Wind Turbine Charge Controller: Important Guide
A wind turbine charge controller is a crucial component in wind energy systems that ensures safe and efficient battery charging. This comprehensive guide explores everything you need to know about these essential devices that protect and optimize your wind power setup.
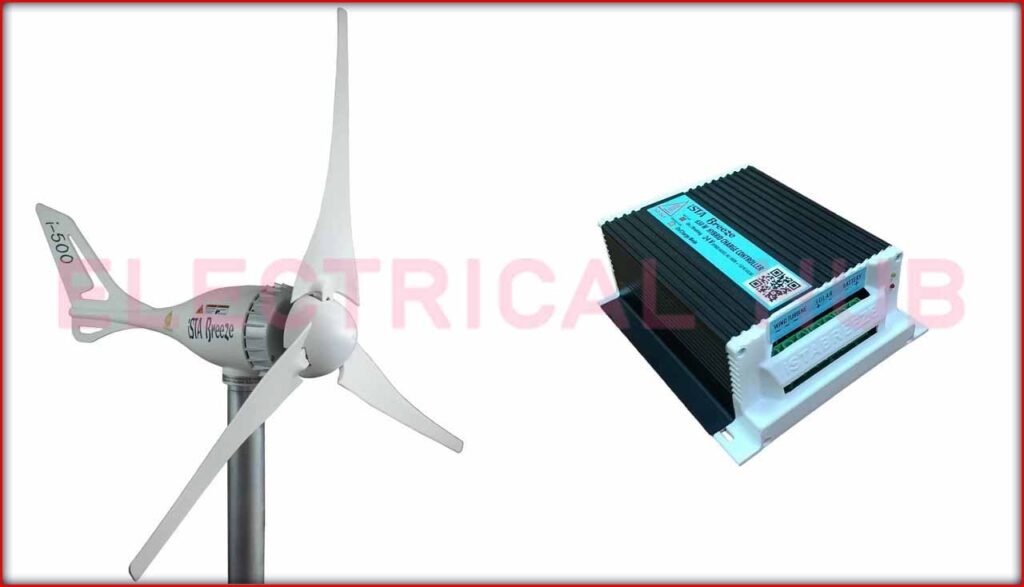
Understanding Wind Turbine Charge Controller: The Heart of Wind Energy Systems
Wind turbine charge controllers serve as the brain of wind power systems, managing the electrical output from your wind turbine to safely charge batteries while preventing overcharging and damage. These sophisticated devices optimize energy harvest from varying wind conditions and protect your investment in renewable energy equipment.
Wind turbine charge controllers operate on complex electrical principles to manage the unpredictable nature of wind-generated power. These intelligent devices handle the challenging task of converting variable AC power from wind turbines into stable DC output suitable for battery charging and grid integration.
How Wind Turbine Charge Controllers Transform Raw Power into Usable Energy
The primary function of a wind turbine charge controller is converting the variable AC power generated by wind turbines into regulated DC power suitable for battery charging. When wind speeds fluctuate, the controller maintains stable voltage output, ensuring your batteries receive the right charging current regardless of weather conditions.
Modern wind turbine charge controllers employ advanced microprocessors that continuously monitor battery voltage, charging current, and wind conditions. This intelligent management system adjusts charging parameters in real-time, maximizing energy capture while preventing battery damage from overcharging or excessive current.
Fundamental Components of Wind Turbine Charge Controllers
The internal architecture of a wind turbine charge controller consists of several sophisticated components working in harmony. The primary components include a rectifier circuit that converts AC to DC, power monitoring sensors, microprocessor control units, and solid-state switching devices. Advanced models incorporate MOSFET transistors or IGBT modules for efficient power handling and precise control.
Modern controllers employ sophisticated algorithms that continuously analyze input parameters including voltage, current, wind speed, and battery state of charge. This real-time monitoring enables dynamic adjustments to maximize power harvest while ensuring system protection.
Choosing the Right Wind Turbine Charge Controller for Your System
Selecting an appropriate charge controller depends largely on your system voltage and power requirements. The most common wind turbine charge controller configurations are available in 12V, 24V, and 48V variants, each suited for different applications and system sizes.
12V Wind Turbine Charge Controllers: Perfect for Small-Scale Applications
A 12V wind turbine charge controller is ideal for small wind energy systems, typically handling power outputs up to 400 watts. These controllers are perfect for remote cabins, boats, or small off-grid applications. Their simplicity and reliability make them a popular choice for beginners in wind energy.
The 12V controllers often feature basic but essential protection functions, including over-voltage protection, short-circuit protection, and reverse polarity protection. Many models include LED indicators showing battery status and charging conditions, making system monitoring straightforward for users.
