L298N Motor Driver: A Comprehensive Guide
Table of Contents
Introduction
The L298N motor driver is a versatile integrated circuit widely used to control and drive DC motors and stepper motors. In this comprehensive guide, we will delve into the intricacies of the L298N motor driver, exploring its features, working principles, and practical applications. Whether you’re a beginner or an experienced hobbyist, this article aims to provide valuable insights into maximizing the performance of your motor control projects using the L298N motor driver.
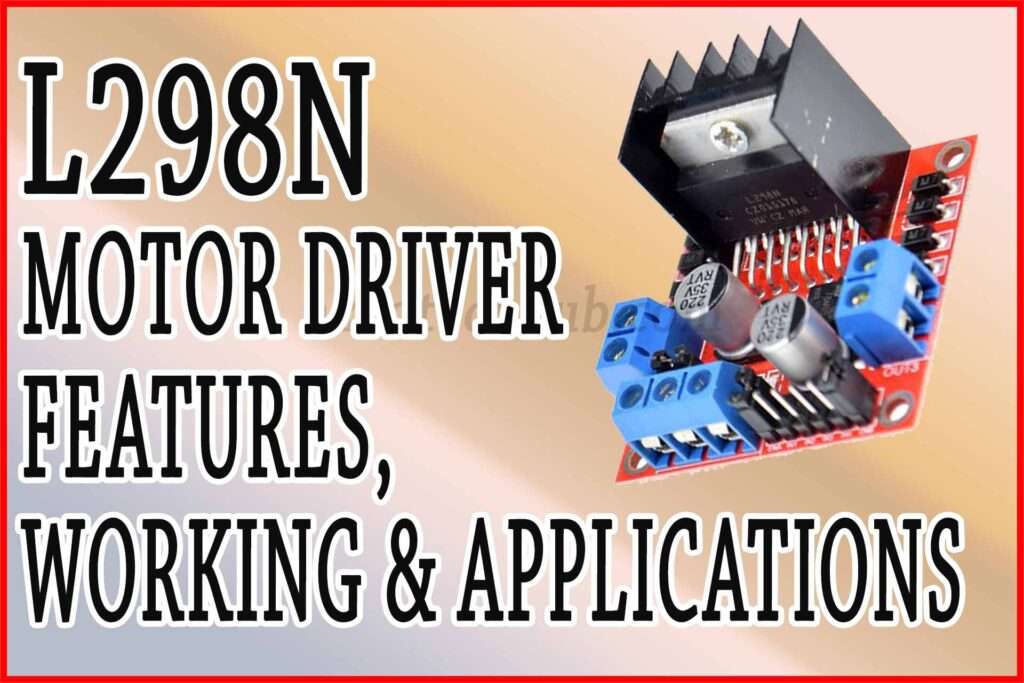
What is the L298N Motor Driver?
The L298N Motor Driver is a popular integrated circuit (IC) module used for controlling and driving DC motors and stepper motors. It is commonly used in robotics, automation, and other projects that require precise motor control. The L298N module consists of two H-bridges, capable of driving two DC motors bidirectionally or one stepper motor.
The L298N motor driver operates based on the H-bridge configuration, which allows the control of the direction and speed of motors. It accepts input signals from a microcontroller or other control devices to control the rotation and movement of the motors. By controlling the voltage and current supplied to the motors, the L298N motor driver enables precise control over motor speed and direction.
The L298N motor driver has several key features that contribute to its popularity. It can handle a wide range of voltage inputs, typically from 5V to 35V, making it compatible with various power sources. It has built-in protection mechanisms such as overcurrent protection and thermal shutdown, which safeguard the IC and connected components from damage due to excessive current or overheating.
The module offers separate power supply inputs for the logic circuitry and motor-driving circuitry, allowing you to use different voltage levels for each. This feature enhances flexibility in designing motor control systems. The L298N motor driver also provides enable pins for each motor channel, enabling the user to selectively enable or disable individual motors as needed.
With its versatility and robustness, the L298N motor driver finds applications in a wide range of projects. It is commonly used in robotics projects for controlling wheels, arms, and other motorized components. It is also utilized in CNC machines, automation systems, smart vehicles, and other applications where precise motor control is required.
