Flyback Converter Design in 10 Steps: Comprehensive Guide
A flyback converter, also known as a flyback transformer or buck-boost converter, is a type of switched-mode power supply (SMPS) used to convert one DC voltage to another. It is commonly used in low to medium-power applications and has unique features that make it suitable for a variety of electronic devices and power sources.
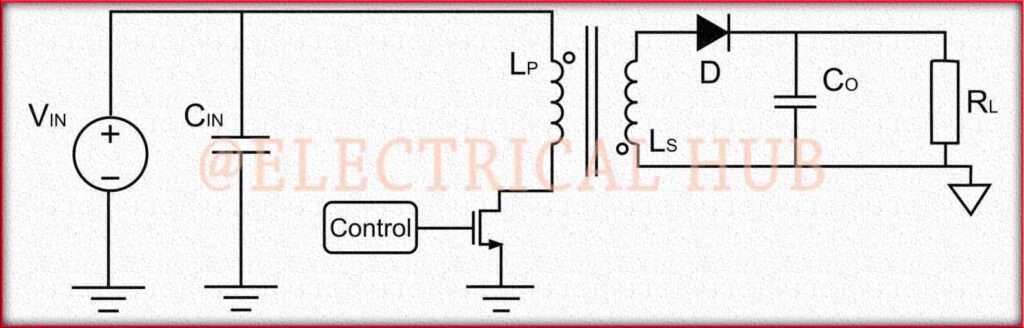
Read More About
How to design a DC DC flyback converter?
When it comes to designing a DC-DC flyback converter, it’s quite a comprehensive procedure, merging the world of power electronics theory with real-world practicality. To help illustrate the process, let’s embark on a simplified example.
In this scenario, we’re going to design a flyback converter to lower an initial voltage of 24V down to an output of 12V while delivering a current of 1A. Our goal is to ensure efficiency and meet some commonly applied specifications.
Step 1: Define Your Requirements
In this example, we aim to design a flyback converter with the following specifications:
- Input Voltage (Vin): 24V
- Output Voltage (Vout): 12V
- Output Current (Iout): 1A
- Efficiency (η): ≥ 85%
- Frequency (fsw): 100 kHz
Step 2: Calculate Duty Cycle (D)
The duty cycle (D) is determined by the ratio of the output voltage to the input voltage and is calculated as follows:

Step 3: Determine Turns Ratio (Np: Ns)
The turns ratio of the transformer (Np:Ns) is the reciprocal of the duty cycle:
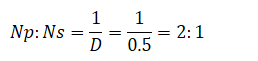
Step 4: Calculate Primary Current (Ip)
To calculate the primary current, use the following formula:
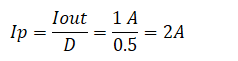
Step 5: Choose Transformer and Inductor Values
Choose a transformer and inductor that are a good fit for your needs by considering the right core material and size, taking into account the turns ratio and primary current. To keep things straightforward, let’s assume you’ve already made the selection of a transformer and inductor that align with your specific requirements.
Step 6: How to Design the Control Circuit
Creating the control circuit for a DC-DC flyback converter plays a vital role in the entire design process. This circuit holds the responsibility of maintaining the output voltage, guaranteeing stability, and offering protective functions. Let us walk you through the process of designing this control circuit step by step:
Choose the Right PWM Controller: The first step is to pick the ideal Pulse Width Modulation (PWM) Controller Integrated Circuit (IC) for your flyback converter. You have options such as UC3842, LT3757, or LM5113, which are commonly used. Ensure that the selected controller aligns with your input voltage and switching frequency requirements.
Set Your Feedback Approach: Next, you need to decide on the method for feedback in regulating voltage. For flyback converters, a voltage feedback loop is typically employed. This loop compares the actual output voltage to a reference voltage and adjusts the duty cycle accordingly.
Design Your Voltage Divider and Feedback Network In this step, you’ll design a voltage divider network to sample the output voltage. This voltage divider is comprised of two resistors, R1 and R2. Calculate the resistor values using the following formula:

Where:
- Vout is the desired output voltage.
- Vref is the reference voltage of your controller (typically a fixed value specified in the datasheet).
- R1 and R2 are the values of the resistors.
The Error Amplifier In this step, the error amplifier within the controller comes into play. It takes the output voltage (acquired from the voltage divider) and compares it with the reference voltage. This comparison generates an error signal used to control the duty cycle. Simply connect the error amplifier input to the output of the voltage divider.
Voltage Feedback Loop Compensation: Now, let’s focus on designing the compensation network for the voltage feedback loop. This network might include a compensation capacitor and possibly a compensation resistor.
The specific values of these components will depend on the controller’s requirements and the desired stability of the feedback loop. To get these values right, consult the controller’s datasheet and follow design guidelines for recommendations.
