Induction Motor Interview Questions: Best Overview
Navigating through induction motor interview questions is like embarking on an exploration of how machines work and how well we understand them. These questions aren’t just random queries; they’re more like a test that checks how deep we dive into the world of motors.
They cover a bunch of stuff, from figuring out how efficient a motor can be to practical things about how it actually works. In these interviews, we chat about things like insulation resistance, checking on bearings, losses inside the motor, and making sure the power going in is all good. It’s like a map showing how much we know about these electrical machines.
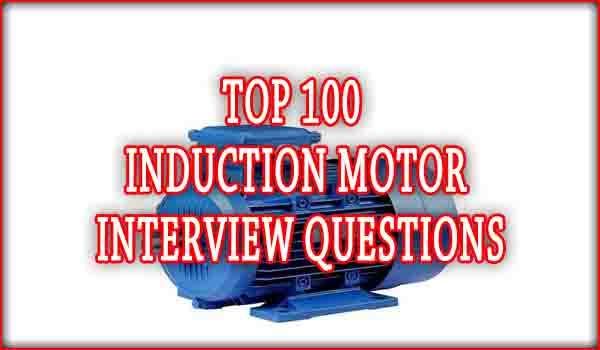
So, when we’re facing these induction motor interview questions, it’s like entering a zone full of technical puzzles and real-life connections. These questions dig into everything about how motors function, from dealing with different loads to how they handle being up high in the mountains.
Talking about these questions leads us into the details of stuff like how to change a motor’s speed, ways to deal with pesky harmonic issues, and even upgrading methods. Answering these induction motor interview questions isn’t just about showing what we know; it’s about proving we can take what we know and put it to work in the world of electrical machines.
Top 100 Induction Motor Interview Questions
1. What is an induction motor?
An induction motor is an AC motor widely used in various industries and applications. It operates on the principle of electromagnetic induction to produce rotational motion.
2. How does an induction motor work?
It functions by inducing a magnetic field in the rotor via electromagnetic induction from the stator’s rotating magnetic field, creating rotational motion.
3. What are the main components of an induction motor?
An induction motor consists of a stator (housing windings that produce a rotating magnetic field) and a rotor (usually made of conductive material), which interacts with the stator’s magnetic field to produce motion.
4. What are the types of induction motors?
Induction motors are typically categorized as single-phase and three-phase motors. Three-phase induction motors are more common due to their efficiency and robustness in industrial applications.
Understanding the operational principles is fundamental when answering induction motor interview questions.
5. What are the advantages of induction motors?
They are rugged, reliable, and require minimal maintenance due to the absence of brushes. They’re also cost-effective and suitable for a wide range of applications.
6. How does an induction motor start?
Induction motors typically start by using methods like direct-on-line (DOL) starting, star-delta starting, or using variable frequency drives (VFDs) to control the starting torque and speed.
7. Can you control the speed of an induction motor?
The speed of induction motors is generally fixed, but it can be controlled to some extent by varying the frequency of the power supply using VFDs.
8. What are the applications of induction motors?
Induction motors are extensively used in pumps, compressors, fans, conveyor systems, HVAC systems, and various industrial machinery due to their reliability and robustness.
9. What maintenance is required for induction motors?
Routine maintenance includes checking for bearing wear, ensuring proper lubrication, inspecting electrical connections, and monitoring for any signs of overheating.
10. How efficient are induction motors?
Induction motors are known for their high efficiency, especially when operating at or close to their rated load. Larger motors often have higher efficiencies.
11. What factors affect the efficiency of induction motors?
Efficiency is influenced by load, motor size, design, operating conditions, and power quality. Running the motor close to its rated load and maintaining optimal operating conditions enhances efficiency.
In induction motor interview questions, candidates often discuss the impact of insulation resistance on motor performance.
12. Can induction motors operate at variable speeds?
While their speed is inherently fixed by the frequency of the power supply, variable frequency drives (VFDs) can be employed to alter the motor’s speed by adjusting the frequency of the AC power.
13. What is slip in an induction motor?
Slip is the difference between the synchronous speed (theoretical speed) and the actual rotor speed. It’s necessary for the motor to generate torque, with higher slip resulting in higher torque.
