Cable Size for Motor: Important Guide
Choosing the appropriate cable size for motor applications is crucial for ensuring efficient performance, safety, and longevity of both the motor and the electrical system. This article will explore the factors influencing cable size selection, provide technical insights, and outline calculation methods to help you make informed decisions.
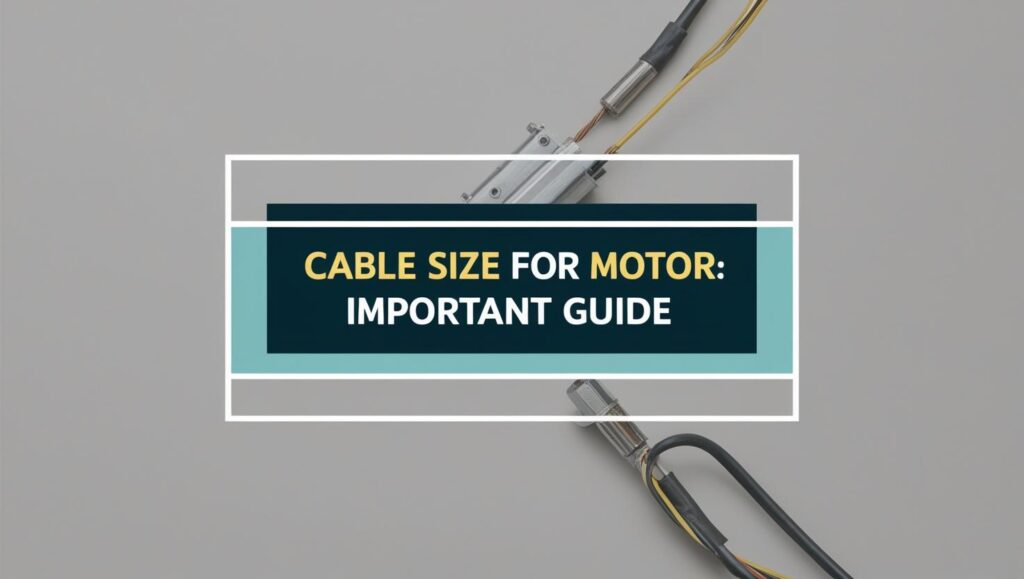
Table of Contents
Understanding Cable Size for Motors
The cable size for motor refers to the cross-sectional area of the conductor used to connect the motor to its power source. This size is determined based on several factors, including the motor’s power rating, voltage, distance from the power source, and installation conditions. Proper sizing is essential to prevent overheating, voltage drop, and potential failure of electrical components.
Importance of Correct Cable Sizing
- Safety: Undersized cables can overheat, leading to insulation failure or electrical fires.
- Efficiency: Properly sized cables minimize energy losses due to resistance.
- Cost-effectiveness: Oversized cables can lead to unnecessary expenses in materials and installation.
Cable Size for Motor Calculator
Factors Affecting Cable Size Selection
When determining the appropriate cable size for a motor, several factors must be considered:
1. Motor Power Rating
The power rating of the motor (in kilowatts or horsepower) directly influences the current that will flow through the cable. Higher power ratings require larger cables to handle increased current without overheating.
2. Voltage Level
The supply voltage (single-phase or three-phase) impacts the current drawn by the motor. For example:
- Single-phase systems typically operate at 230V.
- Three-phase systems usually operate at 400V or higher.
3. Distance from Power Source
The length of cable run affects voltage drop. Longer distances require larger cable sizes to compensate for voltage losses over distance.
4. Type of Conductor
Cables can be made from different materials, primarily copper and aluminum:
- Copper cables are more conductive and typically require smaller cross-sectional areas compared to aluminum cables.
- Aluminum cables are lighter and less expensive but have lower conductivity.
5. Installation Conditions
Environmental factors such as temperature, cable routing (in air or buried), and grouping with other cables can impact the current-carrying capacity of a cable.
