Electrical Risk Assessment Template for Factories
Electrical hazards are a serious concern in industrial environments. Factories, with their high-powered machines, wiring systems, and complex operations, are especially vulnerable. An Electrical Risk Assessment Template for Factories is a practical tool that helps identify, analyze, and control potential electrical risks before they cause damage or injury.
Table of Contents
Table of Contents
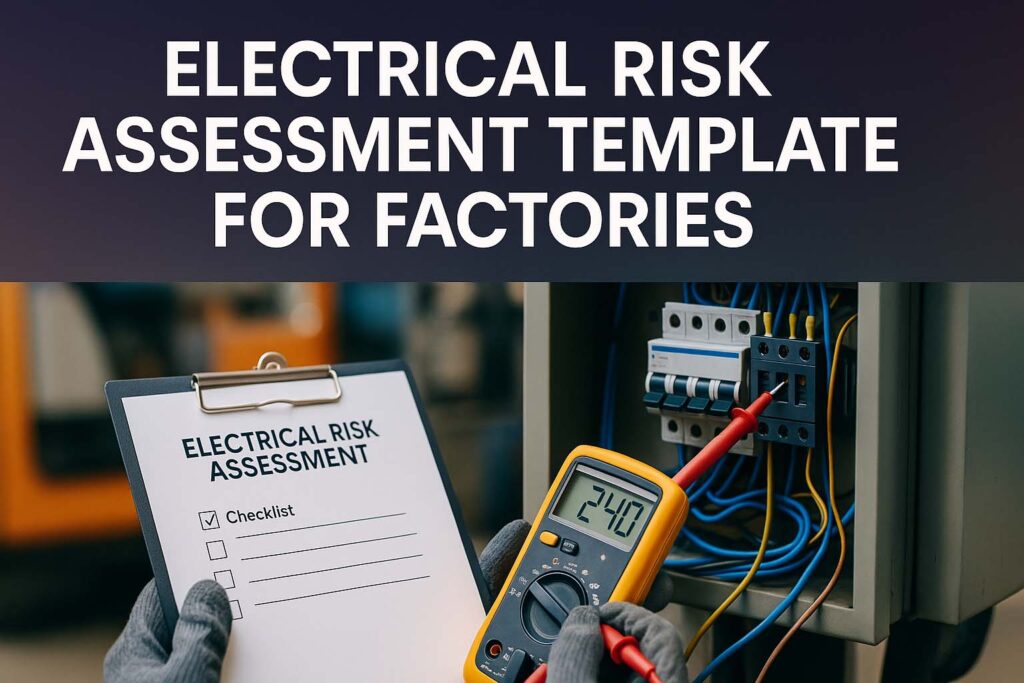
This guide explains the importance of having a proper template, what it should include, and how to implement it effectively.
Why Use an Electrical Risk Assessment Template for Factories?
Factories are filled with electrical installations—panels, motors, switchgear, transformers, and control systems. Any fault, misuse, or neglect can lead to fire, electrocution, or production loss. An Electrical Risk Assessment Template for Factories allows safety managers and engineers to carry out systematic evaluations.
Using a standardized template ensures no hazard is overlooked. It provides structure to inspections and makes compliance with health and safety laws easier. Moreover, having a documented record is essential for audits and insurance.
Know more about Best Megger Testers for Industrial Use
Key Elements of an Electrical Risk Assessment Template for Factories
A well-designed electrical risk assessment template should cover every possible hazard. It must be specific to the processes and equipment used in that factory. Below are the essential components to include:
1. General Information Section
This section includes the basics:
- Name of the assessor
- Date of assessment
- Factory name and location
- Department or area under review
- Equipment or process being evaluated
Even though this part seems simple, it sets the foundation for the rest of the report.
Know more about Insulation Resistance Testing: Step-by-Step Process
2. Hazard Identification Table
The core of any risk assessment is hazard identification. For electrical systems, hazards can be numerous. Here’s a sample table that outlines how hazards might be recorded:
Potential Hazard | Source | Who is at Risk |
---|---|---|
Electric shock | Exposed wires, live terminals | Technicians, Operators |
Arc flash | Switchgear, circuit breakers | Maintenance personnel |
Fire due to overload | Motors, panels, wiring | Entire facility |
Short circuits | Poor insulation, wet areas | Electricians, Engineers |
Tripping hazards | Loose electrical cables | All factory workers |
This table helps visualize where and how dangers might arise.
3. Risk Evaluation
Every hazard must be evaluated based on likelihood and severity. Use a risk matrix to assign a rating. Below is a sample scale:
Likelihood | Severity | Risk Rating |
---|---|---|
Rare (1) | Minor (1) | Low (1) |
Possible (2) | Moderate (2) | Medium (4) |
Likely (3) | Major (3) | High (9) |
Almost certain (4) | Critical (4) | Extreme (16) |
An Electrical Risk Assessment Template for Factories should include this matrix and apply it to each identified hazard.