14. How do you calculate the synchronous speed of an induction motor?
Synchronous speed is calculated using the formula:

where frequency is in Hz and the number of poles represents the motor’s pole pairs.
15. What are the effects of varying the number of poles in an induction motor?
Altering the number of poles changes the motor’s speed and torque characteristics. Increasing the number of poles decreases the speed and increases the torque, while reducing the number of poles has the opposite effect.
16. How do you detect motor faults in an induction motor?
Motor faults can be detected through methods like vibration analysis, thermal imaging, current and voltage analysis, and insulation resistance testing to identify issues like bearing wear, overheating, or winding faults.
17. Can induction motors be used in hazardous environments?
Specialized induction motors with features like explosion-proof enclosures, suitable insulation, and protective measures against flammable substances are available for hazardous environments.
18. What are the differences between squirrel cage and wound rotor induction motors?
Squirrel cage motors have rotor bars permanently short-circuited, providing ruggedness and simplicity. Wound rotor motors have external resistors allowing control of starting torque and speed.
19. How do you prevent overheating in induction motors?
Overheating can be prevented by ensuring proper ventilation, maintaining the recommended operating temperatures, and avoiding overload conditions that lead to excessive heat generation.
20. What are the advantages of using soft starters or VFDs with induction motors?
Soft starters and VFDs help in reducing the inrush current during motor start-up, minimizing mechanical stress, and allowing smooth acceleration, thus extending the motor’s lifespan.
21. What is the importance of the stator and rotor slot design in induction motors?
The stator and rotor slot design impacts motor performance by influencing factors like magnetic flux distribution, efficiency, torque, and overall motor operation.
22. Can induction motors be used for high-precision applications that demand constant speed?
Induction motors inherently have a fixed speed determined by the frequency of the power supply and might not be suitable for applications requiring highly precise speed control without additional control mechanisms.
23. How does the load affect the performance of an induction motor?
Changes in load affect the motor’s speed and efficiency. Operating the motor near its rated load optimizes performance, while operating at significantly lower or higher loads might affect efficiency and torque characteristics.
24. What are the typical starting methods for induction motors?
Common starting methods include Direct-On-Line (DOL) starting, star-delta starting, auto-transformer starting, and soft starters, each with its own impact on the motor’s starting torque and current.
One of the frequently asked induction motor interview questions pertains to the mitigation of harmonic effects in motor systems.
25. How do you mitigate the effects of harmonics in induction motors?
Harmonics can negatively impact motor efficiency and increase losses. Mitigation methods involve using harmonic filters, line reactors, or proper VFDs to minimize these effects.
Could you explain how adjustable speed drives impact the efficiency of induction motors, a common query in induction motor interview questions.
26. Can induction motors be used in regenerative braking systems?
While induction motors are typically not well-suited for regenerative braking due to their inherent inability to generate power back into the grid, specialized designs or combined systems can facilitate limited regenerative braking.
27. What measures can be taken to reduce noise in induction motors?
Noise reduction can be achieved through better design, improved insulation, using high-quality bearings, and employing vibration-damping materials to minimize mechanical vibrations.
28. How does insulation play a role in induction motor performance and longevity?
Insulation ensures proper electrical isolation, preventing faults and breakdowns that can compromise motor performance. Regular insulation testing is vital to maintain motor integrity.
29. Can induction motors be used for applications requiring frequent starting and stopping?
Yes, induction motors can handle frequent start-stop cycles, but frequent starts without adequate cooling intervals might impact the motor’s longevity and efficiency.
30. What are the advantages of high-efficiency induction motors?
High-efficiency induction motors reduce energy consumption, operating costs, and environmental impact, making them favorable for sustainable and energy-efficient applications.
31. What role do bearings play in induction motor performance?
Bearings support rotor shafts, impacting motor efficiency, smooth operation, and longevity. Proper lubrication and maintenance are crucial to prevent wear and ensure optimal performance.
32. How do you calculate the torque in an induction motor?
Torque in an induction motor is calculated using the formula:
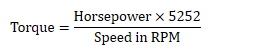
This formula relates torque, horsepower, and speed.
33. What methods are used for cooling induction motors?
Cooling methods include natural convection, forced air circulation using fans, liquid cooling systems, and more sophisticated techniques in larger or high-power motors to maintain optimal operating temperatures.
