What are Common VFD Troubleshooting Tips?
Variable Frequency Drives (VFDs) are essential in modern industrial automation. They control motor speed, reduce energy consumption, and improve system performance. But like any electronic device, VFDs can face issues during operation. Knowing the right VFD troubleshooting tips can help avoid downtime, reduce maintenance costs, and extend equipment life.
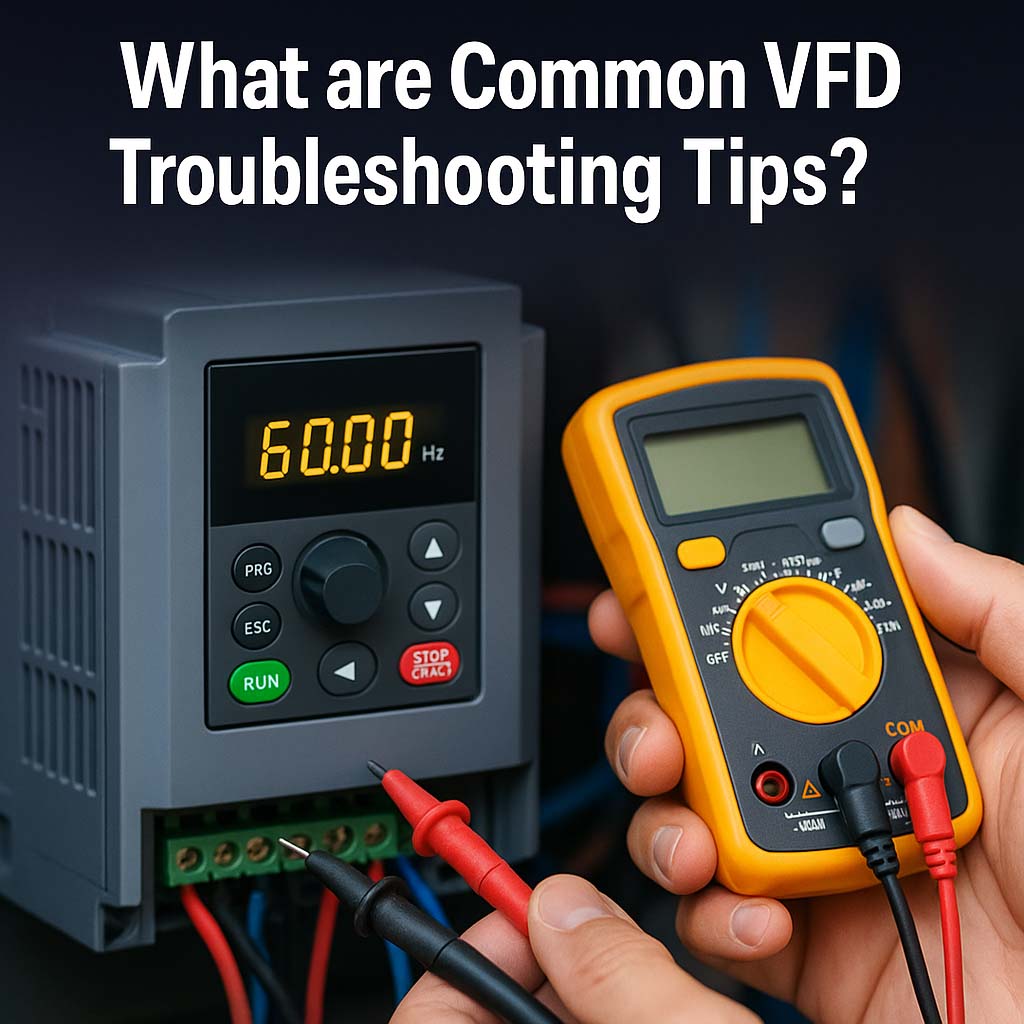
Understanding how to diagnose and solve common VFD problems is a key skill for engineers, technicians, and maintenance teams. This article provides practical, technical, and easy-to-understand insights on how to identify and fix VFD-related issues.
Why Do VFDs Fail?
Before we jump into the VFD troubleshooting tips, it’s crucial to know why VFDs fail in the first place. Most issues arise due to poor installation, harsh environmental conditions, incorrect programming, or lack of maintenance.
Some common causes include:
- Overvoltage and undervoltage
- Ground faults
- Overheating
- Motor overloads
- EMI (Electromagnetic Interference)
- Loose connections
- Harmonics and electrical noise
By understanding the root causes, you can apply effective troubleshooting techniques.
Know more about Top 15 Variable Frequency Drive Manufacturers
Basic VFD Troubleshooting Tips for Beginners
If your VFD isn’t working as expected, start with the basics. These VFD troubleshooting tips apply to most models and situations.
1. Check the Power Supply
Always begin by verifying the incoming power supply. Use a multimeter to check for proper voltage levels at the input terminals. If the voltage is too low or too high, the VFD may trip or fail to start.
Ensure all three phases are present and balanced. An imbalance greater than 2% can cause heating and eventual damage.
2. Inspect the Display Panel
Modern VFDs have user-friendly display panels. The display shows alarms, fault codes, and status messages. Check if the VFD is in fault mode or if an alarm has triggered.
Each manufacturer provides a fault code reference in the manual. Decode the error and take action accordingly.