To optimize the performance of the L298N motor driver, it is important to consider factors such as efficient motor control techniques, proper heat dissipation, and appropriate power supply configurations. Understanding the principles and capabilities of the L298N motor driver enables users to leverage its features effectively and achieve reliable motor control in their projects.
Working Principle of the L298N Motor Driver
The working principle of the L298N Motor Driver revolves around the concept of H-bridges, which allow bidirectional control of motors. The L298N module consists of two H-bridges, one for each motor channel, allowing independent control of two DC motors or a single stepper motor.
Each H-bridge in the L298N motor driver configuration consists of four power MOSFETs (Metal-Oxide-Semiconductor Field-Effect Transistors) or bipolar transistors. These transistors are arranged in a specific configuration that enables the control of motor direction and speed.
To understand the working principle, let’s consider a single motor channel within the L298N motor driver. Each motor channel consists of two pairs of transistors, usually referred to as the upper (U1 and U2) and lower (L1 and L2) transistors.
To control the motor’s direction, the upper and lower transistors of one side of the H-bridge are turned on or off selectively. For example, if U1 and L2 are turned on while U2 and L1 are turned off, the current flows from the power supply through U1 and the motor, creating a forward motion. By reversing the configuration and turning on U2 and L1 while turning off U1 and L2, the current flows in the opposite direction, resulting in the motor’s backward motion.
To control the motor’s speed, a technique called Pulse Width Modulation (PWM) is commonly used. PWM involves rapidly switching the transistors on and off at a high frequency. By varying the ratio of on-time to off-time, the effective voltage supplied to the motor is adjusted, thus controlling the motor’s speed.
The control signals required to operate the L298N motor driver typically come from a microcontroller or other control devices. The L298N module has input pins for controlling the state of the upper and lower transistors in each H-bridge. By providing the appropriate logical signals to these input pins, the desired motor direction and speed can be achieved.
It’s worth noting that the L298N motor driver also includes enable pins for each motor channel. These enable pins allow the user to enable or disable individual motors as needed, providing an additional level of control.
By understanding the working principle of the L298N motor driver and utilizing the appropriate control signals, users can achieve precise control over motor direction and speed, making it a versatile solution for various motor control applications.
L298N Motor Driver Features and Benefits
The L298N Motor Driver offers a range of features and benefits that make it a popular choice for motor control applications. Here are some key features and benefits of the L298N Motor Driver:
Dual H-Bridge Configuration: The L298N Motor Driver module consists of two H-bridges, allowing independent control of two DC motors or a single stepper motor. This configuration enables bidirectional control of motors, offering flexibility in controlling motor direction and movement.
Wide Voltage Range: The L298N Motor Driver can handle a wide range of voltage inputs, typically from 5V to 35V. This feature allows compatibility with various power sources and makes it suitable for a wide range of applications.
High Current Capacity: The L298N Motor Driver is designed to handle high currents, typically up to 2A per channel and with peak currents up to 3A. This capability makes it suitable for driving motors with higher power requirements.
Built-in Protection Mechanisms: The L298N Motor Driver incorporates built-in protection mechanisms to ensure the safety of the module and connected components. It includes features like overcurrent protection and thermal shutdown, which help prevent damage caused by excessive current or overheating.
Separate Power Supply Inputs: The L298N Motor Driver offers separate power supply inputs for the logic circuitry and motor-driving circuitry. This feature allows users to use different voltage levels for each, providing flexibility in designing motor control systems.
Enable Pins for Motor Channels: The L298N Motor Driver includes enable pins for each motor channel. These enable pins enable the user to selectively enable or disable individual motors as needed, providing an additional level of control and power management.
Compatibility with Microcontrollers: The L298N Motor Driver is compatible with various microcontrollers and control devices. It can be easily interfaced with microcontrollers like Arduino, Raspberry Pi, and other popular platforms, making it convenient for integration into existing projects.
Versatile Applications: The L298N Motor Driver finds applications in a wide range of projects, including robotics, automation, CNC machines, smart vehicles, and more. Its versatility makes it suitable for controlling motors in different contexts and industries.
By leveraging the features and benefits of the L298N Motor Driver, users can achieve precise motor control, ensure the safety of the system, and drive various types of motors effectively. Whether you are a hobbyist or an engineer working on motor control projects, the L298N Motor Driver provides a reliable and flexible solution.
