Top 30 Buck Converter Interview Questions: Best Guide
It’s a pleasure to welcome you to this thorough discussion of “buck converter interview questions.” A buck converter is a key part of power electronics and is frequently used for energy conversion and voltage management in a variety of applications. It’s crucial for engineers and other experts in this industry to comprehend the unique characteristics of buck converters.
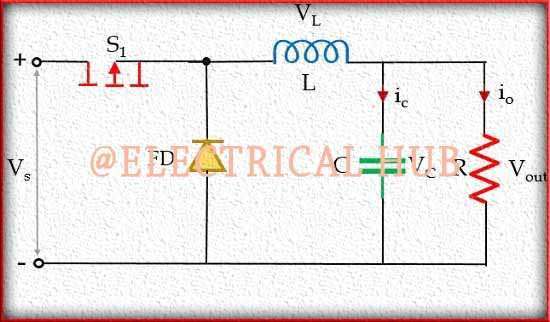
Table of Contents
In-depth buck converter interview questions will be covered in this discussion, shedding light on both the theoretical and practical aspects. These questions will be a useful tool for anyone wishing to learn more about buck converters as well as for interviewers who need to evaluate prospects. So let’s explore the fundamental concepts related to buck converter interview questions.
Top 30 Buck Converter Interview Questions
What is a synchronous rectifier in a buck converter, and how does it improve efficiency compared to a diode rectifier?
A synchronous rectifier uses active switches (typically MOSFETs) instead of diodes for rectification in a buck converter. It improves efficiency by reducing conduction losses. The rectification efficiency (η) can be calculated as
η = Vo / Vin
where Vo is the output voltage, and Vin is the input voltage.
Explain the concept of sub-harmonic oscillations in buck converters and methods to mitigate them.
Sub-harmonic oscillations are unwanted voltage spikes or ringing during transitions in buck converters. Mitigation techniques include adding a snubber circuit, adjusting control loop parameters, or modifying the compensation network.
How does parasitic capacitance affect buck converter performance, and what techniques can be used to minimize its impact?
Parasitic capacitance can cause voltage spikes and affect transient response. Techniques to minimize its impact include minimizing PCB trace lengths, using low-ESR capacitors, and careful layout design.
Describe the impact of the dead time in a buck converter on switching losses and control loop stability.
Dead time prevents shoot-through in synchronous buck converters but increases switching losses. It should be carefully set to avoid instability and maintain efficient operation.
What are the advantages and disadvantages of using current sensing techniques (e.g., current shunt resistor, inductor DCR) in buck converter control?
Current sensing provides accurate control but introduces additional losses. The current through an inductor (IL) can be measured using a current shunt resistor, and losses P(loss) can be calculated as
P(loss) = IL^2 * R
Can you explain the concept of voltage feedforward control in buck converters and its benefits in transient response?
Voltage feedforward control adjusts the duty cycle based on input voltage changes to improve transient response. It helps maintain output voltage stability during load or input changes.
How does the choice of inductor core material (e.g., powdered iron, ferrite) impact the performance of a buck converter?
The inductor core material affects inductance and losses. Ferrite cores offer high inductance but may have higher core losses, while powdered iron cores provide lower core losses but lower inductance.
Discuss the challenges and solutions related to thermal management in high-power buck converters.
High-power buck converters generate heat. Thermal management involves proper heatsinking, airflow, and component selection. The power dissipation (P_diss) in a component can be calculated using
P_diss = I^2 * R.
What is the role of the input filter in a buck converter, and how do you design it to minimize conducted EMI?
The input filter reduces high-frequency noise. To minimize EMI, select filter components (inductor and capacitor) based on the switching frequency and conduct EMI limits.
Explain the concept of inductor saturation in buck converters and its consequences on efficiency and performance.
Inductor saturation occurs when the core reaches its magnetic limits, causing increased current and reduced efficiency. The inductance (L) of an inductor can be calculated as
L = N^2 * µ * A / l
where N is the number of turns, µ is the permeability of the core material, A is the cross-sectional area, and l is the length of the core.
How can you achieve voltage tracking or multiphase operation in buck converters, and what are the advantages of doing so?
Voltage tracking involves paralleling multiple buck converters to share the load. Multiphase operation improves load sharing and reduces output ripple. The output voltage (Vo) of each phase can be equalized using interleaved operation.
Discuss the use of advanced control techniques like predictive control or fuzzy logic control in buck converters.
Advanced control techniques improve transient response and efficiency. Predictive control uses predictive algorithms to anticipate changes, while fuzzy logic control employs fuzzy sets and rules to adjust the control signal.
What is the impact of output capacitance equivalent series resistance (ESR) on voltage ripple in a buck converter?
Output capacitance ESR can cause increased voltage ripple. The voltage ripple (ΔV) can be calculated as
ΔV = IL / (C * f * ESR)
where “IL” is the load current, C is the output capacitance, f is the switching frequency, and ESR is the equivalent series resistance.