Know more about Off-Grid Solar System Design Guide for Remote Areas
4. Control Measures
Once a risk is evaluated, the next step is to decide how to manage it. This section of the template explains the existing controls and what additional measures are needed. Here’s how that could look:
Hazard | Existing Controls | Additional Controls Required |
---|---|---|
Electric shock | Insulated tools, PPE, signage | Periodic inspection, GFCI sockets |
Arc flash | Arc-rated clothing, remote operation | Arc flash labels, training updates |
This makes it clear which steps are being taken and which ones still need attention.
5. Person Responsible and Timeline
Every action point should have someone responsible for it. Without accountability, safety plans often remain unexecuted.
Action | Responsible Person | Target Date |
---|---|---|
Install GFCI sockets | Electrical Supervisor | 10th August 2025 |
Add arc flash warning labels | HSE Officer | 5th August 2025 |
This step ensures proper follow-up and project completion.
6. Review and Sign-off
Once the assessment is complete, it should be reviewed by senior management or the safety officer. This final check confirms that all hazards have been addressed and that controls are acceptable.
Common Electrical Hazards in Factories
Understanding what hazards to look for is key to filling out the Electrical Risk Assessment Template for Factories. Here are some common ones seen in industrial settings:
- Overloaded circuits due to multiple machines connected to one supply
- Damaged extension leads and flexible cables
- Loose terminations in control panels
- Moisture ingress into electrical enclosures
- Improper earthing or bonding
- Use of non-certified electrical components
Each of these should be checked during the walkthrough inspection.
Know more about Grounding vs Bonding: Key Differences Explained
Legal and Safety Standards
In many countries, industrial workplaces must comply with national electrical safety regulations. For example:
- UK: Electricity at Work Regulations 1989
- USA: OSHA Electrical Standards
- EU: Low Voltage Directive, EN 60204
- Pakistan/India: Central Electricity Authority (CEA) Regulations
An Electrical Risk Assessment Template for Factories should reference these standards to ensure compliance. Using them also strengthens your case during inspections.
Electrical Risk Assessment Template for Factories in Action
Let’s look at a brief example to see how the assessment works in practice.
Scenario: A metal fabrication unit using CNC machines, welding stations, and conveyors.
Hazard Identified: Welding station has no dedicated circuit and causes frequent tripping.
Risk Level: High (Likelihood: Likely, Severity: Major)
Existing Control: Only a basic MCB in the panel
Recommended Control: Install individual circuit with 30mA RCD
Responsible: Plant Electrical Incharge
Target Completion: 1st September 2025
This real-world example shows the practical application of the template. Simple, structured, and focused on solving a problem.
Benefits of Using a Factory-Specific Template
Each factory has a unique layout, process, and machinery set. A custom Electrical Risk Assessment Template for Factories ensures the risks are specific to your plant. Benefits include:
- Improved safety culture among workers
- Fewer production delays due to electrical faults
- Better compliance with workplace regulations
- Enhanced reputation for safety and quality
- Lower insurance premiums due to reduced risk
Templates reduce guesswork. They make safety a proactive task, not a reactive burden.
Know more about Short Circuit Calculation Methods: IEC vs ANSI
Tips for Effective Use of Electrical Risk Assessment Template for Factories
To get the most value out of your risk assessment template, consider the following:
- Review it quarterly or after any major changes in equipment
- Train team members to recognize electrical hazards
- Use visual aids, such as photos of unsafe conditions
- Integrate findings into your maintenance schedule
- Involve electrical contractors in assessments during shutdowns
Remember, a risk assessment is only effective if acted upon. Keep it dynamic and regularly updated.
Final Thoughts
Electrical safety is not a one-time task. It’s a continuous effort, especially in factories where high power is part of daily operations. Having a structured Electrical Risk Assessment Template for Factories helps managers, supervisors, and engineers take control of this critical area.
Know more about Transformer Cooling Methods: ONAN, ONAF, OFAF & More
This tool makes the workplace safer, operations smoother, and compliance easier. It transforms safety from a document into a daily practice. Don’t wait for an incident to highlight gaps—build your template, train your team, and stay one step ahead of electrical risks.
Follow Us on Social:
Subscribe our Newsletter on Electrical Insights to get the latest updates in Electrical Engineering.
#ElectricalRiskAssessment, #FactorySafety, #WorkplaceRiskAssessment, #ElectricalSafety, #IndustrialSafety, #RiskAssessmentTemplate, #OSHACompliance, #FactoryMaintenance, #ElectricalHazards, #RiskManagement, #SafetyChecklist, #ElectricalInspection, #WorkplaceHealthAndSafety, #HSEStandards, #SafetyFirst