Applications of the L298N Motor Driver
The L298N Motor Driver finds applications in various projects and industries that require precise control and driving of motors. Here are some common applications where the L298N Motor Driver is widely used:
Robotics: The L298N Motor Driver is extensively used in robotics projects to control the movement of robotic platforms, including wheeled robots, robotic arms, and humanoid robots. It enables accurate control over the motors, allowing robots to navigate, perform tasks, and interact with their environment.
Automation Systems: In industrial automation and home automation systems, the L298N Motor Driver is utilized to control motors in conveyor belts, automated doors, robotic arms, and other motorized components. It enables seamless integration of motors into the automation process, enhancing efficiency and productivity.
CNC Machines: Computer Numerical Control (CNC) machines rely on precise motor control for accurate positioning and movement of cutting tools. The L298N Motor Driver is employed to control stepper motors or DC motors in CNC machines, enabling high precision and repeatability in manufacturing processes.
Smart Vehicles: The L298N Motor Driver is commonly used in smart vehicle projects, including autonomous cars, remote-controlled vehicles, and drones. It allows control over the motors responsible for propulsion, steering, and stabilization, enabling smooth and responsive movement.
Home Appliances: The L298N Motor Driver can be found in various home appliances that incorporate motorized components, such as automated curtains, motorized blinds, fans, and robotic vacuum cleaners. It enables precise motor control in these devices, enhancing functionality and user experience.
Educational Projects: The L298N Motor Driver is often utilized in educational settings for teaching motor control principles and robotics. It provides a hands-on learning experience, allowing students to build and control their own robots or motorized projects.
Hobbyist Projects: The versatility and affordability of the L298N Motor Driver make it popular among hobbyists and DIY enthusiasts. It can be used in a wide range of hobby projects, including RC (remote-controlled) vehicles, motorized toys, home automation prototypes, and more.
Industrial Machinery: The L298N Motor Driver is employed in various industrial machinery applications, such as conveyor systems, packaging machines, and production line equipment. It facilitates precise control over the motors involved in these processes, ensuring smooth operation and optimal productivity.
These are just a few examples of the numerous applications where the L298N Motor Driver is utilized. Its ability to control and drive motors accurately and reliably makes it a versatile choice for a wide range of motor control projects in various industries.
Optimizing Performance with the L298N Motor Driver
To optimize the performance of the L298N Motor Driver and ensure efficient motor control, consider the following tips and techniques:
Efficient Motor Control Techniques: Implement efficient motor control techniques such as Pulse Width Modulation (PWM) to control the speed of the motors. By varying the duty cycle of the PWM signal, you can achieve smooth and precise speed control while minimizing power consumption.
Heat Dissipation: The L298N Motor Driver can generate heat, especially when driving high-power motors or operating at high currents. Ensure proper heat dissipation by using heat sinks or cooling fans. This helps prevent overheating, which can lead to reduced performance or damage to the motor driver.
Power Supply Considerations: Provide a stable and adequate power supply to the L298N Motor Driver. Ensure that the power supply can deliver sufficient current to meet the motor’s requirements. Using a separate power supply for the motor-driving circuitry and the logic circuitry can help minimize interference and improve overall performance.
Motor Current Limiting: Consider implementing current limiting measures to protect the L298N Motor Driver and the connected motors. This can be achieved by using current-limiting resistors, external current sensors, or incorporating current protection circuits. These measures help prevent excessive current from damaging the driver or the motors.
Wiring and Connection Quality: Ensure proper wiring and secure connections between the L298N Motor Driver and the motors. Loose or inadequate connections can cause voltage drops, affecting motor performance. Use proper connectors, soldering techniques, and gauge appropriate wire sizes to minimize resistance and maintain reliable connections.
Motor Specifications and Compatibility: Familiarize yourself with the specifications and limitations of the motors you are using. Ensure that the L298N Motor Driver can handle the voltage and current requirements of the motors. Matching the motor specifications with the capabilities of the motor driver optimizes performance and ensures reliable operation.
Testing and Calibration: Test and calibrate the motor control parameters to achieve desired performance. Fine-tuning the control signals, PWM frequency, and motor acceleration/deceleration profiles can optimize the motor’s response and overall system performance.
