Partial Discharge Testing in HV Equipment: A Practical Guide
Partial discharge testing in HV equipment is one of the most critical diagnostic tools in modern power systems. It helps identify insulation defects that could lead to catastrophic failures. As the demand for reliable high-voltage (HV) power infrastructure grows, understanding how to conduct effective partial discharge (PD) testing is no longer optional—it’s essential.
Table of Contents
Table of Contents
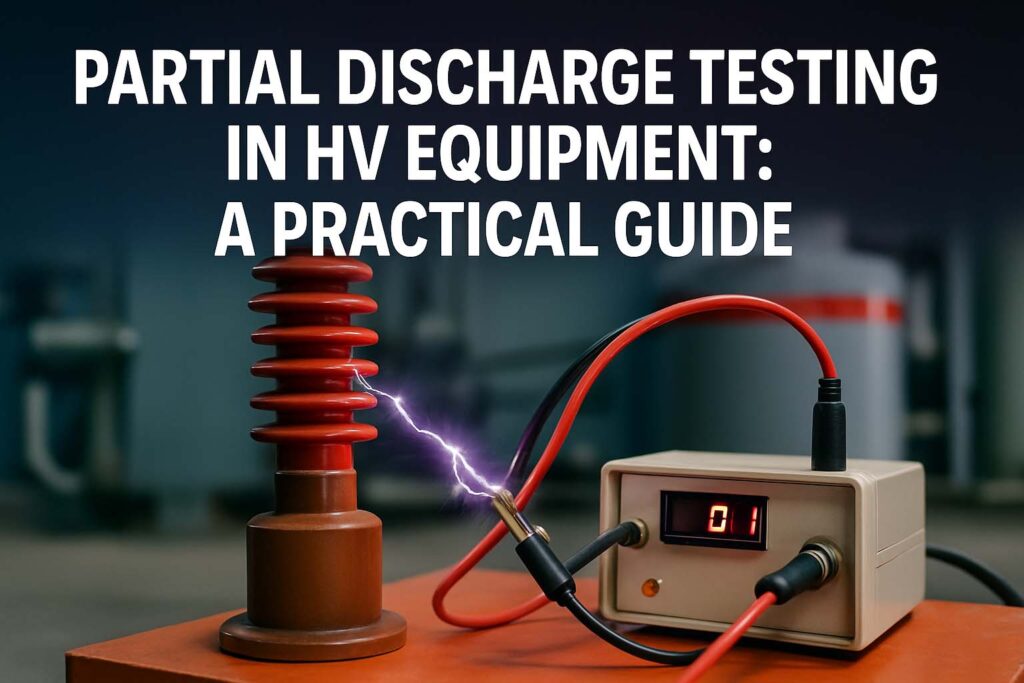
This guide provides a practical, engineer-friendly explanation of how partial discharge testing works, why it’s important, how it’s done, and what results mean. Whether you’re an asset manager, field engineer, or testing contractor, this guide will help you master the essentials.
What is Partial Discharge Testing in HV Equipment?
Partial discharge is a localized electrical discharge that does not completely bridge the insulation between conductors. In simple terms, it’s a tiny spark inside insulation material. Over time, this spark erodes the insulation, leading to equipment failure. This can happen in transformers, switchgear, cables, bushings, and even rotating machines.
Partial discharge testing in HV equipment is the process of detecting, measuring, and analyzing these discharges. By detecting PD early, engineers can prevent unexpected breakdowns, extend equipment life, and reduce maintenance costs.
Why is Partial Discharge Testing in HV Equipment So Important?
Partial discharges are silent killers. They rarely trip protection relays or show up in routine visual inspections. However, they cause cumulative damage that leads to insulation breakdown. This can trigger unplanned outages, expensive replacements, and even dangerous fires or explosions.
Here are some key benefits of PD testing in HV equipment:
- Early Fault Detection: Identifies insulation defects long before failure.
- Improved Asset Life: Helps plan timely maintenance or refurbishment.
- Operational Safety: Reduces risk of catastrophic failures in critical HV assets.
- Cost Optimization: Avoids unnecessary shutdowns and emergency repairs.
Know more about Insulation Resistance Testing
How Partial Discharge Develops in High Voltage Systems
Partial discharges occur due to defects in insulation. These defects can be internal (within solid insulation), surface-based (tracking along insulation surfaces), or external (caused by bad connections or contamination).
Common causes include:
- Voids in insulation during manufacturing
- Improper cable terminations
- Moisture ingress in bushings or joints
- Mechanical damage during installation
As discharges continue, they generate heat, ozone, and even sound or light. Eventually, they create carbonized paths through insulation, reducing its dielectric strength and leading to full breakdown.
Types of Partial Discharge in HV Equipment
There are several types of partial discharges, each associated with different insulation defects. Here’s a table summarizing the key types:
Type of Partial Discharge | Description | Typical Equipment Affected |
---|---|---|
Internal Discharge | Occurs in voids or gas pockets within solid insulation | Power transformers, XLPE cables |
Surface Discharge | Takes place along the surface of insulation | Cable joints, bushings |
Corona Discharge | Happens in air near sharp edges or loose connectors | Switchgear, open terminals |
Treeing | Branch-like electrical discharges forming in solid insulation | XLPE cables, epoxy resin systems |
Know more about Best Megger Testers for Industrial Use (2025)
Partial Discharge Testing Methods in HV Equipment
There are multiple ways to test for partial discharge depending on the equipment type and application. Each method offers different insights.