Can you describe the operation of a hysteretic control mode in buck converters and its trade-offs compared to voltage or current mode control?
Hysteretic control adjusts the duty cycle based on the difference between the actual and desired output voltage. It offers a faster transient response but can introduce a higher output ripple.
How does the choice of switching topology (e.g., synchronous buck, non-synchronous buck) affect efficiency and design complexity?
Synchronous buck converters offer higher efficiency but are more complex due to the need for synchronous rectifiers. Non-synchronous buck converters are simpler but less efficient.
Explain the concept of burst mode operation in buck converters and when it is typically used.
Burst mode operation reduces switching frequency at light loads to improve efficiency. It is typically used in battery-powered applications to extend battery life.
Discuss the limitations and advantages of using GaN (Gallium Nitride) or SiC (Silicon Carbide) devices in high-frequency buck converters.
GaN and SiC devices offer higher switching frequencies and reduced losses but may have higher component costs. They are ideal for applications where high-frequency operation is crucial.
What is the role of output voltage feedback compensation in improving the transient response of buck converters?
Output voltage feedback compensation adjusts the control signal based on output voltage errors, enhancing transient response and reducing overshoot.
How can you mitigate the impact of input voltage spikes and transients on buck converter operation?
Input voltage spikes can be reduced using input filters or transient voltage suppressors (TVS diodes). Properly designed snubber circuits can also help dampen transients.
Describe the challenges associated with designing a buck converter for automotive applications, including cold-crank conditions.
Automotive buck converters must operate reliably under harsh conditions, including cold-crank start-ups. This requires careful component selection for wide temperature ranges and robust protection mechanisms.
Can you explain the concept of multi-objective optimization in buck converter design and its relevance in achieving conflicting design goals?
Multi-objective optimization considers multiple design goals, such as efficiency, cost, and size, simultaneously. It helps balance conflicting requirements to achieve the best overall design.
Discuss the trade-offs between using fixed-frequency and variable-frequency control schemes in buck converters.
Fixed-frequency control simplifies design but may not adapt well to varying load conditions. Variable-frequency control offers better efficiency under varying loads but can introduce additional complexity.
How do you calculate and control the output voltage overshoot during load transients in buck converters?
Output voltage overshoot can be calculated using control loop transfer functions. Control techniques like feedforward control or adaptive compensation can help mitigate overshoot.
What are the considerations when designing a buck converter for battery-powered applications with strict energy efficiency requirements?
Battery-powered buck converters should minimize quiescent current, maximize efficiency, and provide power-saving modes when the load is light.
Explain the concept of digital control and digital signal processing (DSP) in advanced buck converter designs.
Digital control uses microcontrollers or DSPs to implement advanced control algorithms, enabling precise regulation and adaptability to changing conditions.
What are the advantages of using soft-switching techniques (e.g., ZVS, ZCS) in buck converters, and how are they implemented?
Soft-switching techniques reduce switching losses and EMI. Zero Voltage Switching (ZVS) and Zero Current Switching (ZCS) are achieved by manipulating the timing of switch transitions.
Describe the role of adaptive voltage positioning (AVP) and adaptive dead time control in improving buck converter efficiency.
AVP adjusts the output voltage based on load conditions, while adaptive dead time control optimizes dead time to minimize switching losses, both contributing to higher efficiency.
How does the choice of input filter components (inductor and capacitor) impact the overall EMI performance of a buck converter?
Proper selection of input filter components reduces conducted EMI. A high-quality differential mode choke and low ESR input capacitor can help achieve EMI compliance and increase EMI performance.
Discuss the challenges and techniques for achieving high-efficiency buck converters at extremely low output voltages, such as for sub-millivolt applications.
Achieving high efficiency at low output voltages requires minimizing voltage drops, optimizing component selection, and employing low-resistance switches and inductors.
Can you explain the concept of dynamic voltage scaling (DVS) in buck converters and its significance in modern power management systems?
DVS dynamically adjusts the output voltage to optimize power consumption based on load conditions, enhancing energy efficiency in portable devices and IoT applications.
Finally, it should be noted that the area of “buck converter interview questions” is an important part of the larger subject of power electronics and electrical engineering. These types of questions include a range of topics, such as control tactics, efficiency improvement, component choice, and design issues.
Candidates can demonstrate their knowledge of buck converters and interviewers can get a thorough evaluation of their qualifications by knowing the answers to these questions. The knowledge offered by these questions is essential, whether you are preparing for a job interview or just want to learn more about buck converters.
An in-depth knowledge of buck converter interview questions is helpful in getting a highly wanted job in the industry of power electronics as the demand for effective power conversion solutions rises.
Follow us on LinkedIn”Electrical Insights” to get the latest updates in Electrical Engineering. You can also Follow us on LinkedIn and Facebook to see our latest posts on Electrical Engineering Topics.
Worth Read Posts