PLC vs DCS: Main Differences for Industrial Automation
Industrial automation has revolutionized manufacturing and process control. Two primary systems lead this transformation—PLC (Programmable Logic Controller) and DCS (Distributed Control System). Though both are used for control and automation, their architecture, applications, and core functionalities differ significantly.
Table of Contents
Table of Contents
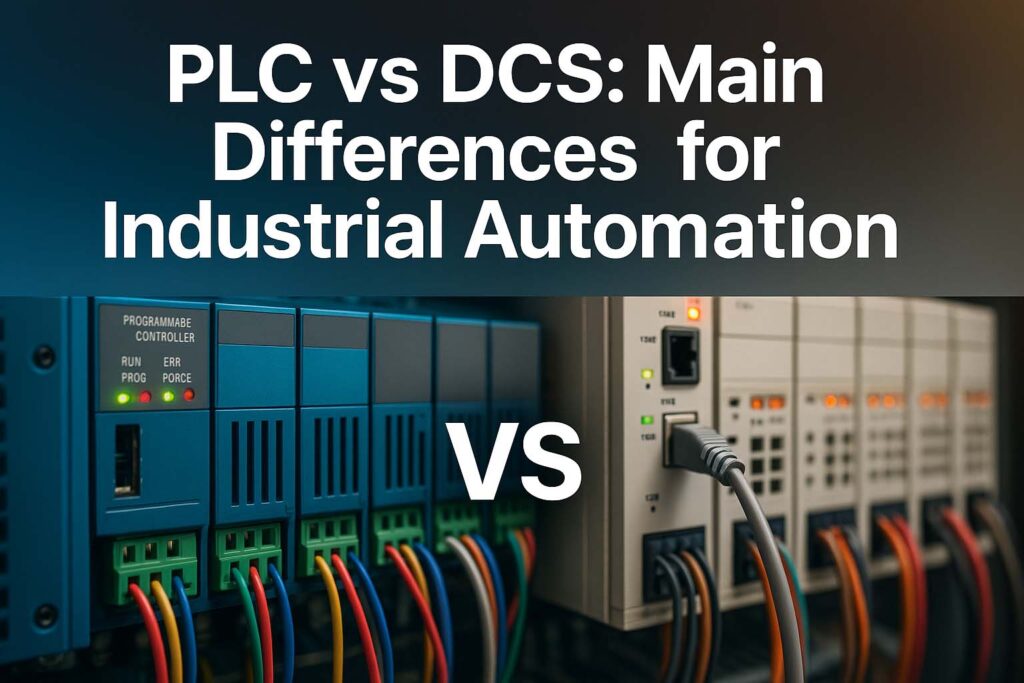
In this article, we explore the PLC vs DCS debate in depth, highlighting technical differences, practical use cases, and choosing the right system for your industrial setup.
Understanding the Basics of PLC vs DCS
Before diving into the differences, it’s essential to understand what PLCs and DCSs are and how they function in an industrial environment.
A PLC is a rugged digital computer designed for real-time control of manufacturing processes. It’s used primarily in discrete manufacturing such as packaging, bottling, or automotive assembly.
A DCS, on the other hand, is a networked control system that manages continuous and complex processes. It’s common in industries like chemical, oil & gas, power generation, and water treatment where precise process control is critical.
PLC vs DCS: Architecture and Design Philosophy
Architecture
In the PLC vs DCS comparison, architecture is the foundational difference.
PLCs follow a centralized design. A central controller communicates with input/output modules via fieldbus or industrial Ethernet. This modular design allows customization based on process requirements.
DCSs have a decentralized or distributed architecture. They consist of multiple controllers located close to process areas. Each controller manages specific parts of the process and communicates with a central operator station or Human Machine Interface (HMI).
Feature | PLC | DCS |
---|---|---|
Architecture | Centralized | Distributed |
Controller Location | Usually in one cabinet | Spread across plant |
Communication | Fieldbus / Ethernet | Proprietary / Standard protocols |
Know more about Best Programmable Logic Controller Manufacturers
Design Philosophy
PLCs were originally designed for replacing relay logic in discrete automation. Their focus is speed, reliability, and ease of programming for simple repetitive tasks.
DCSs were developed for managing large-scale, continuous processes. Their design is aimed at fault-tolerance, advanced process control, and scalability.
PLC vs DCS: Programming and Control Logic
Programming logic is another key area of distinction.
PLCs typically use ladder logic, function block diagrams, and structured text. These programming methods are intuitive for technicians with an electrical background. PLCs are also faster in scanning and execution, which makes them ideal for time-sensitive operations.
DCSs use more advanced and process-oriented programming such as sequential function charts and continuous function blocks. DCS programming is better suited for process industries where tuning and process optimization are ongoing.
Feature | PLC | DCS |
---|---|---|
Programming | Ladder, Function Block, Structured Text | Function Block, Sequential Charts |
Execution Speed | Faster scan cycles (10-50 ms) | Moderate scan cycles (100-500 ms) |
Control Type | Discrete, Sequential | Continuous, Regulatory |
Know more about Programmable Logic Controller Components
PLC vs DCS: Scalability and Flexibility
Scalability is crucial in modern industrial automation.
