rating) x (Number of motors) x (Demand factor) = 10 kW x 10 x 0.8 = 80 kW
In this case, the plant’s electrical system needs to be designed to handle a maximum demand of 80 kW, even though the individual motor ratings sum up to 100 kW. By considering the demand factor, we avoid the unnecessary oversizing of electrical equipment, reducing costs and ensuring efficient operation.
The demand factor for motor loads can vary depending on the type of motors, their load characteristics, and the nature of the application. Motors used in residential buildings, commercial facilities, and industrial settings often have different demand factors due to varying usage patterns. For instance, in a residential building, the demand factor for motor loads may be lower because not all motors, such as those in air conditioning units, run simultaneously.
In electrical system design, the demand factor for motor loads is crucial for proper load balancing and ensuring the electrical infrastructure’s reliability. By accurately estimating the demand factor, engineers can size and select the appropriate electrical equipment, such as transformers, circuit breakers, and conductors, to meet the expected load demands without excessive oversizing or undersizing.
Furthermore, the demand factor for motor loads is vital in optimizing energy consumption. By understanding the probability of simultaneous full-load operation, energy management systems can be implemented to control motor usage, reducing peak demand and overall power consumption. This optimization leads to cost savings and improved energy efficiency.
The demand factor for motor loads is a fundamental parameter in electrical engineering and design. It determines the maximum potential power consumption of a group of motors based on their operational characteristics and load probabilities. By considering the demand factor, engineers can accurately size electrical equipment, balance loads, optimize energy consumption, and ensure the reliability and efficiency of electrical systems.
Examples of Demand Factor For Motor Loads
In a commercial office building, there are 20 motors installed, each with a rating of 5 kW. The demand factor for motor loads in this case is estimated to be 0.6. Therefore, the maximum simultaneous demand for all the motors would be: Maximum demand = 5 kW x 20 x 0.6 = 60 kW
A wastewater treatment plant utilizes various motors for pumps, mixers, and blowers. The motors have individual ratings ranging from 3 kW to 15 kW. After analyzing the load profiles and considering the operating schedules, an overall demand factor for motor loads of 0.75 is determined. This means that the total maximum demand can be calculated as: Maximum demand = (Sum of motor ratings) x (Demand factor)
In an industrial facility, there are multiple conveyor belts powered by electric motors. The motors have different power ratings, such as 2 kW, 5 kW, and 10 kW. By analyzing the operational data and studying the production processes, an average demand factor for motor loads of 0.9 is determined. This factor considers the intermittent operation of some motors during maintenance or production downtimes.
A hotel’s HVAC system comprises several air conditioning units, each equipped with a motor. The motors have different capacities, ranging from 3 kW to 10 kW. Based on historical data and occupancy patterns, the demand factor for motor loads is determined to be 0.7. This factor accounts for the likelihood that not all air conditioning units will be running at full load simultaneously, especially during periods of low occupancy or mild weather conditions.
In a data center, numerous server racks are cooled by fans powered by electric motors. The motors have ratings of 1 kW each. Through monitoring and analysis, it is determined that the demand factor for motor loads in the data center is 0.5. This factor considers the redundancy and load-sharing capabilities of the cooling system, which prevent all fans from operating at maximum capacity simultaneously.
Remember, the demand factor for motor loads can vary significantly depending on the specific application, industry, and load characteristics. Accurate determination of the demand factor is crucial for proper electrical system design, efficient energy management, and reliable operation of the motors.
Related Posts:
- What is Demand Factor and Diversity Factor?
- Transformers: Important Types, Features
- Transformer Oil Testing: 9 Important Tests
- 10 Transformer Tests Before Commissioning
Subscribe to our Newsletter “Electrical Insights Daily” to get the latest updates in Electrical Engineering. You can also Follow us LinkedIn and Facebook to see our latest posts on Electrical Engineering Topics.