34. Can induction motors run at speeds higher than synchronous speed?
No, induction motors cannot run faster than synchronous speed under normal operating conditions. The difference between synchronous and rotor speed defines the motor’s slip.
35. How does a variable frequency drive (VFD) control the speed of an induction motor?
VFDs adjust the frequency and voltage of the power supplied to the motor, thereby changing the motor’s speed without altering the number of poles, providing precise control over the motor’s operations.
36. What are the effects of voltage fluctuations on induction motors?
Voltage fluctuations can adversely affect motor performance, causing overheating, increased losses, and potentially damaging insulation, bearings, and other components.
37. Can induction motors be used in parallel operation?
Yes, induction motors can be operated in parallel, provided they have similar specifications and are properly synchronized to prevent issues like circulating currents and imbalances.
38. How do you estimate the efficiency of an induction motor?
Efficiency can be estimated using the formula:

where output power is mechanical power and input power is electrical power.
39. What are the factors affecting the starting current in induction motors?
Starting current is influenced by load, voltage, motor size, and starting method. Direct-on-line starting, for instance, leads to higher starting currents compared to soft starters.
40. What role does the frequency of the power supply play in induction motor operation?
Frequency determines the motor’s synchronous speed and affects its speed and torque characteristics. Altering the frequency can vary the motor’s speed and performance.
41. What is cogging in an induction motor?
Cogging refers to the phenomenon where an induction motor experiences a reluctance torque ripple at low speeds due to magnetic interactions between the stator and rotor slots.
42. How do you mitigate cogging effects in induction motors?
Cogging can be reduced by altering the number of stator or rotor slots, using skewed rotor slots, or employing special rotor designs to minimize the impact of magnetic cogging.
43. Can induction motors operate in both forward and reverse directions?
Yes, induction motors can run in both forward and reverse directions by altering the phase sequence of the power supply or reversing the connection of any two motor terminals.
44. What are the advantages of using high-efficiency induction motors in industrial applications?
High-efficiency induction motors offer reduced energy consumption, lower operating costs, compliance with environmental regulations, and improved overall system efficiency.
45. How do you analyze the efficiency of induction motors under variable load conditions?
Analyzing efficiency under variable load involves performance testing across different load levels and mapping the motor’s efficiency curve to understand its performance range.
46. What methods are used for motor insulation testing in induction motors?
Insulation testing methods include megger tests, polarization index tests, and dielectric absorption ratio tests to assess insulation integrity and detect potential faults.
47. How does slip influence the torque in induction motors?
Slip is directly related to the induction motor’s torque. Higher slip values result in higher torque, allowing the motor to generate sufficient starting torque.
You May Want to Read
48. What are the challenges of starting high-power induction motors?
High-power induction motors often require specialized starting methods to manage high inrush currents and mechanical stresses during start-up to prevent damage to the motor and the power supply.
49. Can induction motors be used for high-precision speed control applications?
Induction motors might not be the optimal choice for high-precision speed control due to their inherent limitations in varying speed directly without external control devices like VFDs.
50. How do you calculate the power factor of an induction motor?
Power factor can be calculated using the formula:

It is a measure of the motor’s electrical efficiency.
51. How does the load affect the slip of an induction motor?
The slip increases as the load on an induction motor increases. Higher loads cause greater torque requirements, resulting in increased slip to maintain the necessary torque.
52. What are the different rotor types used in induction motors?
Common rotor types include squirrel cage rotors, wound rotor or slip-ring rotors, and double-cage rotors, each with distinct characteristics affecting motor performance.
53. How does the number of poles impact the speed of an induction motor?
The number of poles in an induction motor is inversely proportional to its speed. Motors with more poles have lower synchronous speeds and operate at lower speeds than those with fewer poles.
54. What is the importance of phase balancing in three-phase induction motors?
Phase balancing ensures even distribution of load across all phases, preventing overheating, minimizing losses, and enhancing motor efficiency and performance.
55. Can induction motors run at low speeds without overheating?
Induction motors can run at low speeds, but prolonged operation at very low speeds might lead to inadequate cooling and potential overheating issues.
