Thermal Imaging in Electrical Preventive Maintenance: Step by Step
Thermal imaging in electrical preventive maintenance is a powerful diagnostic tool used to detect problems before they become serious. It works by capturing infrared radiation emitted by electrical components. This radiation is then translated into thermal images that help technicians identify hot spots, loose connections, overloaded circuits, and deteriorating equipment. By doing this regularly, companies can avoid unexpected failures and downtime.
Table of Contents
Table of Contents
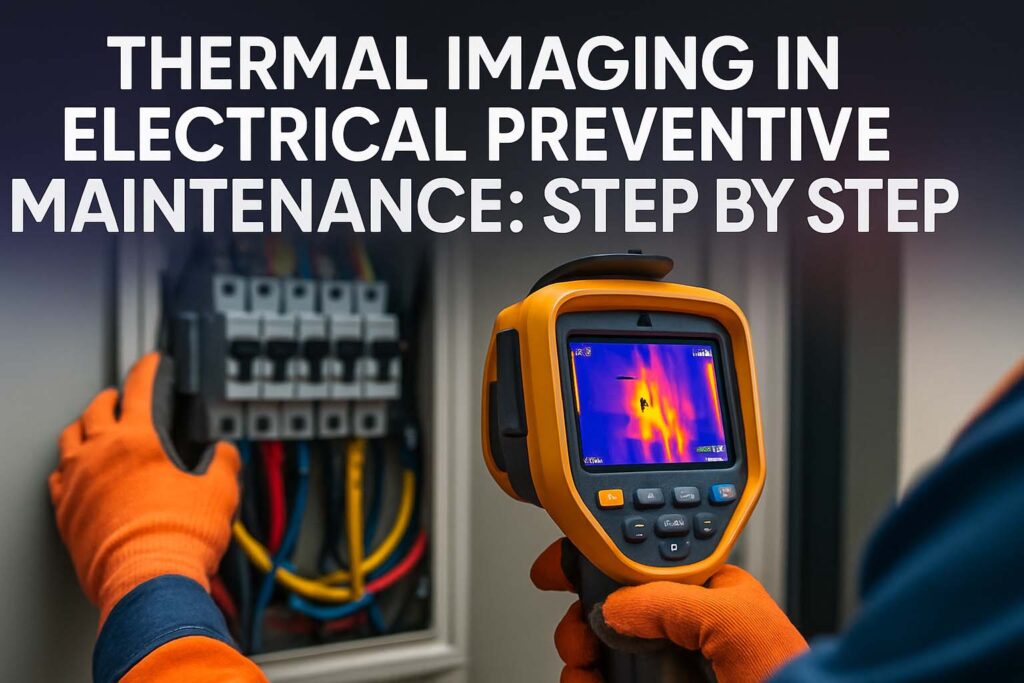
This technique has become a standard in the electrical industry. It is non-invasive, cost-effective, and highly accurate. It allows maintenance teams to carry out inspections without shutting down systems. This improves safety and efficiency, especially in commercial and industrial setups.
Why Thermal Imaging is Vital for Electrical Systems
Electrical systems generate heat as a natural byproduct of current flow. However, abnormal heat levels usually indicate a problem. If left unchecked, this heat can lead to equipment damage, fire hazards, or power outages. Thermal imaging helps in early detection of these issues.
Here are some common faults detected by thermal imaging:
- Loose or corroded connections
- Overloaded breakers
- Faulty fuses
- Imbalanced loads
- Insulation failure
Know more about Earth Ground Testing: Clamp Meter vs Fall-of-Potential Method
Thermal imaging in electrical preventive maintenance provides a visual map of temperature variations. This helps in pinpointing exactly where an issue exists. The earlier these problems are found, the easier and cheaper they are to fix.
How Thermal Imaging Works in Preventive Maintenance
The technology behind thermal imaging is based on infrared thermography. All objects emit infrared energy based on their temperature. Thermal cameras capture this invisible radiation and convert it into a visible image.
Different temperatures show up as different colors on the thermal image. Usually, red and white indicate hotter areas, while blue and green show cooler regions. These variations help technicians identify electrical problems that the naked eye can’t see.
Step-by-Step Guide to Thermal Imaging in Electrical Preventive Maintenance
Step 1: Planning the Inspection
Before beginning, it’s crucial to identify the electrical systems that require inspection. This includes panels, switchboards, transformers, motor control centers, and circuit breakers. Prioritize equipment based on load, location, and history of faults.
Create an inspection checklist. Record the nameplate data, load conditions, and ambient temperature. These details help in accurate thermal evaluation. It’s best to conduct the inspection under normal operating conditions, as this reveals real-time performance.
Step 2: Safety First
Safety should never be compromised. Only trained and authorized personnel should operate thermal cameras near live electrical equipment. Ensure proper PPE (Personal Protective Equipment) is used. This includes arc-rated clothing, insulated gloves, and face shields.
