DC to DC Converter 48V to 12V Design: Comprehensive Overview
DC to DC converter 48V to 12V Design involves creating an efficient and reliable circuit that steps down the higher DC voltage of 48 volts to a stable 12V output. This step-by-step guide will walk you through the design process, including calculations and an example, to achieve a well-functioning converter.
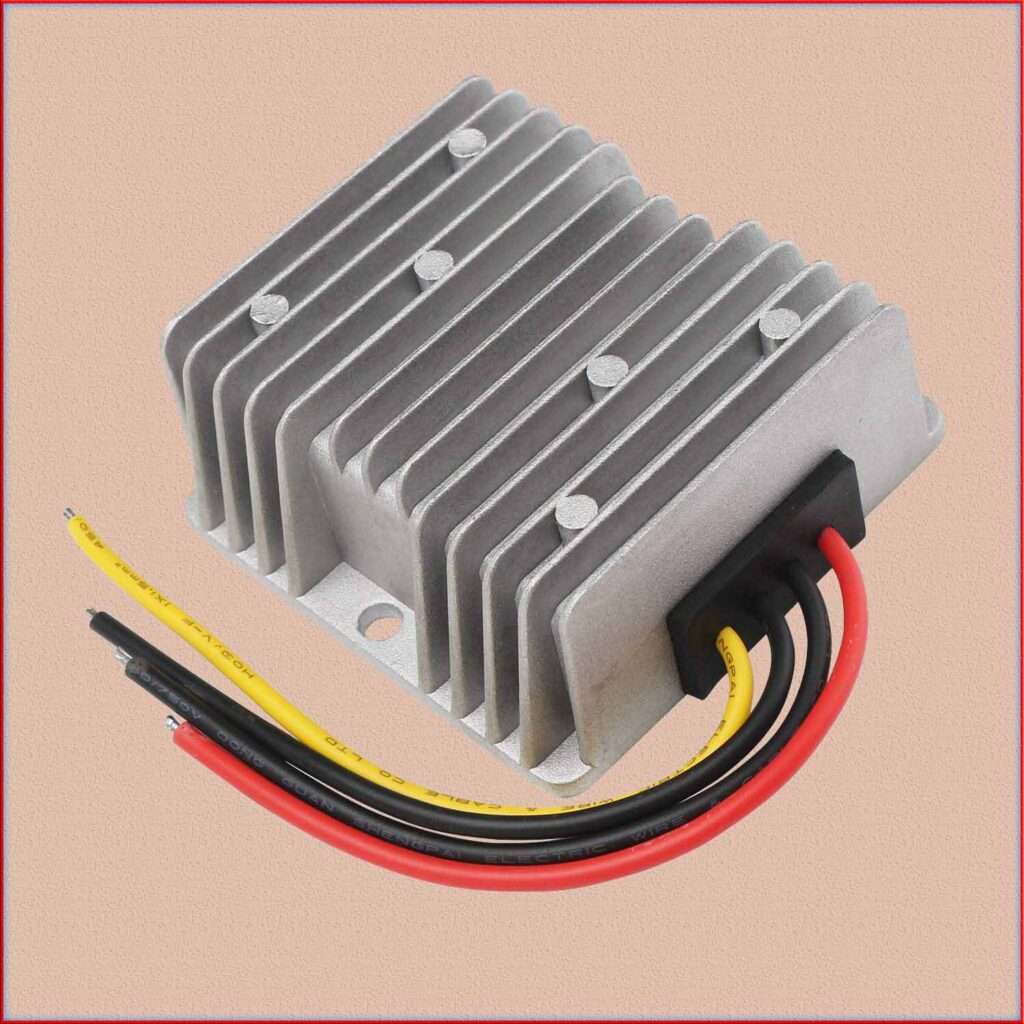
Read More
DC to DC converter 48V to 12V Design
Determine Design Specifications
Define the specifications of your DC to DC converter 48V to 12V design, including the input voltage (Vin), desired output voltage (Vout), output current (Iout), efficiency requirements, and any other specific constraints or requirements for your application. For this example, let’s design a buck converter with the following specifications:
- Vin = 48V
- Vout = 12V
- Iout = 5A
- Efficiency > 90%
Choose Switching Frequency
Select the switching frequency for your buck converter. The switching frequency determines how often the converter switches on and off. A higher switching frequency can lead to smaller and more compact components but may increase switching losses. For this example, let’s choose a switching frequency of 200 kHz.
Calculate Duty Cycle
The duty cycle (D) of a buck converter represents the ratio of time the switch is ON to the total switching period. It can be calculated using the formula:
D = Vout / Vin
In our example:
D = 12V / 48V = 0.25
Calculate Inductor Value
The inductor value (L) is crucial for energy storage and ripple current control in the buck converter. You can calculate the inductor value using the formula: L = (Vin – Vout) x (D / (fs x Iout))
Where fs is the switching frequency.
In our example:
L = (48V – 12V) x (0.25 / (200,000 Hz x 5A)) ≈ 3.2 μH
Choose Inductor and Capacitor
Select standard inductor and capacitor values that are close to the calculated values. For this design, let’s choose a 3.3 μH inductor and a 100 μF output capacitor.
Calculate Output Capacitor ESR
The equivalent series resistance (ESR) of the output capacitor affects the converter’s output ripple voltage. Calculate the output capacitor ESR using the formula:
ESR = (Vout x ΔIout) / (ΔVout x Iout)
Where ΔIout is the output current ripple and ΔVout is the output voltage ripple.
Let’s assume a 2% output voltage ripple for this example:
ΔVout = 0.02 x Vout = 0.02 x 12V = 0.24V
ESR = (12V x 5A) / (0.24V x 5A) = 50 mΩ (milliohms)
Choose MOSFET and Diode
Select appropriate MOSFET and diode components based on the input voltage, output current, and switching frequency. Ensure that they can handle the required voltage and current ratings.
Design Control Circuitry
Design the control circuitry for your buck converter. This circuitry usually includes a pulse-width modulation (PWM) controller, feedback circuit, and voltage regulation loop to ensure stable output voltage.
Simulate and Prototype
Simulate the DC to DC converter 48V to 12V design using software tools like LTspice or MATLAB to verify its performance. Build a prototype and test it to validate the design’s efficiency and stability.
Optimize and Fine-Tune
Based on simulation and testing results, fine-tune your DC to DC converter design to meet efficiency and performance goals. Consider factors like component losses, transient response, and thermal management during the optimization process.
In conclusion, DC to DC converter 48V to 12V design involves creating an efficient and reliable circuit that steps down the higher DC voltage to a stable 12V output. This step-by-step guide covered the calculations for duty cycle, inductor value, output capacitor ESR, as well as the selection of suitable components like inductors, capacitors, MOSFETs, and diodes.
Through simulation, prototyping, and optimization, you can create a well-functioning and reliable DC to DC converter that efficiently converts 48V to a stable 12V output for your specific application.
Subscribe to our Newsletter “Electrical Insights Daily” to get the latest updates in Electrical Engineering. You can also Follow us LinkedIn and Facebook to see our latest posts on Electrical Engineering Topics.