56. How does the design of stator windings influence the performance of induction motors?
Stator winding design impacts motor efficiency, starting torque, and overall performance. Proper winding design ensures balanced magnetic fields and efficient operation.
57. What is the role of end rings in squirrel cage rotor design?
End rings in squirrel cage rotors facilitate the flow of induced currents within the rotor bars, ensuring a closed electrical circuit, which is vital for the rotor’s operation.
58. How do you determine the ideal insulation resistance value for an induction motor?
The insulation resistance value varies based on motor specifications and operating conditions. Regular insulation testing establishes a baseline for expected resistance values.
59. Can induction motors operate with high-frequency power supplies?
Induction motors are designed for specific frequencies and might not operate efficiently with high-frequency power supplies unless specifically designed for such applications.
60. What is the significance of the starting torque in induction motors?
Starting torque determines the motor’s ability to start under load conditions. Higher starting torque is necessary for applications with heavy loads or those requiring rapid acceleration.
61. How does the motor’s efficiency change with varying loads in an induction motor?
Efficiency typically peaks at or near the rated load of the motor. Deviation from this load level results in a decrease in efficiency due to increased losses.
62. What are the advantages and disadvantages of using a wound rotor in induction motors?
Wound rotor induction motors offer controllable starting torque and speed by external resistance, but they involve more complex construction and maintenance compared to squirrel cage rotors.
63. Can induction motors be used in variable load conditions?
Induction motors can handle variable loads. However, significant and frequent load variations might affect their efficiency and require careful consideration in design and operation.
64. How does the ambient temperature impact the performance of an induction motor?
High ambient temperatures can reduce the cooling efficiency of induction motors, potentially leading to overheating issues. Conversely, lower temperatures can enhance motor performance.
65. What are the methods used to protect induction motors from overcurrent and overload conditions?
Protection methods include using overload relays, circuit breakers, and thermal protection devices that interrupt power supply or provide warnings when the motor draws excessive current.
66. Can induction motors exhibit speed control without VFDs or variable frequency power supplies?
Induction motors have inherent limitations in direct speed control without external devices like VFDs or altering the frequency of the power supply.
67. How does the rotor resistance affect the performance of a wound rotor induction motor?
Rotor resistance influences the motor’s starting torque and speed control. Adjusting rotor resistance alters these characteristics in wound rotor motors.
68. What is the impact of rotor bar design on induction motor performance?
Rotor bar design affects motor starting torque, slip, efficiency, and reliability. Optimal bar designs ensure balanced performance and minimal losses.
69. Can induction motors be used for high-speed applications?
Induction motors are not typically designed for high-speed operations due to inherent limitations in synchronous speeds determined by frequency and the number of poles.
70. How do induction motors compare in terms of power factor and efficiency to other types of motors?
Induction motors often exhibit lower power factors compared to synchronous motors but offer good efficiency, making them widely used in various applications.
71. What role does the air gap between the stator and rotor play in induction motor efficiency?
The air gap influences magnetic flux density, affecting motor efficiency and performance. Proper air gap maintenance is critical for optimal motor operation.
72. Can induction motors be used in applications requiring high starting torque?
Yes, induction motors can provide high starting torque, especially in designs with higher rotor resistance or utilizing external resistors in wound rotor motors.
73. How do you calculate the motor slip from the frequency and speed of an induction motor?
Motor slip can be calculated using the formula:

74. What are the consequences of unbalanced voltage or current in a three-phase induction motor?
Unbalanced voltage or current can lead to uneven torque production, increased heating, reduced efficiency, and potential motor damage due to overload in motor on certain phases.
75. How does a soft starter differ from a variable frequency drive (VFD) in controlling induction motor speed?
A soft starter limits the initial current during motor start-up, while a VFD allows precise control over the motor’s speed by varying both the frequency and voltage.
76. What factors contribute to losses in induction motors?
Losses in induction motors include copper losses due to resistance in windings, core losses from hysteresis and eddy currents, and mechanical losses from friction and windage.
Induction motor interview questions frequently explore the role of core losses in the stator and their influence on overall efficiency.
77. What is the significance of the starting current in induction motors?
Starting current is often higher than the operating current and can lead to voltage drops and mechanical stresses. Effective control mechanisms are employed to manage this high starting current.
