Insulation Resistance Testing: Step-by-Step Process
What is Insulation Resistance Testing?
Insulation Resistance Testing is a fundamental process in electrical maintenance. It helps check the quality of insulation in cables, motors, transformers, switchgear, and other electrical equipment. By applying a DC voltage, the test measures the resistance between conductive parts and ground. This test helps detect insulation breakdowns that could lead to electrical failures, equipment damage, or even fires.
Table of Contents
Table of Contents
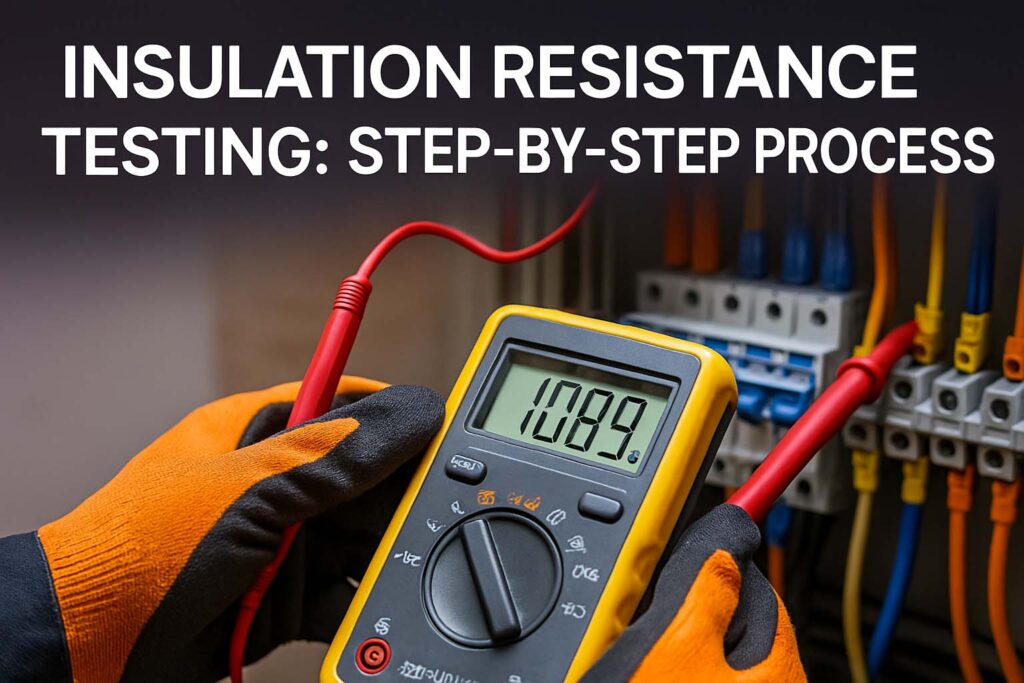
Electrical insulation degrades over time due to moisture, heat, dust, mechanical damage, and aging. Insulation Resistance Testing helps detect early signs of degradation so that corrective actions can be taken before breakdowns occur.
Why is Insulation Resistance Testing Important?
Insulation resistance is directly linked to electrical safety and equipment reliability. High insulation resistance indicates good insulation, while low resistance values indicate leakage currents or faults. This test prevents:
- Equipment failure
- Short circuits
- Fire hazards
- Electrical shocks
- Downtime in critical operations
Regular insulation resistance tests are part of predictive and preventive maintenance programs. They are performed during commissioning, scheduled shutdowns, or before energizing any new electrical installation.
Principle of Insulation Resistance Testing
The principle is simple. A known DC voltage is applied across insulation. The resulting current is measured. Using Ohm’s Law (R = V/I), the insulation resistance is calculated in ohms, kilohms (kΩ), megohms (MΩ), or even gigohms (GΩ) for high-quality insulation.
Common insulation testers, also known as Megger testers, use test voltages of 250V, 500V, 1000V, or higher depending on the application. The higher the insulation resistance, the better the insulation condition.
Know more about Best Megger Testers for Industrial Use (2025)
Step-by-Step Process of Insulation Resistance Testing
Insulation Resistance Testing must be carried out carefully. Safety precautions and standard procedures ensure accuracy and avoid equipment damage.
Step 1: Preparation Before Testing
- De-energize the equipment completely.
- Confirm the absence of voltage using a multimeter or voltage tester.
- Discharge all stored energy from capacitors or windings.
- Visually inspect cables or equipment for visible damage or moisture.
- Identify the test points (e.g., conductor to ground, phase to phase).
Tip: Label the terminals or wires before disconnection. This avoids confusion after testing.