If the equipment is in an enclosed panel, ensure it’s designed for IR inspection or has an IR window. Never open live equipment unless it’s safe and permitted by safety protocols.
Know more about Insulation Resistance Testing: Step-by-Step Process
Step 3: Capturing Thermal Images
Use a calibrated and well-maintained thermal camera. Start scanning each component gradually. Keep the camera at a consistent angle and distance. Try to avoid reflections or bright light that may affect image quality.
Focus on key areas such as bus bars, terminals, contactors, relays, fuses, and transformers. Compare readings across phases to identify imbalance or anomalies. Take multiple images if necessary, including wide shots and close-ups.
Always label each thermal image with the component name, date, time, and ambient conditions. This will help during data analysis and future comparisons.
Step 4: Analyzing the Images
Once the images are captured, transfer them to analysis software for a detailed review. Modern thermal cameras usually come with analysis tools. Look for temperature differences that exceed the acceptable thresholds.
Here is a typical temperature difference guideline:
Temperature Rise Above Normal | Condition |
---|---|
0–10°C | Normal |
10–20°C | Monitor closely |
20–40°C | Schedule corrective action soon |
Over 40°C | Immediate attention required |
Compare these readings with previous inspections. If the same component shows rising temperatures over time, it may indicate progressive deterioration.
Step 5: Generating a Report
A well-documented report is essential for decision-making. Include thermal images with visual photos, temperature readings, and a clear explanation of the findings. Mention the possible cause and severity of each hotspot.
The report should also include recommendations for corrective action. This may involve tightening connections, load balancing, equipment replacement, or further investigation. Share the report with the maintenance and safety teams for immediate planning.
You might want to know Best Megger Testers for Industrial Use (2025)
Benefits of Thermal Imaging in Electrical Preventive Maintenance
Thermal imaging offers multiple advantages in maintenance planning. It provides visual proof of problems, which helps in faster decision-making. Since it is a non-contact method, inspections can be done without disturbing operations.
Some major benefits include:
- Reducing unplanned downtime
- Improving equipment life
- Enhancing energy efficiency
- Ensuring personnel safety
- Preventing costly repairs or replacements
Companies that integrate thermal imaging into their preventive maintenance programs often report fewer breakdowns and better overall asset management.
Common Tools and Equipment for Thermal Inspections
To carry out effective thermal imaging in electrical preventive maintenance, some essential tools are required:
Tool | Purpose |
---|---|
Thermal camera | Captures infrared images |
IR windows | Safe scanning without opening panels |
Clamp meters | Cross-checking load current |
PPE (gloves, face shield, etc.) | Ensures safety during inspection |
Thermal analysis software | Detailed examination and reporting |
Ensure the thermal camera has a good resolution (minimum 160×120), adjustable emissivity, and data storage capabilities. Advanced models also allow real-time video capture and wireless data sharing.
Learn more about IEC Standard for Differential Protection
Real-World Applications
Thermal imaging is used across various industries, including power plants, manufacturing units, hospitals, data centers, and commercial buildings. It helps detect faults in:
- LV/MV panels
- UPS systems
- Server racks
- Switchgears
- Capacitor banks
- Battery banks
Even in residential buildings, thermal scans can detect poor wiring or overloaded circuits. Regular inspection helps avoid fire hazards and ensures compliance with safety standards.
Best Practices for Long-Term Maintenance Strategy
To get the most from thermal imaging in electrical preventive maintenance, adopt a long-term strategy. Schedule routine inspections, preferably bi-annually or quarterly, depending on equipment criticality.
Maintain a thermal history log for each asset. This helps track performance trends over time. Update maintenance teams with proper training on interpreting thermal images.
Also, integrate thermal inspections with other tests like insulation resistance, power quality monitoring, and vibration analysis. This holistic approach provides a complete picture of equipment health.
Learn more about IEC Standard for Distribution Transformer
Final Thoughts on Thermal Imaging in Electrical Preventive Maintenance
Thermal imaging in electrical preventive maintenance is more than just a technical tool. It’s a smart investment in safety, reliability, and cost control. By detecting invisible problems early, it saves time and resources.
Following a structured, step-by-step process ensures consistent and accurate results. With thermal technology evolving, future inspections will become even more precise and automated.
Follow Us on Social:
Subscribe our Newsletter on Electrical Insights to get the latest updates in Electrical Engineering.
#ThermalImaging, #ElectricalMaintenance, #PreventiveMaintenance, #InfraredInspection, #ElectricalSafety, #PredictiveMaintenance, #ThermalCamera, #MaintenanceTips, #EnergyAudit, #FacilityManagement, #ThermalScanning, #ElectricalInspection, #PowerSystems, #IndustrialSafety, #InfraredTechnology