Consider Advanced Motor Control Techniques: Explore advanced motor control techniques such as PID (Proportional-Integral-Derivative) control or sensor feedback for enhanced precision and stability, especially in applications that require high positional accuracy or velocity control.
By implementing these optimization techniques, you can maximize the performance of the L298N Motor Driver, achieve efficient motor control, and ensure the reliability and longevity of the motor control system in your projects.
Troubleshooting and Common Issues
While working with the L298N Motor Driver, you may encounter certain common issues. Here are some troubleshooting tips to help you address these issues:
Motor Not Responding:
- Check the wiring connections between the L298N Motor Driver and the motor. Ensure that the motor is properly connected to the correct motor channel and that the polarity is correct.
- Verify that the control signals (PWM and direction) are correctly connected to the L298N Motor Driver’s input pins.
- Ensure that the power supply is providing sufficient voltage and current to the motor driver.
- Check if the enable pin for the motor channel is properly set to enable the motor.
Overheating
If the L298N Motor Driver is getting excessively hot during operation, check for proper heat dissipation. Ensure that heat sinks or cooling fans are properly installed to dissipate the heat generated by the motor driver.
- Consider reducing the load on the motor or adjusting the motor’s speed to lower the overall power dissipation.
- Verify that the motor driver is not being operated beyond its current capacity. If necessary, implement current limiting measures to protect the motor driver and prevent overheating.
Motor Jerking or Vibrating
Adjust the PWM frequency to a suitable value. Very low or very high frequencies can cause motor instability. Experiment with different frequencies to find the optimal setting for smooth motor operation.
- Check the motor power supply voltage. Ensure that it is stable and within the recommended range for the motor.
- Inspect the motor driver’s power connections and ensure they are secure. Loose connections can cause voltage drops and affect motor performance.
Unexpected Motor Behavior
- Check the control signals sent to the L298N Motor Driver. Make sure they are correct and properly synchronized.
- Inspect the wiring and connections to ensure there are no loose or shorted wires that may cause erratic behavior.
- Verify that the motor driver’s power supply is stable and providing sufficient voltage and current for the motors.
Excessive Current Draw
- Confirm that the motor driver can handle the current requirements of the motors. Check the datasheet or specifications for the maximum current rating of the L298N Motor Driver.
- Inspect the motor connections for any short circuits or improper wiring that may be causing excessive current draw.
- Consider implementing current-limiting measures such as current-limiting resistors or external current sensors to protect the motor driver and prevent damage.
Motor Stall
- If the motor stalls or does not have enough torque to move the load, verify that the power supply is providing sufficient voltage and current.
- Check the mechanical aspects of the motor system, such as friction or binding, which can cause the motor to stall.
- Consider adjusting the motor control parameters, such as increasing the PWM duty cycle or adjusting the motor acceleration profile, to provide enough power to overcome the load.
By troubleshooting these common issues and taking appropriate corrective actions, you can ensure the smooth operation of the L298N Motor Driver and achieve reliable motor control in your projects.
Conclusion
In conclusion, the L298N Motor Driver is a versatile and widely used integrated circuit module for controlling and driving DC motors and stepper motors. Its dual H-bridge configuration allows independent control of two motors, providing bidirectional control and precise motor movement.
The L298N Motor Driver offers several key features and benefits, including a wide voltage range, high current capacity, built-in protection mechanisms, separate power supply inputs, and enable pins for individual motor control. These features make it suitable for various applications such as robotics, automation systems, CNC machines, smart vehicles, and more.
To optimize the performance of the L298N Motor Driver, it is important to implement efficient motor control techniques, ensure proper heat dissipation, provide stable and adequate power supply, and consider factors such as motor current limiting and wiring quality. Additionally, troubleshooting common issues related to motor response, overheating, jerking, unexpected behavior, excessive current draw, and motor stall can help ensure smooth operation and reliable motor control.
By leveraging the capabilities of the L298N Motor Driver and following best practices, you can achieve precise motor control, protect the motor driver and connected components, and successfully implement motor control systems in your projects. Whether you are working on robotics, automation, or hobbyist projects, the L298N Motor Driver serves as a valuable tool for driving and controlling motors effectively.
Follow us on LinkedIn”Electrical Insights” to get the latest updates in Electrical Engineering. You can also Follow us LinkedIn to see our latest posts.