Step 2: Selecting the Test Instrument
Choose an insulation resistance tester (Megger) that suits your voltage rating and application. For low-voltage systems, 500V or 1000V testers are ideal. For high-voltage motors and transformers, 2500V or 5000V testers are used.
Ensure the tester is calibrated and batteries are fully charged. Instruments should comply with IEC standards and safety categories (CAT III or CAT IV).
Know more about Grounding vs Bonding
Step 3: Connecting the Test Leads
Connect the leads as per the manual. Typically:
- Connect Line (L) to the conductor under test.
- Connect Earth (E) or Guard to the equipment body or ground.
- If using a Guard terminal, it should bypass leakage through surface contamination.
Proper contact is important. Use clean terminals and firm connections.
Step 4: Applying Test Voltage
Apply the test voltage by pressing the “Test” or “Start” button. Hold it for at least 1 minute. This duration allows any capacitive charging currents to decay, and gives a stable resistance reading.
Important: Do not touch the equipment under test during voltage application. Keep away until it is fully discharged.
Step 5: Reading and Recording the Values
Note the insulation resistance shown on the display. Values are usually in MΩ. Compare the reading with manufacturer recommendations or industry standards.
If the reading is less than 1 MΩ for most low-voltage systems, it could indicate degraded insulation. High-voltage systems often require readings of 100 MΩ or more.
Know more about Earthing Transformer Working Principle
Keep a record of:
- Test voltage
- Measured resistance
- Test duration
- Temperature and humidity (if significant)
- Equipment name and date
Step 6: Discharging the Equipment
After the test, the equipment may retain residual charge. Press the discharge button (if available) or wait for automatic discharge. For safety, manually discharge using an insulated discharge rod before touching.
Step 7: Analyzing and Interpreting Results
Compare the result with baseline readings or expected standards. If the insulation resistance is significantly lower than previous records, it could be a sign of:
- Moisture ingress
- Surface contamination
- Insulation aging
- Mechanical damage
In such cases, drying, cleaning, or insulation replacement may be required.
Know more about IEC Standard for Differential Protection
Common Insulation Resistance Testing Standards
Equipment Type | Test Voltage (DC) | Minimum Resistance |
---|---|---|
Low Voltage Circuits | 500V | ≥ 1 MΩ |
440V Motors | 500V | ≥ 1 MΩ |
11kV Transformers | 1000V–2500V | ≥ 100 MΩ |
High Voltage Cables | 5000V | ≥ 1000 MΩ |
Generators | 1000V–5000V | ≥ 10 MΩ per kV |
Always consult equipment datasheets or IEEE/IEC standards for exact values.
Factors Affecting Insulation Resistance Values
Several conditions can affect the test result:
- Temperature: Higher temperature lowers insulation resistance. Use correction charts.
- Humidity: Moisture lowers resistance. Test in dry conditions if possible.
- Length of Cable: Longer cables show lower resistance due to more surface area.
- Age of Equipment: Older equipment may naturally show lower resistance.
- Contamination: Dust, oil, or salt deposits can cause surface leakage.
Insulation Resistance Testing of Motors
For motors, insulation is tested between windings and between windings and ground. The testing should be done before startup, after long storage, or during annual maintenance.
For better analysis, Polarization Index (PI) and Dielectric Absorption Ratio (DAR) are used. These involve measuring resistance at intervals (usually at 1 minute and 10 minutes).
PI = Resistance at 10 minutes / Resistance at 1 minute
PI > 2 indicates good insulation. PI < 1.5 may need attention.
Know more about IEC Standard for Distribution Transformer
Safety Precautions During Testing
- Always de-energize before testing
- Use properly rated instruments and probes
- Keep unauthorized persons away from the test zone
- Discharge before and after test
- Use PPE if required
- Never test live equipment with insulation tester
Conclusion: Importance of Insulation Resistance Testing
Insulation Resistance Testing is not just a formality. It is essential to ensure operational safety and equipment health. Electrical faults due to insulation breakdown can be dangerous and costly. A simple insulation resistance test can reveal hidden issues before they turn into disasters.
By understanding the step-by-step process of Insulation Resistance Testing, technicians can diagnose problems early, ensure compliance with standards, and extend the life of electrical systems.
Follow Us on Social:
Subscribe our Newsletter on Electrical Insights to get the latest updates in Electrical Engineering.
#InsulationResistanceTesting, #ElectricalTesting, #IRTesting, #MeggerTest, #ElectricalSafety, #PreventiveMaintenance, #ElectricalEngineering, #HighVoltageTesting, #TestAndMeasurement, #DielectricTesting, #InsulationTest, #PowerSystemTesting, #IndustrialMaintenance, #StepByStepTesting, #ElectricalInspection