Soft-Start and Current Limit (if necessary): If your application calls for it, you’ll need to implement soft-start and overcurrent protection features. Soft-start is handy for gradually increasing the duty cycle to prevent inrush current, while current limit protection keeps a check on excessive current flow.
Frequency Control (if needed): Certain controllers offer the flexibility to adjust the switching frequency. If this feature is necessary for your design, you’ll have to craft the necessary circuitry to control the frequency.
Protection Features: To ensure the safety of your converter and the connected devices, it’s essential to incorporate protection features. These may include safeguards like overvoltage protection, undervoltage lockout, and thermal shutdown. The choice of these features should align with the specific requirements of your application.
Simulation and Testing: Before finalizing your design, it’s wise to simulate the control circuit using tools like LTSpice or PSpice. This step helps verify the performance. Once satisfied with the simulation, proceed to test the physical circuit on a prototype to confirm it meets the desired regulation, stability, and protection criteria.
Fine-Tuning: Finally, fine-tune your circuit as needed based on the results of your simulation and testing. This involves adjusting component values to optimize the control loop for the desired performance and transient response.
Step 7: How to Select Output Capacitor and Diode
Choosing the right output capacitor and diode is a pivotal aspect of designing your DC-DC flyback converter. These components are instrumental in maintaining output voltage stability, storing energy, and preventing voltage spikes. Here’s a straightforward guide on how to make these selections:
Capacitor Selection
Step 1: Picking the Output Capacitor
1. Determine Output Voltage Ripple (ΔVout): Start by calculating or specifying the acceptable voltage ripple for your application. A commonly targeted value is 1% of the output voltage. For instance, if your output voltage is 12V, you might find a 120mV ripple to be acceptable.
2. Estimate Load Current (Iout): Next, figure out the maximum output current that your circuit will draw.
3. Calculate the Required Output Capacitance (Co): Use the following formula to estimate the necessary output capacitance:
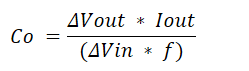
Where:
- Co is the required output capacitance.
- ΔVout is the acceptable voltage ripple (in volts).
- Iout is the maximum output current (in amperes).
- ΔVin is the input voltage ripple (considered as a fraction of the input voltage).
- f is the switching frequency of the converter.
This formula will help you find the output capacitance needed for your specific application.
In the next steps, we’ll explore further into diode selection and offer more insights to guide you through the process.
Diode Selection
1. Determine Output Current (Iout): Start by identifying the maximum output current that your flyback converter will deliver.
2. Estimate Diode Voltage and Current Ratings: Your chosen diode should have voltage and current ratings that exceed the maximum output voltage and current. It’s always wise to consider a safety margin to ensure reliability.
3. Select the Diode Type: In flyback converters, Schottky diodes are a popular choice. They’re favored for their fast recovery times and lower voltage drops. Ensure that the diode you select is well-suited for your specific application.
4. Check Reverse Recovery Time: Keep an eye on the diode’s reverse recovery time. A shorter recovery time is preferred as it helps minimize voltage spikes. You can find this parameter in the diode’s datasheet.
Step 3: Optional – Calculating Power Dissipation
If needed, you can calculate the power dissipation in the diode using the following formula:

Where:
- Pd is the power dissipation in the diode (in watts).
- Iout is the maximum output current (in amperes).
- Vf is the forward voltage drop of the diode (in volts).
- Vin is the input voltage (in volts).
This calculation can be helpful to ensure that the selected diode can handle the power dissipation without overheating or causing issues in your circuit.
Efficiency and Temperature Considerations
When you’re making choices regarding the output capacitor and diode for your flyback converter, it’s crucial to remember that these selections can significantly affect the converter’s overall efficiency and temperature. Make sure that the components you choose align with your performance goals and thermal requirements.
Simulation and Testing
Before finalizing your component choices, it’s a wise move to simulate their behavior within your circuit. Utilize simulation tools like LTSpice or PSpice to ensure that the components are compatible and meet your performance expectations.
Additionally, don’t skip the physical testing phase. Put your selected output capacitor and diode to the test in your circuit to verify that the ripple voltage falls within acceptable limits and that the diode operates as anticipated. This real-world testing step is vital for confirming that your components perform as expected in your specific flyback converter design.
Step 8: How to choose Snubber Circuit
Selecting a snubber circuit for your flyback converter is a crucial step in managing voltage spikes and ringing within your circuit. Here’s a practical guide on how to choose the right snubber circuit:
1. Voltage and Current Ratings Start by identifying the maximum voltage and current levels in your flyback converter circuit. This information is essential to ensure that the snubber components can handle the expected voltage and current demands.
2. Switching Frequency Know the switching frequency of your flyback converter, as it plays a significant role in shaping your snubber circuit’s design.
