Difference Between Star Delta and DOL Starter: A Comprehensive Guide
Understanding motor starters is crucial in electrical engineering, especially when dealing with induction motors. Two common methods for starting these motors are Direct-On-Line (DOL) starting and Star-Delta starting. Both techniques have their advantages and disadvantages, making them suitable for different applications. This article provides a detailed comparison, focusing on the difference between star delta and DOL starter, to help you make informed decisions for your specific needs.
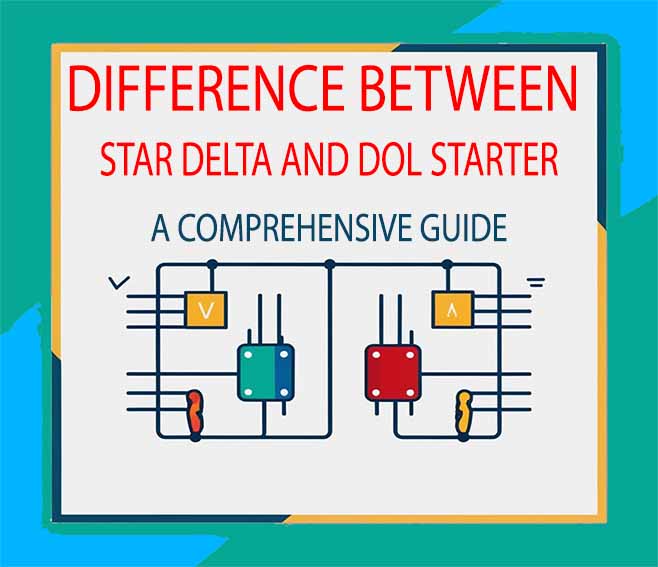
Table of Contents
Table of Contents
Understanding Direct-On-Line (DOL) Starters
A Direct-On-Line (DOL) starter is the simplest method for starting a three-phase induction motor. As the name suggests, it connects the motor directly to the power supply. This means the motor receives the full line voltage from the moment it starts.
How DOL Starters Work
In a DOL starter, a contactor acts as an on-off switch, connecting the motor directly to the power source. When the start button is pressed, the contactor closes, and the motor receives full voltage. A thermal or electronic overload relay is often included to protect the motor from overloads.
Advantages of DOL Starters
Simplicity: DOL starters are simple to design, install, and maintain, making them a cost-effective option.
Low Cost: They are relatively inexpensive compared to other starting methods because they require fewer component.
High Starting Torque: DOL starters provide maximum starting torque, which is beneficial for applications requiring high initial force.
Easy to Use: Operating a DOL starter is straightforward, requiring minimal training.
Disadvantages of DOL Starters
High Starting Current: The most significant drawback is the high inrush current, which can be 6-8 times the motor’s rated current. This can cause voltage dips and stress on the power supply system.
Limited to Smaller Motors: Due to the high starting current, DOL starters are typically used for motors up to 7.5 kW. Larger motors can cause excessive voltage drops.
Mechanical Stress: The high starting torque can cause mechanical stress on the motor and driven equipment.
Not Suitable for High Inertia Loads: Motors with high inertia loads, like centrifugal blowers, can draw very high starting currents, making DOL starters unsuitable.
Exploring Star-Delta Starters
A Star Delta starter is a reduced voltage starting method used to mitigate the high inrush current associated with DOL starting. It involves starting the motor with a star connection, then switching to a delta connection once the motor reaches a certain speed.
How Star-Delta Starters Work
Initially, the motor windings are connected in a star configuration. This reduces the voltage applied to each winding to 57.7% (1/√3) of the line voltage. As a result, the starting current and torque are reduced to one-third of what they would be in a DOL start. Learn more about how does star delta starter reduces starting current here.
Once the motor accelerates to near its rated speed (typically around 80%), the starter switches the connections to a delta configuration, applying full voltage to the windings. This transition usually happens automatically via a timer. Learn more about Star Delta Starter Diagram with Timer. Contactors are used to switch between star and delta connections.
Advantages of Star-Delta Starters
Reduced Starting Current: The primary advantage is the reduction in starting current, typically to about one-third of the DOL starting current.
Lower Voltage Dips: Reduced starting current minimizes voltage dips in the power supply, which is particularly important in areas with weak grids.
Suitable for Larger Motors: Star-delta starters can be used for motors larger than those typically started with DOL starters.
Reduced Thermal Stress: Lower starting current reduces thermal stress on motor windings, potentially extending motor life.
Disadvantages of Star-Delta Starters
Reduced Starting Torque: The starting torque is reduced to one-third of the DOL starting torque, which may not be sufficient for all applications.
Complex Wiring: Star-delta starters require more complex wiring and control circuitry compared to DOL starters.
Higher Cost: The additional components increase the cost of star-delta starters.
Torque Surge: During the transition from star to delta, there can be a brief torque surge and a momentary current peak if not timed correctly.
Unsuitable for Loaded Starts: Star-delta starting is best suited for applications where the motor starts without a load. It’s useful when a clutched gearbox is used.
Key Difference Between Star Delta and DOL Starter: A Detailed Comparison
To summarize, the core difference between star delta and DOL starter lies in their approach to managing starting current and torque. Here’s a comparative overview:
Feature | DOL Starter | Star-Delta Starter |
---|---|---|
Starting Current | High (6-8 times rated current) | Reduced (1/3 of DOL current) |
Starting Torque | High (Full rated torque) | Reduced (1/3 of DOL torque) |
Motor Size | Typically up to 7.5 kW | Suitable for larger motors |
Complexity | Simple | More Complex |
Cost | Low | Higher |
Application | Suitable for small motors and applications needing high starting torque | Suitable for larger motors and applications with reduced load requirements during startup |
Voltage Dip | Can cause significant voltage dips | Minimizes voltage dips |
Wiring | Simple Wiring Diagram | Complex Wiring Diagram |
The difference between star delta and DOL starter significantly impacts their application. DOL starters are favored for smaller motors needing high initial torque, while star-delta starters are preferred for larger motors to reduce stress on the electrical grid.
Applications of DOL and Star-Delta Starters
DOL Starter Applications
DOL starters are commonly used in applications such as:
- Small pumps
- Fans
- Conveyors
- Compressors
These applications typically involve motors that do not require reduced starting torque and are of a size that can tolerate the high inrush current.
Star-Delta Starter Applications
Star-delta starters find their use in applications where reducing the starting current is crucial, such as:
- Large pumps
- Large fans
- Compressors
- Centrifugal blowers
- Applications with unloaded start requirements
They’re especially beneficial when voltage dips need to be minimized, and thermal stress on the motor windings has to be reduced.
Related Posts:
Follow Us on Social:
Subscribe our Newsletter on Electrical Insights to get the latest updates in Electrical Engineering.
#StarDeltaStarter, #DOLStarter, #MotorStarters, #StarDeltaVsDOL, #ElectricalEngineering, #MotorControl, #DOLStarterDiagram, #StarDeltaWorking, #IndustrialAutomation, #ElectricalCircuits, #MotorStarterComparison, #StarDeltaAdvantages, #DOLStarterAdvantages, #ControlCircuit, #EngineeringTips