Introduction to Siemens Programmable Logic Controllers (PLC)
Understanding Siemens Programmable Logic Controllers (PLC)
Siemens programmable logic controllers (PLC) are among the most widely used automation devices in the world. They control machinery, monitor inputs and outputs, and automate processes in industries such as manufacturing, water treatment, oil and gas, and energy distribution. Siemens PLCs are known for their reliability, scalability, and integration capabilities.
Table of Contents
Table of Contents
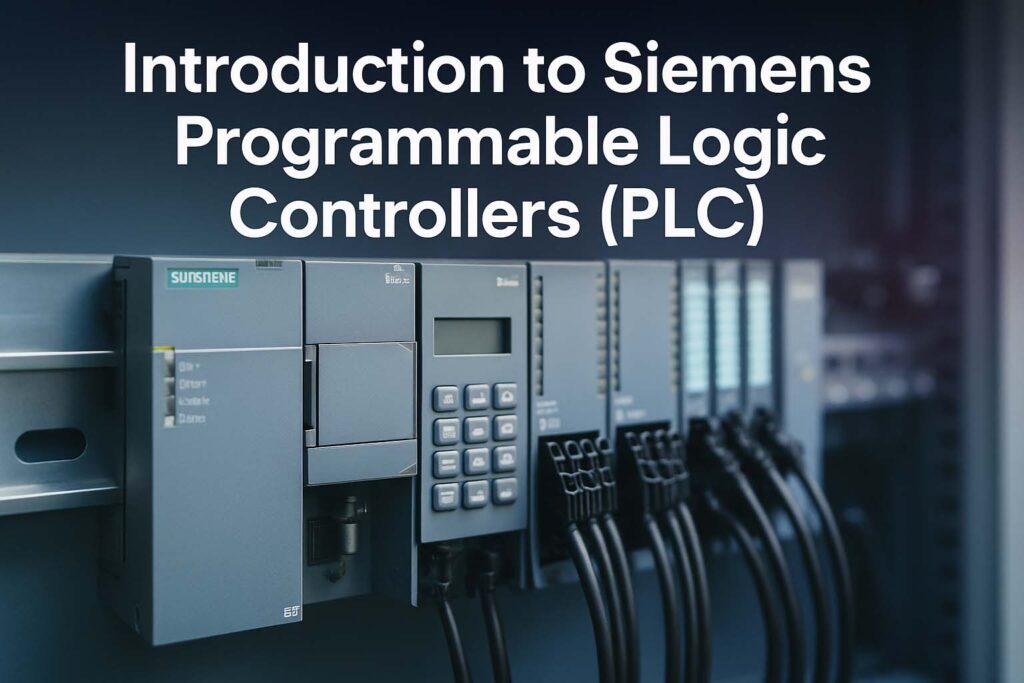
The core purpose of a PLC is to execute control programs in real-time. Siemens offers a broad range of PLC models, making them suitable for everything from small machines to large industrial plants. Their modularity and flexibility allow engineers to design custom automation systems that meet specific process needs.
What Makes Siemens Programmable Logic Controllers (PLC) Stand Out?
Siemens PLCs are built for industrial environments. They are rugged, durable, and capable of handling harsh conditions such as temperature extremes, humidity, and electrical noise. Siemens has been a pioneer in PLC technology, constantly evolving its hardware and software platforms to stay ahead of modern automation needs.
One of the key features of Siemens programmable logic controllers (PLC) is their integration with the Totally Integrated Automation (TIA) Portal. This engineering framework combines hardware configuration, programming, diagnostics, and network setup in one platform. It saves time and improves efficiency during the project lifecycle.
Know more about How Difficult Is It to Learn Programmable Logic Controller (PLC)?
Evolution of Siemens PLCs
The journey of Siemens PLCs began with the SIMATIC S5 series, which was popular in the 1980s and early 1990s. Later, Siemens introduced the SIMATIC S7 series, which became the global standard in automation.
Today, Siemens offers several S7 models, including:
PLC Model | Application Scope | Memory Size | Communication Options |
---|---|---|---|
S7-1200 | Small to mid-level automation | Up to 125 KB | PROFINET, Ethernet |
S7-1500 | Advanced automation systems | Up to several MB | PROFINET, PROFIBUS, OPC UA |
S7-300 | Legacy systems | Medium range | MPI, PROFIBUS |
S7-400 | Large process automation | High memory | PROFIBUS, Industrial Ethernet |
These PLCs offer different features but are all designed with a focus on real-time processing, modular expansion, and connectivity.
Components of Siemens Programmable Logic Controllers (PLC)
A Siemens PLC system typically includes several hardware components. Each plays a critical role in the control process.
Central Processing Unit (CPU):
The brain of the PLC. It executes logic instructions, processes data, and communicates with other devices.
Power Supply Module (PS):
It converts the AC or DC input power into a suitable format for the PLC system.
Input/Output Modules (I/O):
Input modules receive signals from sensors. Output modules send control signals to actuators like relays and motors.