3. Calculating Snubber Parameters
Selecting Snubber Components: Typically, you’ll require a resistor (R) and a capacitor (C) for your snubber circuit. Use these guidelines to determine their values:
Resistor (R): Calculate the snubber resistor value using the formula
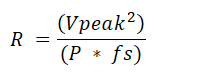
where Vpeak represents the peak voltage across the switch, P is the power rating of the resistor, and fs is the switching frequency.
Capacitor (C): Calculate the snubber capacitor value using

Here fs is the switching frequency and R is the snubber resistor value. Ensure that you select readily available resistor and capacitor values.
Snubber Diode (if necessary): Depending on your specific flyback converter circuit, you may need a diode in the snubber circuit to manage the energy stored in the snubber capacitor. Make sure that this diode has voltage and current ratings exceeding your requirements.
4. Snubber Damping Ratio Pay attention to the damping ratio (ζ) of your snubber circuit. It’s essential to strike a balance, ensuring that the snubber doesn’t overdamp or underdamp the switching transient. A damping ratio between 0.3 and 0.7 generally suits most applications.
5. Design for Efficiency Keep in mind the trade-off between snubber effectiveness and power loss in the snubber components. Optimize your snubber circuit to maintain efficiency while effectively controlling voltage spikes and ringing.
6. Simulation and Testing Put your snubber circuit to the test. Simulate its performance using tools like LTSpice or PSpice to ensure it behaves as expected. Additionally, perform physical testing on a prototype to verify that it effectively suppresses voltage spikes and ringing.
7. Fine-Tuning Lastly, fine-tune your snubber circuit based on the results of your simulation and testing. Adjust component values or even consider different snubber circuit types (such as RC or RCD) to optimize its performance for your specific flyback converter design.
Step 9: Simulate and Optimize
Use simulation tools like LTSpice or PSpice to simulate your design. Adjust component values, especially the transformer and inductor, based on simulation results to optimize efficiency and performance.
Step 10: Build and Test
Once the design is finalized, build a prototype and thoroughly test it under various operating conditions. Measure efficiency, output voltage regulation, and other critical parameters. Make any necessary adjustments based on test results.
Subscribe to our Newsletter “Electrical Insights Daily” to get the latest updates in Electrical Engineering. You can also Follow us on LinkedIn and Facebook to see our latest posts on Electrical Engineering Topics.
Worth Read Posts
- Methods of Electrical Earthing
- Electrical Earthing Important Types
- Plant Factor, Plant Capacity Factor, and Load Factor
- Difference Between Demand Factor and Diversity Factor
- Buck Converter Interview Questions
- DC DC Converter Interview Questions
- Transformer Electrical Interview
- Top 30 Op Amp Interview Questions
- Power Electronics Interview Questions
What is a flyback converter, and how does it work?
A flyback converter is a type of switching power supply used to step up or step down voltage levels. It operates by storing energy in a magnetic field and then releasing it to the output in a controlled manner. It’s commonly used in applications like LED drivers and low-power electronics.
What are the advantages of using a flyback converter?
Well, flyback converters have a few benefits. They’re relatively simple in terms of design, offer electrical isolation between the input and output, and can handle a wide input voltage range. This makes them great for a variety of applications.
Are there any drawbacks to using flyback converters?
Of course, there are trade-offs. Flyback converters can be less efficient compared to some other topologies, like the forward converter. They’re also typically used for low to moderate power levels, so they may not be the best choice for high-power applications.
What safety considerations should I keep in mind when working with flyback converters?
Safety is paramount. Because of the electrical isolation they provide, flyback converters are often used in products where user safety is crucial, like medical devices. So, make sure you’re following the right standards and guidelines, and always be cautious with high-voltage components.
Can a flyback converter handle different input voltages?
Yes, one of the advantages of flyback converters is that they can often handle a wide range of input voltages. This is achieved by adjusting the turns ratio of the transformer, allowing them to adapt to different input levels.
How do I calculate the transformer turns ratio for a flyback converter?
You’ll need to consider your input and output voltage requirements. The turns ratio (N) can be calculated as N = Vout / Vin, where Vout is the desired output voltage and Vin is the input voltage.
What are some common applications for flyback converters?
Flyback converters are commonly used in applications such as LED drivers, battery chargers, and isolated power supplies for low-power devices like sensors and IoT gadgets.
How can I improve the efficiency of a flyback converter?
To boost efficiency, pay attention to component selection, minimize switching losses, and ensure you’re operating the converter within its specified voltage and current limits. Using high-quality components and proper design techniques can go a long way in improving efficiency.
What are some common troubleshooting issues with flyback converters?
Problems can include output voltage instability, excessive heating, or poor regulation. When troubleshooting, start by checking your components, connections, and waveform measurements. It’s often a matter of fine-tuning your design or identifying faulty components.