- Input voltage range: 0-50V AC (wild voltage from turbine)
- Maximum input current: 0-40A
- Charging regulation points: 13.8V (float) to 14.4V (bulk)
- Temperature compensation: -30mV/°C
24V Wind Turbine Charge Controllers: The Mid-Range Power Solution
Moving up in capacity, 24V wind turbine charge controllers handle medium-sized systems generating between 400 to 1000 watts. These controllers offer improved efficiency compared to 12V systems, with reduced power losses in transmission. They’re commonly used in residential wind power systems and larger off-grid applications.
The 24V controllers typically incorporate more advanced features, such as temperature compensation and multiple charging stages, ensuring optimal battery maintenance and longevity. Many units also provide data logging capabilities, allowing users to track system performance over time.
- Input voltage range: 0-100V AC
- Maximum input current: 0-60A
- Charging regulation points: 27.6V (float) to 28.8V (bulk)
- Power handling capacity: 400W to 1500W
48V Wind Turbine Charge Controllers: Powering Large-Scale Operations
For larger wind energy systems, 48V wind turbine charge controllers handle power outputs exceeding 1000 watts. These high-capacity controllers are essential for industrial applications, large residential systems, or commercial wind farms. The higher voltage reduces current flow, minimizing wire size requirements and power losses.
Professional-grade 48V controllers often include sophisticated monitoring systems, remote access capabilities, and advanced protection features. They’re designed for maximum efficiency and reliability in demanding applications where consistent power output is crucial.
- Input voltage range: 0-200V AC
- Maximum input current: 0-100A
- Charging regulation points: 55.2V (float) to 57.6V (bulk)
- Power handling capacity: 1000W to 5000W
Advanced Features: Wind Turbine Charge Controllers with Dump Load
A particularly important feature in modern wind turbine charge controllers is dump load management. When batteries reach full charge and excess power is generated, the controller diverts energy to a dump load, preventing system damage from over-voltage conditions.
The dump load, typically a resistive heating element, converts excess electrical energy into heat, which can be used for water heating or space heating. This feature ensures continuous turbine operation even when batteries are fully charged, protecting the wind turbine from potential damage caused by free-spinning in high winds.
Smart dump load controllers automatically engage when needed, maintaining optimal system balance. Some advanced models even allow programmable thresholds and can prioritize different loads based on system conditions, maximizing energy utilization.
Technical specifications for dump load systems typically include:
- Dump load resistance matching to turbine output
- Programmable voltage thresholds for load engagement
- PWM-based load modulation for precise control
- Temperature monitoring of dump load elements
- Automatic load distribution algorithms
Protection Systems and Safety Features
Modern wind turbine charge controllers incorporate multiple layers of protection:
Overvoltage Protection:
- Primary overvoltage cutoff
- Secondary surge protection devices
- Transient voltage suppression
Short Circuit Protection:
- Fast-acting electronic circuit breakers
- Current limiting circuits
- Automatic system recovery features
Temperature Protection:
- Thermal sensors throughout critical components
- Automatic shutdown at high temperatures
- Temperature-compensated charging parameters
Integration and System Optimization
Modern wind turbine charge controllers often feature hybrid capabilities, allowing integration with solar panels and other renewable energy sources. This integration provides more stable power output and improved system reliability. Many controllers include built-in MPPT (Maximum Power Point Tracking) technology, optimizing power harvest across varying wind conditions.
The latest controllers also offer smart monitoring capabilities through mobile apps or web interfaces, providing real-time data on system performance, battery status, and energy production. This connectivity enables remote system management and predictive maintenance, ensuring optimal performance and longevity.
Maintaining Your Wind Turbine Charge Controller
Regular maintenance of your wind turbine charge controller ensures long-term reliability and optimal performance. While these devices are generally robust, periodic inspection of connections, cooling systems, and parameter settings is essential. Modern controllers often include self-diagnostic features that alert users to potential issues before they become serious problems.
Regular firmware updates, when available, can improve controller performance and add new features. Keep ventilation paths clear and ensure proper grounding connections remain intact. Most quality controllers include surge protection, but additional lightning protection measures may be necessary in areas prone to electrical storms.
Through proper selection, installation, and maintenance of your wind turbine charge controller, you can ensure efficient, reliable operation of your wind energy system for years to come. Whether you’re using a basic 12V system or a sophisticated 48V setup with dump load management, understanding your controller’s capabilities and requirements is key to maximizing your renewable energy investment.
Worth Read Posts
- Wind Energy
- Smart Grid
- Wind Turbine Design Ideas
- What Are 555 Timers
- DL2450 vs CR2450
- Fading and Attenuation
- CR2032 vs CR2450
- CR2450N Battery
- CR2450 Battery Equivalent
Follow us on LinkedIn, “Electrical Insights,” to get the latest updates on Electrical Engineering.