78. How does the insulation class of an induction motor affect its performance?
Insulation classes determine the motor’s thermal endurance and the maximum operating temperature. Higher insulation classes offer better thermal protection and durability.
79. Can induction motors be used in applications requiring high-speed control precision, like robotics or CNC machines?
Induction motors might not be the primary choice for such applications due to their inherent limitations in precise speed control without additional complex control systems.
80. How do you mitigate the effects of harmonics in induction motors caused by non-linear loads?
Harmonic filters, line reactors, and careful system design help mitigate harmonics induced by non-linear loads, reducing their impact on motor performance.
81. How does the number of poles affect the torque characteristics of an induction motor?
The number of poles influences the torque-speed curve of the motor. More poles usually result in higher torque at lower speeds, beneficial for applications requiring higher starting torque.
82. Can induction motors experience resonance issues, and how are these mitigated?
Induction motors might experience resonance due to their mechanical and electrical characteristics. Proper system design, vibration dampening, and control mechanisms help mitigate resonance.
83. What methods are used for motor protection against faults like overvoltage or undervoltage?
Relays, protective circuits, and voltage monitoring devices are used for protection against overvoltage or undervoltage conditions to prevent damage to the motor.
84. What are the characteristics of inrush current in induction motors during start-up?
Inrush current is significantly higher than the motor’s operating current and gradually decreases as the motor reaches its running speed.
85. How do you determine the ideal cooling method for an induction motor in different applications?
Cooling methods are selected based on factors such as motor size, operating environment, duty cycle, and required cooling efficiency, ensuring optimal heat dissipation.
86. What measures are taken to reduce the losses in the rotor of an induction motor?
Reducing rotor losses involves optimizing rotor design, minimizing eddy current losses, selecting suitable materials, and ensuring proper alignment of rotor components.
87. Can induction motors operate efficiently with non-sinusoidal power supplies?
Induction motors are designed for sinusoidal power supplies and might experience reduced efficiency or performance issues with non-sinusoidal power sources.
88. How does the load factor affect the operating efficiency of an induction motor?
Operating closer to the rated load improves efficiency. Deviation from the rated load, especially operating at light loads, can reduce the motor’s efficiency.
89. What methods are used for rotor bar testing in induction motors?
Rotor bar testing methods include current signature analysis, motor current spectrum analysis, and various electrical tests to detect potential rotor faults.
90. How do you adjust the speed of an induction motor using a pole-changing method?
Pole-changing methods involve altering the motor’s connections to change the number of poles, effectively modifying the motor’s speed-torque characteristics.
91. What role does the insulation resistance play in the operation of an induction motor?
Insulation resistance ensures the integrity of the motor’s insulation system, preventing faults and breakdowns caused by moisture, contamination, or deterioration.
92. How do you analyze the effects of varying loads on the efficiency of an induction motor?
Analyzing the motor’s efficiency under different loads involves conducting performance tests across varying load conditions and plotting efficiency curves for comprehensive assessment.
93. What methods are used for bearing condition monitoring in induction motors?
Bearing condition monitoring involves vibration analysis, temperature monitoring, lubrication analysis, and acoustic emission analysis to detect wear or faults in motor bearings.
94. How does the use of adjustable speed drives impact the efficiency of induction motors?
Adjustable speed drives, such as VFDs, allow better control of motor speed, resulting in improved efficiency, reduced energy consumption, and enhanced system performance.
95. What factors contribute to core losses in the stator of an induction motor?
Core losses in the stator arise from hysteresis and eddy currents generated in the magnetic core material, resulting in energy losses converted to heat.
96. Can induction motors be used in high-altitude environments, and how does altitude affect their performance?
Induction motors can operate at high altitudes, but reduced air density might lead to reduced cooling efficiency, affecting their thermal performance.
97. How do you calculate the starting time of an induction motor under specific load conditions?
Starting time depends on load, inertia, and starting torque. Complex calculations or simulations are used to estimate starting times under various scenarios.
98. What measures can be taken to prevent moisture ingress in induction motors used in humid environments?
Sealing the motor housing, proper insulation, using moisture-resistant materials, and maintaining proper ventilation help prevent moisture ingress and subsequent motor damage.