Note: Use our online electrical load calculator for electrical load calculation here. You can also use voltage drop calculator for voltage drop calculation for cable selection in any single and three phase circuit here. Further explore our online electrical calculators to design your electrical systems in an efficient way.
Calculating Cable Size for Motors
To accurately calculate the required cable size for a motor, follow these steps:
Step 1: Determine Motor Specifications
Gather the following information:
- Power Rating (P): In kilowatts (kW) or horsepower (HP).
- Voltage (V): Supply voltage (e.g., 230V for single-phase or 400V for three-phase).
- Efficiency (η): Typically provided on the motor nameplate.
- Power Factor (pf): Necessary for AC motors; also found on the nameplate.
Step 2: Calculate Full Load Current
Use the following formulas based on whether you have a single-phase or three-phase motor:
For Single-Phase Motors:
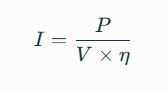
Where:
- I = Current in Amperes
- P = Power in Watts (1 kW = 1000 W)
- V = Voltage in Volts
- η = Efficiency (as a decimal)
For Three-Phase Motors:
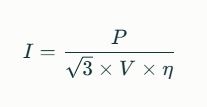
- I = Current in Amperes
- P = Power in Watts (1 kW = 1000 W)
- V = Voltage in Volts
- η = Efficiency (as a decimal)
Example Calculation
For a three-phase motor rated at 10 kW operating at 400V with an efficiency of 85%:
Convert power rating:
P=10kW=10,000W
Calculate full load current:
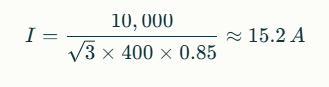
Consider Voltage Drop
Voltage drop should be limited to a maximum of 5% for motors. The formula for voltage drop is:
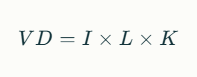
Where:
- VD = Voltage Drop
- I= Current in Amperes
- L = Length of cable run in meters
- K = Voltage drop constant (specific to cable type)
For example, if using copper cable with a K value of approximately 0.017 ohm-mm²/m:
Calculate voltage drop over a distance of 50 meters:
VD=15.2×50×0.017≈12.9V
Check if this is within acceptable limits:
Allowable drop at 400V:
Allowable VD=0.05×400=20V
Since 12.9V<20V, this is acceptable.
Selecting Appropriate Cable Size
Once you have calculated the full load current and considered voltage drop, you can select an appropriate cable size based on standard ratings.
Cable Size for Motor Table
Conductor Material | Current Rating per mm² | Recommended Cable Size |
---|---|---|
Copper | ~2.5 A | Based on calculated current |
Aluminum | ~1.5 A | Based on calculated current |
For example, if your calculated current is approximately 15 A:
For copper:
Required size:

For aluminum:
- Required size:

Conclusion
Selecting the correct cable size for motor applications is essential for ensuring safety and efficiency in electrical systems. By understanding how to calculate full load currents and considering factors such as voltage drop and conductor material, you can make informed decisions that enhance performance and reduce risks associated with electrical installations.
Key Takeaways
- Always calculate full load currents based on motor specifications.
- Consider voltage drop when selecting cable sizes.
- Use appropriate tables and formulas to determine suitable conductor sizes based on material type.
By following these guidelines, you can effectively manage your motor’s electrical demands while ensuring safety and compliance with relevant standards.
Follow us on LinkedIn, “Electrical Insights,” to get the latest updates on electrical engineering. You can also Follow us on LinkedIn and Facebook to see our latest posts on Electrical Engineering Topics.
Worth Read Posts
#MotorCableSizing, #CableSelectionGuide, #ElectricalEngineering, #MotorCableSize, #CableCalculation, #MotorEfficiency, #IndustrialElectrician, #ElectricalSafety, #CableSizing, #ElectricalInstallations, #EngineeringTips, #PowerTransmission, #ElectricalMaintenance, #HVACMotorWiring, #CableSizeCalculation