14 Power Transformer Parts: A Comprehensive Guide with PDF
In the field of electrical engineering and energy distribution, power transformer parts play a pivotal role in the efficient and seamless transfer of electricity. Power transformer parts are the intricate components that allow for the conversion of voltage levels, the maintenance of power quality, and the facilitation of electricity flow across diverse applications.
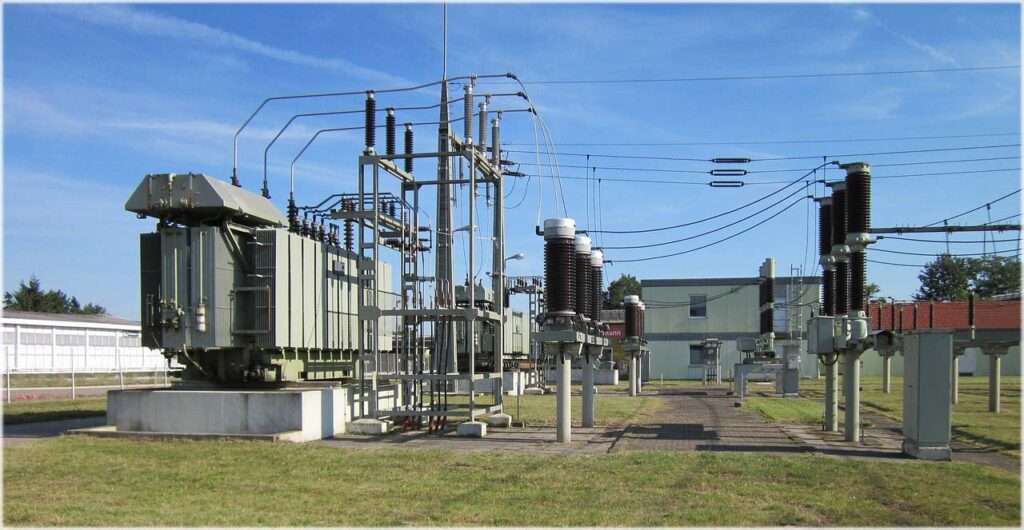
Read More About
Surrounding the core are the primary and secondary windings, meticulously wound coils of copper wire that facilitate the transformation of voltage levels. These windings are insulated to prevent electrical breakdowns and are essential for achieving the desired turns ratio, which determines the output voltage in relation to the input.
Moreover, power transformer parts include insulation systems that not only protect the windings but also ensure safe operation by preventing any unintended contact between conductive elements. Power transformer parts extend beyond the windings and core, encompassing vital auxiliary components that collectively enhance their efficiency and safety.
Cooling systems, often utilizing oil-immersed or forced air mechanisms, dissipate the heat generated during operation, maintaining optimal temperature ranges and preventing overheating. Tap changers, yet another critical component, allow for the adjustment of the turns ratio, enabling voltage regulation to accommodate varying load conditions.
Additionally, the inclusion of bushings ensures the secure and insulated connection between the internal windings and external electrical circuits. The integration of pressure relief devices, conservator tanks, and breathers collectively contribute to the safety and stability of power transformer parts, ensuring that these devices can withstand various operational stresses while maintaining their performance over time.
Power Transformer Parts
Understanding the functions and interactions of power transformer parts is necessary to ensure the reliability and longevity of power distribution networks.
1. Core
The core is an indispensable power transformer part that lies at the heart of its functionality, driving the conversion and transmission of electrical energy with remarkable efficiency. In the context of power transformer parts, the core’s primary function is to provide a low-reluctance path for the magnetic flux generated by the alternating current passing through the primary winding.
This magnetic flux is vital for inducing a corresponding voltage in the secondary winding, enabling voltage transformation as per the desired turns ratio. Constructed from high-quality laminated steel, the core minimizes energy losses by reducing eddy currents and hysteresis effects.
This optimization enhances the overall performance of the transformer, ensuring that a substantial portion of the electrical energy input is efficiently converted and transmitted, rather than dissipated as heat. The core’s design and construction are meticulously engineered to provide uniform magnetic flux distribution and minimize magnetic leakage.
By controlling magnetic flux within the core, power losses due to undesirable stray fields are mitigated, resulting in improved energy efficiency. This control over magnetic flux also aids in reducing electromagnetic interference and noise generation, ensuring clean and stable power output.
2. Windings
The windings, among the essential power transformer parts, serve as the conduits for the electrical energy conversion and transmission. These meticulously wound coils of copper wire form the primary and secondary windings, each with a distinct role in the transformation process.