99. Can induction motors be retrofitted to improve their efficiency?
Retrofitting involves modifications like replacing older windings, using higher efficiency materials, or installing advanced control systems to improve the motor’s overall efficiency.
100. How do you ensure optimal power quality for induction motors in electrical systems?
Maintaining stable voltage levels, reducing harmonics, providing proper grounding, and ensuring consistent power supply contribute to optimal power quality for induction motors.
Direct Torque Control of Induction Motor
Direct Torque Control (DTC) is a method used to control the torque and flux of an induction motor. It offers precise and fast torque control without the need for a speed sensor, improving efficiency and performance.
Do Induction Motors Have Capacitors?
Induction motors typically do not have capacitors in their design. However, capacitor-start or capacitor-run motors use capacitors to improve starting torque and efficiency.
Does a Linear Induction Motor Use a Magnet?
No, a linear induction motor does not use permanent magnets. It operates based on electromagnetic induction, where alternating current produces a traveling magnetic field in the stator.
Does an AC Induction Motor Have Brushes?
No, an AC induction motor does not have brushes. It is a brushless motor where the rotor induces current through electromagnetic induction without the need for direct contact.
Does an Induction Motor Have Brushes?
No, an induction motor does not have brushes. The rotor is not directly connected to the stator and relies on electromagnetic induction to generate motion.
Does an Induction Motor Have Back EMF?
Yes, an induction motor generates back electromotive force (EMF) when the rotor rotates. This back EMF opposes the applied voltage and limits the motor’s current.
Does an Induction Motor Have a Commutator?
No, an induction motor does not have a commutator. Unlike DC motors, which use commutators to reverse the current, induction motors rely on alternating current and electromagnetic induction for operation.
Does an Induction Motor Have High Starting Torque?
Induction motors generally have low starting torque compared to other types like synchronous motors. However, certain designs such as the squirrel cage motor can offer higher starting torque.
Does an Induction Motor Have Magnets?
No, induction motors do not have permanent magnets. They operate based on electromagnetic induction, where the magnetic field is produced by current flowing through the stator coils.
Does an Induction Motor Need a Starter?
Yes, induction motors typically require a starter to limit the inrush current during startup. Starters help manage the initial power demand and prevent damage to the motor.
Does an Induction Motor Require Electricity?
Yes, an induction motor requires electricity to operate. It uses alternating current to generate a rotating magnetic field in the stator, which induces current in the rotor.
Does Tesla Use Induction Motors?
Yes, Tesla uses induction motors in some of its electric vehicles. These motors are highly efficient, reliable, and do not require permanent magnets.
As we wind down our exploration of induction motor interview questions, it’s evident that these inquiries serve as a compass, guiding us through the intricate realms of electrical machinery. They’re not merely questions but portals that unravel a candidate’s depth of understanding and practical prowess in this domain.
Discussing insulation resistance, bearing condition monitoring, core losses, and power quality considerations via these induction motor interview questions reveals the expansive skill set required to thrive in this field. Through these discussions, it’s apparent that a holistic comprehension of induction motor functionality is pivotal in addressing the ever-evolving challenges in electrical engineering. Could you discuss how power quality considerations factor into induction motor operation, a common theme in induction motor interview questions?
In summary, induction motor interview questions are like a rich tapestry, interwoven with threads of technical acumen and practical application. They aren’t just queries; they’re gateways that showcase a candidate’s ability to navigate complexities.
From exploring efficiency impacts to delving into operational intricacies and proposing real-world solutions through discussions on adjustable speed drives, harmonic mitigation, and retrofitting strategies, these questions encapsulate the comprehensive skill set necessary in mastering the intricate landscape of induction motor technology.
They reveal not just knowledge but the capacity to translate that knowledge into tangible solutions, illustrating the candidate’s readiness to tackle the challenges that lie ahead in this dynamic field.
Follow Us on Social:
Subscribe our Newsletter on Electrical Insights to get the latest updates in Electrical Engineering.
InductionMotor #MotorInterviewQuestions #ElectricalEngineering #MotorTheory #InductionMotorBasics #MotorTypes #InterviewPrep #ElectromagneticInduction #EngineeringJobs #MotorControl #ACMotors #InductionMotorApplications #ElectricalMachines #JobInterviewTips #TechInterview