Communication Modules:
Used for industrial network communication such as PROFINET, PROFIBUS, or Ethernet/IP.
Memory Cards:
These store the user program and project configuration data.
All components are modular, allowing easy customization for the desired automation application.
Know more about What is a Programmable Logic Controller (PLC) and How Does it Work?
Siemens PLC Programming Languages
Siemens programmable logic controllers (PLC) are programmed using standard IEC 61131-3 languages. The most commonly used languages include:
- Ladder Logic (LAD): Ideal for electrical engineers familiar with relay logic.
- Function Block Diagram (FBD): Graphical programming, best for logic and process control.
- Structured Text (ST): High-level text-based language for advanced control logic.
- Sequential Function Chart (SFC): Best suited for process or step-wise operations.
The TIA Portal supports all these programming languages and offers a powerful editor for code management, simulation, and testing.
Key Features of Siemens Programmable Logic Controllers (PLC)
Siemens PLCs are packed with features that enhance performance and system integration. Some of the standout features include:
- High-speed processing: Ideal for time-critical automation.
- Integrated safety functions: In models like S7-1500F, ensuring compliance with safety standards.
- Advanced diagnostics: Easy troubleshooting with built-in diagnostic tools.
- Web server access: For remote monitoring and control.
- Scalable I/O architecture: From a few to thousands of I/O points.
- Real-time data logging: Valuable for data-driven decision-making.
These features make Siemens PLCs suitable for Industry 4.0 and smart manufacturing environments.
Applications of Siemens Programmable Logic Controllers (PLC)
Siemens PLCs are used across various industries due to their versatility and performance. Some common application areas include:
- Factory automation: Packaging lines, assembly operations, and conveyor systems.
- Water and wastewater: Pump control, level monitoring, and chemical dosing.
- Building automation: HVAC control, lighting systems, and access management.
- Power plants: Generator management, turbine control, and protection systems.
- Oil and gas: Drilling operations, pipeline monitoring, and SCADA systems.
The combination of robust hardware and advanced software tools allows seamless deployment in mission-critical operations.
Know more about Top 10 Electric Motor Manufacturers in the World
Advantages of Siemens PLCs in Modern Automation
There are several reasons why Siemens programmable logic controllers (PLC) are preferred in modern automation:
Modularity and Scalability:
Engineers can build from small systems and scale as needed without replacing core components.
Reliable Communication Protocols:
Support for PROFINET, PROFIBUS, Modbus, and OPC UA ensures easy device integration.
Strong Support Ecosystem:
Siemens provides extensive documentation, training programs, and a large global network of automation experts.
Future-Ready Architecture:
With integrated cloud connectivity and Industrial IoT (IIoT) support, Siemens PLCs are prepared for digital transformation.
Secure Operations:
Built-in security features like role-based access and encrypted communication help in cybersecurity.
Know more about What are Common VFD Troubleshooting Tips?
Siemens PLCs vs. Other Brands
While there are other big names in the PLC market such as Allen-Bradley, Mitsubishi, and Schneider Electric, Siemens stands out for its:
- Unified engineering platform (TIA Portal)
- Industry-grade durability
- Wide range of automation components
- Strong focus on process industries
Here’s a quick comparison table:
Feature | Siemens PLC | Allen-Bradley | Mitsubishi |
---|---|---|---|
Programming Platform | TIA Portal | Studio 5000 | GX Works |
Scalability | High | Medium | Medium |
Global Support | Excellent | Good | Moderate |
Communication Options | Extensive | Good | Good |
Ease of Integration | Seamless with Siemens ecosystem | Limited outside Rockwell | Moderate |
This makes Siemens a preferred choice for large-scale, complex, and future-oriented projects.
Siemens PLC Troubleshooting and Maintenance
Maintaining a Siemens PLC system is relatively simple. The TIA Portal provides diagnostic features like:
- Online monitoring of variables
- Diagnostic buffer analysis
- Tag force and modify capabilities
In case of faults, users can identify problems quickly through hardware diagnostics or use the integrated web server to access logs and system status remotely. Siemens also offers firmware updates and technical support to keep systems up to date and secure.
Know more about IEC Standard for Differential Protection
Final Thoughts on Siemens Programmable Logic Controllers (PLC)
Siemens programmable logic controllers (PLC) are an essential part of today’s industrial automation. They combine performance, flexibility, and ease of use, making them suitable for both simple and highly complex tasks.
Whether you’re automating a small machine or managing a large factory, Siemens PLCs provide a scalable and future-ready solution. With powerful software like TIA Portal, engineers can reduce development time, minimize errors, and improve plant uptime.
Follow Us on Social:
Subscribe our Newsletter on Electrical Insights to get the latest updates in Electrical Engineering.
#SiemensPLC, #ProgrammableLogicController, #IndustrialAutomation, #PLCProgramming, #AutomationEngineering, #SiemensAutomation, #PLCSystems, #IndustrialControl, #AutomationSolutions, #EngineeringEducation, #FactoryAutomation, #ElectricalEngineering, #PLCTraining, #ControlSystems, #SmartManufacturing