PLCs offer modular scalability. You can add I/O modules, communication cards, or even duplicate PLCs for larger systems. However, managing multiple PLCs can be complex and often requires third-party software integration.
DCSs are inherently scalable. They are designed to integrate numerous process areas through a seamless control network. With built-in data historians, redundancy, and control strategies, DCSs handle large process expansions more efficiently.
In short, PLCs are flexible, while DCSs are scalable and robust.
PLC vs DCS: Human Machine Interface (HMI)
Both systems offer HMI integration, but the capabilities and design differ.
PLCs usually rely on external SCADA systems for HMI. These SCADA systems provide real-time visualization and alarms but often require separate configuration and licensing.
DCSs come with tightly integrated HMI systems as part of their architecture. Operator stations offer centralized control, advanced diagnostics, and alarm management out of the box.
Feature | PLC with SCADA | DCS Integrated HMI |
---|---|---|
Visualization | Real-time, Customizable | Process-centric, Unified |
Alarm Handling | Basic to Advanced | Advanced with prioritization |
Historical Data | Requires additional SCADA software | Built-in data historian |
Know more about Programmable Logic Controller Types
PLC vs DCS: Maintenance and Troubleshooting
Maintaining uptime and diagnosing faults is vital in automation systems.
PLCs are easier to maintain. With simple diagnostic LEDs, modular designs, and widely available spares, technicians can quickly identify and fix issues. Many PLC brands support hot-swapping I/O modules.
DCSs have advanced diagnostic capabilities, but troubleshooting can be more complex. Due to their distributed nature, identifying the root cause often requires trained engineers and centralized diagnostic tools.
In maintenance-heavy environments, PLCs offer quicker serviceability, while DCSs offer deeper insights for predictive maintenance.
PLC vs DCS: Cost Considerations
Cost plays a huge role in system selection, especially for small and medium-scale industries.
PLCs have a lower initial cost. Their hardware is less expensive, and programming tools are often open-source or less restricted. You pay only for what you use.
DCSs have a higher upfront cost due to built-in redundancy, integrated HMI, and sophisticated control. However, for large continuous plants, this investment results in lower downtime and higher process efficiency.
Cost Factor | PLC | DCS |
---|---|---|
Initial Hardware Cost | Low | High |
Software Licensing | Per controller/SCADA module | Bundled, may include multiple features |
Expansion Cost | Low per module, but adds complexity | Scalable and integrated |
Know more about Programmable Logic Controller vs Arduino
PLC vs DCS: Industry Applications
Choosing between PLC and DCS depends on the application.
PLCs are ideal for:
- Packaging lines
- Conveyor systems
- Material handling
- Batch mixing
- Automotive assembly
DCSs are ideal for:
- Oil refineries
- Chemical plants
- Power generation
- Water treatment plants
- Pulp and paper industries
In hybrid plants where both batch and continuous processes exist, it’s common to see PLCs managing discrete tasks and DCS managing core process control.
PLC vs DCS: Integration and Communication Protocols
Both systems support various communication protocols, but with different priorities.
PLCs support open communication standards like Modbus, Profibus, EtherNet/IP, and OPC UA. Integration with third-party systems is easy, which makes PLCs a good fit in diverse hardware environments.
DCSs support both open and proprietary protocols. They focus more on secure, redundant communication, especially for safety-critical applications.
Know more about Siemens S7-1200 Programmable Logic Controller
Making the Right Choice in PLC vs DCS
The decision between PLC vs DCS is not always clear-cut. It depends on factors like:
- Type of process (discrete vs continuous)
- Number of I/O points
- Need for redundancy and uptime
- Operator interface requirements
- Budget and scale of deployment
In smaller or modular systems with fast switching operations, PLCs provide speed and affordability. In complex, critical, and continuous environments, DCS offers integrated reliability and centralized control.
Future Trends in PLC vs DCS
With Industry 4.0 on the rise, the lines between PLC and DCS are becoming blurred. Modern PLCs now come with advanced process control features, data analytics, and cloud connectivity.
Similarly, modern DCSs are adopting modular designs and supporting open protocols for better interoperability.
Emerging technologies like Edge computing, AI-based diagnostics, and cybersecurity-enhanced protocols are also influencing both PLC and DCS landscapes.
Final Thoughts on PLC vs DCS
The PLC vs DCS comparison shows that each system has its unique strengths. Your choice should be based on process complexity, scalability needs, uptime requirements, and overall control philosophy.
While PLCs offer simplicity, speed, and cost-effectiveness, DCS systems provide process integrity, advanced control strategies, and a centralized view for large-scale operations.
In many industrial environments today, a hybrid approach—using both PLC and DCS—is becoming the new standard. Understanding their roles and differences ensures better design, smoother operations, and a more productive automation setup.
Follow Us on Social:
Subscribe our Newsletter on Electrical Insights to get the latest updates in Electrical Engineering.
#PLCvsDCS, #IndustrialAutomation, #AutomationSystems, #PLCvDCSComparison, #ControlSystems, #DCSArchitecture, #PLCTechnology, #AutomationEngineering, #IndustrialControl, #SmartManufacturing, #ProcessAutomation, #FactoryAutomation, #EngineeringInsights, #AutomationTrends, #TechForIndustry