Offline PD Testing
This method requires removing the equipment from service. A test voltage is applied, and PD is measured under controlled conditions.
Pros:
- Accurate and detailed results
- Suitable for factory acceptance tests
Cons:
- Requires shutdown
- Time-consuming and costly for field testing
Online PD Testing
In this method, PD is measured while the equipment remains energized. It’s ideal for condition monitoring in live substations or power plants.
Pros:
- No shutdown required
- Continuous or periodic monitoring possible
Cons:
- Requires signal separation from background noise
- Less precise than offline testing
Know more about Circuit Breaker Timing Test Procedure
Common Testing Techniques
Technique | Application | Signal Detected |
---|---|---|
Ultrasonic Testing | Switchgear, cables | Acoustic waves |
UHF Detection | GIS, transformers | Electromagnetic pulses |
HFCT (High-Frequency Current Transformer) | Cable terminations | Discharge currents |
TEV (Transient Earth Voltage) | Metal-clad switchgear | Surface voltage pulses |
Steps for Conducting Partial Discharge Testing in HV Equipment
Here’s a simplified step-by-step approach to PD testing:
1. Equipment Preparation
- Isolate equipment if doing offline testing
- Clean and inspect all terminals
- Ensure proper grounding and safety measures
2. Sensor Installation
- Install ultrasonic, TEV, or HFCT sensors as applicable
- For UHF tests, use appropriate antenna or couplers
3. Signal Acquisition
- Connect sensors to a data acquisition unit
- Record background noise level before energizing
- Apply test voltage if offline, or record during live operation
4. Data Analysis
- Identify the PD pulse patterns
- Compare pulse magnitude, repetition rate, and phase-resolved patterns
- Use time-domain or frequency-domain analysis tools
Know more about Primary Injection Test Procedure Step by Step
5. Reporting and Recommendations
- Classify PD activity levels (Low, Medium, High)
- Suggest corrective action: immediate repair, scheduled maintenance, or continued monitoring
PD Interpretation: What Do The Results Mean?
Interpreting PD results isn’t always straightforward. A high PD level doesn’t always mean failure is imminent, but it does warrant attention.
Here’s a typical severity classification:
PD Magnitude (pC) | Condition | Recommended Action |
---|---|---|
< 100 | Normal | Routine monitoring |
100 – 500 | Moderate | Detailed inspection advised |
> 500 | Critical | Immediate maintenance needed |
Modern PD analyzers also offer PRPD (Phase Resolved Partial Discharge) plots, helping to pinpoint the discharge location and type.
Partial Discharge Testing in HV Cables
XLPE cables are particularly susceptible to PD due to manufacturing voids, poor terminations, or thermal aging. PD testing can be done during commissioning or periodically during operation.
Technicians typically use VLF (Very Low Frequency) testing combined with PD measurements. This approach is safer for cable insulation and effective at detecting early-stage defects.
Know more about How to Use Megger Insulation Tester MIT2500
Partial Discharge Testing in Transformers
Transformers are critical HV assets. PD in windings or bushings can cause sudden insulation failure. UHF sensors and acoustic emission methods are commonly used for PD detection.
Online PD monitoring is often installed permanently in large power transformers. It offers real-time alerts and trending, which helps asset managers plan timely interventions.
Challenges in Partial Discharge Testing in HV Equipment
While PD testing is powerful, it has some challenges:
- Noise Interference: In substations, external noise can mask actual PD signals.
- Sensor Placement: Improper sensor location may result in missed signals.
- Skill Requirements: Data interpretation requires expertise in PD patterns.
Despite these challenges, partial discharge testing remains a valuable tool when integrated with other diagnostic methods like tan delta testing, insulation resistance, and thermal imaging.
Future of Partial Discharge Testing in HV Equipment
The future of PD testing lies in AI-powered diagnostic systems. These systems will use machine learning algorithms to analyze PD signals and recommend actions automatically. Integration with SCADA and asset management systems is already happening.
Portable PD testing kits are also becoming more user-friendly, allowing even smaller utilities and industrial facilities to adopt them easily.
Conclusion
Partial discharge testing in HV equipment is more than just a test—it’s a vital part of condition-based maintenance. With the growing reliance on high-voltage assets in energy systems, the need for accurate, timely, and non-invasive diagnostics will only increase.
By understanding how partial discharge works, selecting the right test method, and interpreting the data correctly, electrical engineers and technicians can drastically improve equipment reliability, reduce costs, and enhance safety.
Follow Us on Social:
Subscribe our Newsletter on Electrical Insights to get the latest updates in Electrical Engineering.
#PartialDischargeTesting, #HighVoltageTesting, #ElectricalInsulation, #PowerSystemSafety, #PDDetection, #HVTesting, #TransformerTesting, #SwitchgearMaintenance, #ConditionMonitoring, #ElectricalEngineering, #SubstationTesting, #DielectricTesting, #PreventiveMaintenance, #InsulationTesting, #PDAnalysis