The primary winding, connected to the input voltage source, serves as the origin of the magnetic flux that permeates the core. This interaction between the primary winding and the core induces a magnetic field that subsequently generates a voltage in the secondary winding.
This process of electromagnetic induction is at the heart of voltage transformation, enabling power transmission across different voltage levels, a fundamental function of power transformer parts.
The secondary winding, on the other hand, is where the magic of voltage transformation takes place. It is connected to the load and produces an output voltage that corresponds to the turns ratio established by the windings.
This output voltage is vital for meeting the requirements of various applications, from industrial processes to residential electricity supply. The insulation between the turns of the windings, a crucial aspect of power transformer parts, prevents unintended electrical contact and ensures that the induced voltage is effectively transferred to the load without any losses.
By engineering the number of turns in the windings, power transformer designers can achieve the desired step-up or step-down voltage conversion, aligning with the diverse needs of modern power distribution networks.
3. Insulation
Insulation stands as a protective component of power transformer parts, safeguarding the transformer’s reliable performance. In the context of power transformer parts, insulation serves a multifaceted purpose, primarily aimed at preventing electrical breakdown and ensuring the safe operation of the transformer.
The winding insulation, consisting of layers of insulating materials applied between the turns of the windings, creates a barrier that inhibits unwanted electrical contact. This insulation is essential to maintain the distinct voltage levels within the transformer, enabling efficient energy transfer across various power distribution networks.
By preventing unintended electrical discharge, insulation preserves the integrity of power transformer parts, reducing the risk of short circuits, arc flashes, and other potentially hazardous incidents. Beyond its protective role, insulation within power transformer parts contributes significantly to the device’s longevity and overall performance.
Insulation materials are selected and engineered to withstand the electrical, thermal, and environmental stresses encountered during operation. They shield the windings and other components from the harsh conditions of power fluctuations, voltage spikes, and temperature variations.
Insulation prolongs the device’s operational lifespan, reducing the need for frequent maintenance or replacement. Additionally, insulation materials possess dielectric properties that contribute to the efficient transmission of energy by minimizing energy losses due to leakage currents.
4. Winding Insulation
Among vital power transformer parts, winding insulation refers to the layers of insulating materials applied between the turns of the transformer’s windings. Its function is to prevent electrical breakdown between adjacent turns, ensuring safe and efficient voltage transformation.
Winding insulation safeguards against unwanted contact, reducing the risk of short circuits and ensuring the reliability of the transformer.
Materials: Common materials used for winding insulation include paper, pressboard, varnish, mica, and various synthetic materials. These materials are chosen for their high dielectric strength and thermal resistance, enabling them to withstand the electrical and thermal stresses experienced during transformer operation.
5. Oil Tank
The oil tank, a pivotal component among power transformer parts, serves as both a reservoir and a shield. The oil tank plays a dual role by housing the core and windings while containing the vital insulating oil.
This oil, often referred to as transformer oil, not only acts as a coolant but also enhances insulation, dissipates heat, and prevents electrical breakdown.
By immersing the core and windings in the cooling embrace of the oil, the transformer remains within optimal temperature ranges, thus preventing overheating that could compromise the performance of other power transformer parts.
Furthermore, the oil tank within the ensemble of power transformer parts acts as a protective cocoon, guarding the internal components against external environmental factors. It acts as a barrier against moisture and contaminants that could potentially degrade the insulating properties of the oil or affect the performance of the transformer.
This safeguarding role is especially crucial in outdoor installations where power transformer parts are exposed to changing weather conditions. The oil tank’s design and construction are strategically engineered to provide structural integrity and prevent oil leaks, ensuring that the transformer can withstand mechanical stresses and vibrations without compromising its insulating capabilities.
6. Cooling System
Transformers experience temperature rises due to the electrical energy losses that occur during the conversion and transmission of electricity. These losses result in the production of heat, which, if not effectively managed, can lead to overheating and potential damage to the transformer’s components.
Cooling systems are integral parts of power transformers and play a vital role in maintaining the transformer’s operational efficiency, reliability, and safety. There are several types of cooling systems employed in power transformers:
What are Four Methods or Systems of Cooling??
Oil Immersed Cooling: This is one of the most common cooling methods for power transformers. The transformer’s core and windings are immersed in an insulating oil that acts as a coolant and heat transfer medium. The oil absorbs heat generated during operation and carries it away from the core and windings, dissipating it through the transformer’s tank and radiators.