3. Listen for Unusual Noises
Buzzing, whining, or clicking sounds could indicate issues with the internal fan, relay, or capacitors. If you hear anything abnormal, turn off the unit and inspect internal components.
Always ensure power is disconnected before opening the VFD.
Intermediate VFD Troubleshooting Tips
If basic checks don’t solve the problem, move to intermediate diagnostics. These involve more technical steps but remain accessible for most field engineers.
4. Test the Output Voltage
Using a digital multimeter, check the output voltage of the VFD when the motor is supposed to run. Compare the reading with the programmed frequency and expected voltage. An abnormal value could point to issues with the output IGBTs (Insulated Gate Bipolar Transistors) or internal circuitry.
If the VFD shows output frequency but there’s no output voltage, the output stage may be damaged.
Know more about Introduction to PLC and Industrial Automation
5. Inspect Motor Connections
Loose or corroded connections between the VFD and the motor can cause voltage drops, arcing, or motor failure. Tighten all terminals and look for signs of overheating or discoloration.
Also, confirm that the motor leads are connected to the correct VFD terminals (U, V, W). Reversed phases can cause the motor to spin in the wrong direction.
6. Monitor Ambient Temperature
VFDs are sensitive to temperature. If installed in hot, dusty environments without ventilation, the internal components can overheat. Check the heatsink and cooling fans regularly. Clean out dust buildup, especially in industrial sites.
Set the VFD’s thermal protection parameters correctly. Most drives have built-in sensors that shut down the unit if temperatures exceed safe limits.
Advanced VFD Troubleshooting Tips for Professionals
More complex problems may require advanced diagnostics. These VFD troubleshooting tips require experience and sometimes special tools.
7. Use Oscilloscope for Waveform Analysis
Harmonic distortion or irregular switching can only be identified using an oscilloscope. Analyze the output waveform for spikes, noise, or missing pulses. Distorted waveforms usually indicate faulty switching devices or EMI issues.
If available, use a power quality analyzer to measure THD (Total Harmonic Distortion). High THD can damage sensitive equipment connected to the same bus.
Know more about Contact Resistance Test IEC Standard
8. Evaluate Parameter Settings
Misconfigured parameters are a silent killer. If the acceleration or deceleration time is too short, it can stress the motor and the drive. Check motor control mode (V/F, sensorless vector, or closed loop) and ensure it matches the application.
Also, confirm that:
- Motor rated current, voltage, and frequency are correctly entered
- PID settings are tuned (for pressure or flow control applications)
- Restart or catch-on-the-fly features are set if power outages are common
9. Check for Ground Faults
Ground faults can occur due to damaged motor insulation or wet connections. Use a megger or insulation resistance tester to evaluate the resistance between each motor terminal and ground. It should be greater than 1 mega-ohm.
If the insulation is weak, replace the motor or repair the cables.
Know more about Secondary Injection Test Procedure Step by Step
Common VFD Alarms and Fault Codes
Below is a quick reference table for common VFD fault codes and what they typically mean.
Fault Code | Description | Probable Cause | Action |
---|---|---|---|
F001 | Overvoltage | Power spikes or regen energy | Install brake resistor or line reactor |
F002 | Undervoltage | Supply drop or loose terminal | Check input voltage and wiring |
F003 | Overcurrent | Sudden load or short circuit | Inspect motor and cable |
F004 | Overtemperature | Fan failure or poor ventilation | Clean filters, improve airflow |
F005 | Output Phase Loss | Open motor phase or bad contactor | Check motor cable |
F006 | Ground Fault | Damaged insulation | Test insulation resistance |
F007 | Internal Fault | IGBT failure or board malfunction | Contact service center |
Refer to your VFD’s user manual for model-specific codes.
Preventive Maintenance Tips for VFD Longevity
Apart from troubleshooting, preventive care plays a big role in keeping your VFD healthy. Follow these habits:
- Keep the VFD enclosure clean and free from dust
- Maintain proper spacing for ventilation
- Periodically tighten control and power terminals
- Replace cooling fans every 2 to 3 years if used continuously
- Schedule thermal imaging to identify hot spots
- Monitor log history to identify repeating faults
A well-maintained VFD rarely fails without warning.
When to Call for Professional Support
While most VFD troubleshooting tips help solve common problems, some issues may be beyond your scope. If the VFD:
- Emits a burnt smell
- Has bulged capacitors
- Keeps tripping despite resets
- Shows internal board failure codes
Then it’s time to contact the OEM or a certified VFD technician. Avoid opening sealed units as it voids warranties.
Know more about Primary Injection Test Procedure Step by Step
Conclusion: Mastering VFD Troubleshooting Tips
Mastering VFD troubleshooting tips is a valuable skill in today’s automation-driven industries. From basic checks to advanced diagnostics, knowing what to look for can save hours of downtime and prevent costly failures.
Always start simple. Understand the error codes. Check the power, connections, parameters, and the environment. Use tools like multimeters, insulation testers, and oscilloscopes when needed.
Follow Us on Social:
Subscribe our Newsletter on Electrical Insights to get the latest updates in Electrical Engineering.
#VFD, #VFDTroubleshooting, #IndustrialAutomation, #ElectricalMaintenance, #MotorDrives, #VariableFrequencyDrive, #ElectricalEngineering, #ControlSystems, #AutomationTips, #TroubleshootingGuide, #VFDRepair, #VFDProblems, #VFDInstallation, #SmartDrives, #EngineeringTips