Forced Air Cooling: In this method, fans or blowers are used to direct external air over the transformer’s radiators. The moving air absorbs the heat from the radiators, carrying it away and cooling the transformer. This method is often used in smaller transformers and substations.
Natural Convection Cooling: This cooling technique relies on the natural movement of air due to temperature differences. The warm air rises, creating a flow that draws in cooler air to replace it. Natural convection cooling is often used in smaller transformers with lower heat generation.
Liquid Immersed Cooling: Apart from oil, other types of liquids can be used as coolants. Some transformers use synthetic liquids with higher heat transfer capabilities than traditional mineral oil.
The choice of cooling system depends on factors such as the transformer’s size, power rating, application, and environmental conditions. The primary goal of any cooling system is to maintain the transformer’s temperature within safe operating limits, ensuring optimal performance and longevity while minimizing the risk of equipment failure.
7. Transformer Oil
Among the crucial power transformer parts, transformer oil, also known as insulating oil or mineral oil, serves as a vital component within transformers. Its function is multifaceted: it acts as both an electrical insulator and a cooling medium.
Transformer oil helps insulate the winding turns from each other and from the transformer’s core, preventing electrical breakdown. Simultaneously, it plays a pivotal role in dissipating the heat generated during transformer operation, maintaining optimal operating temperatures.
Transformer oil is predominantly derived from mineral oil, chosen for its high dielectric strength and thermal stability. However, alternative insulating oils like silicone-based and ester-based oils are also used, offering enhanced fire safety, environmental friendliness, and extended operational life compared to traditional mineral oil.
8. Oil Gauge
An oil gauge is a device designed to measure and display the level of insulating oil within the conservator tank of a transformer. Its primary function is to provide an accurate visual indication of the oil level, allowing operators to monitor the transformer’s oil volume and ensure it remains within safe operating limits.
Monitoring the oil level is essential for maintaining proper cooling, insulation, and overall functionality of the transformer. The oil gauge is typically connected to the conservator tank through a sealed connection point. It includes a transparent viewing portion that allows operators to visually assess the oil level within the tank.
Some advanced oil gauges may also include electronic sensors that provide remote monitoring capabilities, sending real-time data to control systems for efficient management.
9. HV Load Switch
A high-voltage (HV) load switch is a significant component within power transformer parts that serves as a device for interrupting or connecting the flow of electrical current in high-voltage circuits. Its primary function is to provide a means to control the connection or disconnection of a load from the power system.
HV load switches are commonly used in electrical substations and distribution networks to isolate faulty sections, facilitate maintenance, and control the distribution of electrical power. HV load switches are connected to the high-voltage circuit using appropriate insulation and safety measures.
They are often integrated into switchgear assemblies, designed to withstand the high voltage and current levels present in high-voltage systems. HV load switches can be manually operated or remotely controlled, offering flexibility in managing power distribution.
10. Tap Changer
A tap changer is a specialized component within power transformer parts that allows for the adjustment of the turns ratio between the primary and secondary windings. The turns ratio determines the transformation ratio of voltage levels, enabling power transformers to accommodate variations in input voltages and load conditions.
By altering the position of the tap changer, the number of turns in the winding can be modified, resulting in a change in the output voltage. Tap changers are particularly crucial in power systems where voltage fluctuations are common, ensuring that the output voltage remains stable despite changes in the input or load.
They are employed to regulate voltage levels within permissible limits, enhancing the adaptability and efficiency of power transformer parts in diverse applications.
This adjustable mechanism allows for the fine-tuning of voltage levels, adapting the transformer’s output to varying conditions. Through its role in the intricate interplay of power transformer parts, the tap changer ensures that voltage transformations remain accurate and consistent, catering to the dynamic demands of modern power distribution networks.
Why Tap Changer is always on High Voltage Side?
4 Reasons for Tap Changers to be on HV Side
Tap changers are often located on the high voltage side of power transformers due to practical and operational considerations related to voltage regulation and equipment design. Here’s why tap changers are typically placed on the high voltage side:
Voltage Regulation: The primary purpose of a tap changer is to regulate the output voltage of the transformer. Placing the tap changer on the high voltage side allows for finer control over the output voltage, which is critical for maintaining voltage stability within acceptable limits in power distribution networks.
Minimizing Current: On the high voltage side, the current is lower than on the low voltage side for a given power level. This means that the tap changer components (such as the contacts and switching mechanisms) can be designed to handle lower currents, reducing wear and tear and improving the tap changer’s reliability and lifespan.
Efficiency and Losses: Voltage transformation occurs between the primary and secondary windings. By adjusting the turns ratio on the high voltage side, changes in voltage are translated more efficiently to the secondary side, helping to achieve the desired output voltage while minimizing energy losses.
Design Constraints: The design and construction of the transformer itself can influence the location of the tap changer. High voltage winding designs often provide more space for accommodating tap changer mechanisms without compromising the overall structure and integrity of the transformer.
Overall, placing the tap changer on the high voltage side aligns with the goals of effective voltage regulation, optimal efficiency, and maintaining the transformer’s long-term performance and reliability.
11. Bushing
A bushing is a vital component among power transformer parts that provides a safe and insulated passage for electrical conductors to pass through the walls of the transformer tank or other enclosures. Bushings are crucial for connecting the internal components, such as windings, to the external electrical circuits while preventing any electrical breakdown or leakage.
They are designed to withstand high voltage differences between the internal and external parts of the transformer, ensuring the safety of personnel and the integrity of the electrical system.
Bushings are constructed using insulating materials, and their design takes into account factors like insulation properties, voltage ratings, and environmental conditions to maintain effective insulation and electrical isolation.
By incorporating reliable insulating materials and precise engineering, bushings ensure that power flows seamlessly between the internal windings and external circuits while safeguarding against electrical leakage and breakdown.
A worth Read Posts
12. Conservator Tank
A conservator tank is a vital among power transformer parts that serves as a reservoir for transformer oil, also known as insulating oil. This tank is typically attached to the main transformer tank and is connected through a pipeline. The primary function of the conservator tank is to compensate for the expansion and contraction of transformer oil due to temperature changes.
As the transformer operates, the oil heats up and expands, and conversely, it cools down and contracts when the transformer is not in operation.
The conservator tank is designed with an air space above the oil level. This air space acts as a buffer for the expanding and contracting oil. When the oil expands, excess oil flows into the conservator tank, occupying the available air space.
Similarly, when the oil contracts, oil is drawn back from the conservator tank to compensate for the reduction in volume. This dynamic process ensures that the transformer’s oil level remains relatively constant, minimizing the risk of oil leakage and maintaining proper cooling and insulation properties.
13. Breather
A breather is a critical within power transformer parts that plays a pivotal role in maintaining the quality of the insulating oil present in the transformer. A breather is typically connected to the conservator tank and serves as a means to control the exchange of air between the conservator tank and the external environment.
Its primary purpose is to prevent moisture and other contaminants from entering the transformer’s insulating oil. The breather contains desiccant materials, often silica gel, which have a strong affinity for moisture.
As air is drawn into the breather due to the contracting oil within the transformer, the desiccant material absorbs moisture from the incoming air. This prevents moisture from entering the transformer’s insulating oil, which could degrade the oil’s dielectric properties and insulation capabilities over time.
As the oil heats up and expands during operation, the breather allows air to exit the conservator tank, ensuring a continuous cycle of air exchange without allowing moisture-laden air to enter. By maintaining the dryness of the insulating oil, the breather contributes to the overall performance of power transformer parts.
14. Pressure Relief Device
Among the essential power transformer parts, a pressure relief device serves as a crucial safety feature designed to mitigate the risks associated with sudden increases in internal pressure within the transformer tank.
During abnormal conditions such as short circuits, internal faults, or extreme load variations, excessive heat can be generated, leading to a rapid increase in pressure within the transformer tank. This pressure buildup could potentially lead to catastrophic failure if left unchecked.
The pressure relief device, also known as a pressure relief valve, functions as a pressure sensitive mechanism. It is installed on the transformer tank and is designed to open when the internal pressure surpasses a safe threshold.
When the pressure exceeds this preset limit, the valve opens, allowing the release of gases and pressure from the tank into a controlled venting area. This controlled release prevents the tank from rupturing and minimizes the risk of fire or explosion.
Follow us on LinkedIn”Electrical Insights” to get the latest updates in Electrical Engineering. You can also Follow us LinkedIn and Facebook to see our latest posts on Electrical Engineering Topics.
Worth Read Posts
Transformers: Important Types
Transformer Oil Testing: 9 Important Tests
10 Transformer Tests Before Commissioning
Hysteresis Loss and Eddy Current Loss
Transformer Electrical Interview Questions
What is Demand Factor and Diversity Factor?